In the presence of immediate danger, safety is our first and foremost concern. However, when we do something for a very long time without incident, like driving, we can develop a sense of invulnerability, believing that nothing bad is going to happen. As our false confidence grows, so can the frequency with which we take part in risky behaviors such as texting while driving. The issue with the illusion of invulnerability is that it is an illusion; there is still potential danger all around us and the consequences of the potential danger can be extreme. What makes matters worse is that we often make up excuses to justify, and therefore continue, our risky behavior. For example, we may convince ourselves that “it was only a short text” or “the traffic was moving very slowly.” Excuses like this help to alleviate any guilt that we may have felt for doing what we know we shouldn’t have.
Over time, and with enough excuses, we may forget how dangerous our actions really are and permanently buy into our illusion, creating an unsafe habit that is extremely difficult to change. It should be evident through the examples above and through your own experience that changing personal habits can be very difficult. Now consider the challenge faced when trying to make the habits and behaviors of hundreds of people within an organization safer. Is it even possible? Many will argue that it isn’t. However, a few believe that it can be done, but only through the development of a safety culture.
“A strong safety culture is about doing the right thing all of the time, even when no one is looking.” Patrick Cantner, HSE Director, Willbros Canada.
A culture is a set of values, norms, beliefs and attitudes that are shared by a group of people. When a strong culture exists, it can have a powerful effect on the behaviors of everyone who is part of it. Many strong cultures already exist around us. Consider a church, a golf course, a prestigious country club, a nightclub or even your grandmother’s house. Think about how individual behavior adapts to each situation. What changes happen when moving from one culture to another? Behaviors are typically very different in a church than a nightclub, even for the same individual.
In organizations with a strong safety culture, safety is valued above all other things including profitability, productivity or ego. When this happens, safety rules are followed, safety conscious behavior is the norm, and individual attitudes towards safety are positive and reinforcing. People entering these organizations tend to quickly adapt or discover that they are unwelcome.
It doesn’t take long to realize when an organization has a strong safety culture. These organizations are almost fanatical about the safety of their people, and it shows in most everything they do from the way they talk, to the way they work, right through to the way they make decisions.
When discussing a tour taken of the Alberta liquor and Gaming Commission warehouse that is managed by Connect logistics, Marcia Minto, Program Manager for Government of Alberta O&S raining & education stated, “it was interesting to hear them talk and to watch how their operations function. hey integrated safety right into every piece of work that they do.” She explains that the importance placed on safety can be felt as soon as one walks in the door, and it is this feeling that helps new employees to buy into their safety culture. “They have obviously spent a considerable amount of time structuring their organization in a way that safety is number one and it’s just part of the business.”
Indicators of the importance of safety are everywhere. To get into the warehouse, one must sign in and take a jacket and a badge. The hallways to the warehouse are covered with health and safety information. “They had a board that identified – with names and pictures – who was on the health and Safety Committee. Committee minutes were posted for all employees to access. They had numerous health and safety forms readily available for staff and a suggestion box for employees to submit their feedback. They also had a large recognition board displayed with employees’ names, various health and safety bulletins, as well as a large V monitor mounted in the corner that showed health and safety related information. All these forms of health and safety communication were displayed before you even went through the warehouse door. It all sends a message that ‘we run a tight ship here and safety is important’.”
THE REALITY OF SAFETY
Many different types of safety cultures exist across organizations from the good to the bad to the ugly.
The Ugly:
In organizations with “ugly” safety cultures, no one wins. In these organizations, excuses for unsafe behaviors are plentiful.
“I forgot.”
“It will take longer.”
“It is more dangerous to wear safety gear than not as it gets in the way.”
“I’ve been doing it this way for many years and have never got hurt.”
“The low risk of falling does not justify the need to wear a harness.”
“It’ll only take a minute.”
In organizations where excuses are common, the excuses too often lead to injuries and fatalities that could have been avoided.
“I’ve investigated over 100 fatal accidents and over 300 disabling injuries in my career,” says Ted Lane, an Occupational Health and Safety Officer for Alberta Human Services. “At least 80% of the accidents that’ve investigated weren’t just preventable, they were readily preventable and the hazard that created the accident had quite often been foreseen. It had been observed but hadn’t been dealt with.”
The Bad:
In some organizations, though safety is extremely important, it is used first and foremost to protect against legal or administrative penalties, criticism or punitive damages. As a result, these employers commonly inundate workers with a barrage of policies and procedures. If they ask why they must do something, workers are told, “Just follow the rules”.
These organizations, focused on having a way to prove that they have done everything reasonably practicable should an incident occur, end up shoving safety down everyone’s throats. Over time, workers may come to view safety very negatively.
“What I’ve found over the years, especially in the Fort McMurray area, [is that] we tend to get a little whitewashed with safety,” says Darryl Chipman, Director for CASCA. “You can see [it] as soon as you switch to the safety topic. You can see the disengagement in the room and people go ‘Yeah, yeah. We know. We know. We know.’”
This situation is in sharp contrast to organizations in which safety is used first and foremost to keep their people safe. In these organizations, the employers’ attitudes and approach to safety are very different. They explain that safety is for everyone’s protection, and they are genuinely concerned with ensuring that everyone works safely and is properly trained so that no harm comes to them. This approach to safety positively impacts the attitude of workers, paving the way for a strong safety culture.
The Good:
Many individuals in organizations that do not have a strong safety culture are skeptical that such a thing exists. The reality is that these organizations do exist and that they can achieve amazing results not only in terms of safety but in productivity and profitability as well. A prime example is Alcoa Inc., the world’s leading producer of primary and fabricated aluminum.
In 1987, a new CO, Paul O’Neill, was brought into Alcoa to turn it around. O’Neill understood that a large company needs to have one focus if any dramatic change is going to take place. He needed to identify the most important priority that everyone in the company could agree upon, no one would argue, and that everyone would work together to achieve. He decided that it needed to be worker safety.
In his opening speech to investors in October 1987, he shared his new focus for the company. Reprinted with permission from The Power of Habit: Why We Do What We Do in Life and Business:
“I want to talk to you about worker safety,” he said. “Every year, numerous Alcoa workers are injured so badly that they miss a day of work. Our safety record is better than the general American workforce, especially considering that our employees work with metals that are 1500 degrees and machines that can rip a man’s arm off. But it’s not good enough. I intend to make Alcoa the safest company in America. I intend to go for zero injuries.”
“Now, before I go any further,” O’Neill said, “I want to point out the safety exits in this room.” He gestured to the rear of the ballroom. “There’s a couple of doors in the back, and in the unlikely event of a fire or other emergency, you should calmly walk out, go down the stairs to the lobby, and leave the building.”
Silence. The only noise was the hum of traffic through the windows. Safety? Fire exits? Was this a joke? One investor in the audience knew that O’Neill had been in Washington, D.C. during the sixties. Guy must have done a lot of drugs, he thought.
Eventually, someone raised a hand and asked about inventories in the aerospace division. Another asked about the company’s capital ratios.
“I’m not certain you heard me,” O’Neill said. “If you want to understand how Alcoa is doing, you need to look at our workplace safety figures. If we bring our injury rates down, it won’t be because of cheerleading or the nonsense you sometimes hear from other CEOs. It will be because the individuals at this company have agreed to become part of something important: They’ve devoted themselves to creating a habit of excellence. Safety will be an indicator that we’re making progress in changing our habits across the entire institution. That’s how we should be judged.”
The investors in the room almost stampeded out the doors when the presentation ended. One jogged to the lobby, found a pay phone, and called his twenty largest clients.
“I said, ‘The board put a crazy hippie in charge and he’s going to kill the company,’” that investor recounted. “I ordered them to sell their stock immediately, before everyone else in the room started calling their clients and telling them the same thing.”
“It was literally the worst piece of advice I gave in my entire career.”
Within a year of O’Neill’s speech, Alcoa’s profits would hit a record high. By the time O’Neill retired in 2000, the company’s annual net income was five times larger than before he arrived, and its market capitalization had risen by $27 billion. Someone who invested a million dollars in Alcoa on the day O’Neill was hired would have earned another million in dividends while he headed the company, and the value of their stock would have been five times bigger when he left. What’s more, all that growth occurred while Alcoa became one of the safest companies in the world. Before O’Neill’s arrival, almost every Alcoa plant had at least one accident per week. Once his safety plan was implemented, some facilities would go years without a single employee losing a workday due to an accident. The company’s worker injury rate fell to one-twentieth of the U.S. average.
Some people may believe that the culture O’Neill created caused managers to report fewer incidences, resulting in their improved safety numbers, but the opposite was true. In fact, when it was discovered that a gas leak in a small plant in Mexico wasn’t reported to the CO, that division’s most senior manager, a highly valued member of the executive team, was immediately let go.
THE CHALLENGE
If building a strong safety culture was easy, many organizations would have one. However, there are many challenges faced when seeking to create an effective safety culture, a significant one being that it is too easy to be unsafe.
By nature, we seek to find the easiest way to complete a task, which can make it very tempting to just get a job done without taking the time to do it safely.
Chipman recounts one story. “One of my own brothers was working for me on one job. He took an A-frame ladder and leaned it up against a trailer. When walked by said, ‘What are you doing?’ he said, ‘I’m going to tie this cable back so it’s not drooping so low.’ He was thinking of everyone’s safety, but his own. said, ‘Come off that ladder and go get the right ladder for the job’. he turned around and said, ‘I’m only going to be a minute.’ I replied, ‘I’m only going to tell you this one more time. Get off the ladder and go get the appropriate extension ladder for the job.’ he said, ‘Yeah, but I’m only going two steps up for the job. I could have already had this done [in the time we’ve been talking].’ In the meantime, I had about 5 or 6 foremen that were watching. I said, ‘Why don’t you come down and come with me to my office.’ I sat him down in my office and issued him a reprimand: one for insubordination (not listening) and one for performing unsafe activities. What explained to him during our conversation is that the company pays you to be safe; they pay you to take the time to do the job correctly. I [told him] I appreciate that you’re pulling the cable out of the way for everyone but at the same time I don’t appreciate how you were executing that activity or your attitude towards personal safety because it’s a culture that we really need to promote. When we let one guy get away with it, we might as well let the next guy get away with it.”
In this example, the supervisor intervened, and an unsafe act was prevented. However, if this supervisor wasn’t around, the unsafe act would have likely occurred.
key point to realize is that the instant a decision is made to do something unsafe, excuses are made to justify the decision such as, “I’m only going to be a minute,” or “’m only going two steps up for the job.” The moment an excuse is made is the defining moment.
Excuses can be extremely dangerous. If not immediately challenged, they may be internalized and used to justify future unsafe behavior. This inadvertently helps to build the belief that taking the time to do things safely is extra work or an unnecessary burden. his belief, which can become contagious among the members of a group, can quickly build unsafe attitudes and promote the taking of unnecessary risks.
“I see that attitude of ‘What does this have to do with me?’ or ‘I know what I’m doing’ or ‘I’ve been doing this job for a hundred years’ or ‘I just go in and do my job. Why do have to worry about that?’” said Marcia Minto, Program Manager for Government of Alberta OH&S Training/Education. “That attitude is very difficult to change.”
Soon all the hard work that has been put into building a safety culture can be lost.
THE BENEFITS
If it is extremely difficult to create a safety culture yet it can easily be destroyed, why even bother trying to create one? The benefits, the most important one being improved worker safety, far outweigh any potential challenges.
Everyone has the right to make it home safely at the end of each workday and a strong safety culture is an effective tool to help make this happen.
As Patrick Cantner, HSE Director of Willbros Canada, states: “We have seen great results in our safety culture initiatives. In 2012 we had a 54% reduction in our recordable incidents and a 41.5% reduction in our Total Recordable Incident Rate (RR) and we equate a lot of that to introducing cognitive safety culture initiatives.”
Other benefits realized through the development of a strong safety culture include good workers are easier to attract and retain while risk takers are likely to leave the organization. This not only increases overall competency levels across the organization, but it also reduces training costs incurred due to high turnover.
Dan Carter, Director of the Central Region & Control Centre for Kinder Morgan, puts it in simple terms: “If there are problems with safety and people are getting hurt, they don’t want to work for you anymore. They will leave.”
It is also important to realize that costs can be decreased, both in terms of lives and capital, through the development of a strong safety culture.
“Last year there were 22 fatal workplace accidents,” says Ted Lane. “If you work out the average cost of a fatal or disabling accident in the workplace in Alberta, it’s between 8 and 16 million dollars. This is a lot of money [and the] industry is paying for all those costs directly or indirectly. We are losing an awful lot of money. We can’t replace the money, we can’t replace the people, and we can’t replace the human costs.”
SIGNS OF A SAFETY CULTURE
If you have not been a part of an organization that has a strong safety culture, how would you know what it looks like when you see it? There are a few tell-tale signs that indicate its presence.
Tonia Sulkhova has more than 15 years of HSE experience in the oil & gas industry in North America and Europe, and her time leading several workstreams for Taliman Energy’s corporate occupation safety standards has shown her the value – and hallmarks – of a strong safety culture.
“In my career,” she says, “I worked with some difficult joint ventures between international companies and national oil and gas companies. The latter were not necessarily worried about safety per se; it’s a different mentality in some parts of the world. But saw progress from a pathological to great safety culture in these companies because everyone in the shareholder teams was asking the right questions about safety. Serious incident investigations were personally reviewed by the most senior people in the company. This sent a right message to everyone that actions would have to be implemented to prevent recurrence. Because everyone paid attention to safety, the culture gradually changed, and the joint ventures achieved quite a strong safety culture.”
While organizations like the one just mentioned demonstrate their culture by asking the right questions and ensuring incident reviews are brought to the attention of senior management, other organizations like Kiewit have other indicators–strong employee buy-in.
“Kiewit is an older company but many of the people… within the company are a fairly young group of people,” says Chipman. “The management is older, and they understand the inherent nature of a safety culture. They have achieved more sustainable buy-in, more acceptance of the rules and a shift in the perception of safety [with a change from] ‘these are the rules’ to ‘this is how to run a business,’ – they have managed to achieve fantastic buy-in from the superintendent level right down to the folks in the field.”
In line with its “Nobody gets hurt” objective, Imperial Oil’s safety culture can be identified through the development and enforcement of its safety standards.
“Imperial Oil is really setting the bar [in terms] of driving the safety culture,” says Cantner. “They have identified and defined risk tolerances associated with employee behaviors and have allocated extensive resources in creating safety standards for their company. hey absolutely walk the talk when it comes to holding contractors accountable for meeting or exceeding those standards.”
Though these are just a few indicators of the presence of a safety culture, it isn’t hard to find others, especially when you are a part of an organization that has a great culture.
THE SEVEN DEADLY SINS
There are seven things capable of singlehandedly killing a safety culture and they do not need to occur frequently to have a deadly effect; a single occurrence can start a domino effect that can wipe out all effort previously invested to build a safety culture. One of the most disconcerting parts is that some organizational leaders do them all the time without even realizing.
1. Double Standards
The use of different sets of rules depending on the situation or people involved is the most devastating of all the deadly sins. Having a set of rules that does not apply to everyone in the organization, especially management, will invite others to disregard rules, even those designed to save lives.
“I’ve seen this situation happen many times,” says Lane. “On the shop door it reads: ‘Safety glasses must be worn. Hard hats must be worn. Safety boots must be worn.’ [But] the boss walks in with none of that, because he’s the boss, so it doesn’t apply to him. If you do that, your safety won’t work. Don’t expect people to follow something that you tell them unless you do it as well. With safety, there is no ‘them’ and ‘us’. Everybody is on the same side. Everybody follows the same rules.”
2. Top-down Policy Directives
When a safety policy, procedure or process is created without input from front line workers or from the people whom the policy will affect, it can undermine the safety culture. This common mistake that managers make can cost the company dearly in terms of employee buy-in.
Sharon Cole, an OHS Consultant for Alberta Gaming and Liquor Corporation had this to say. “If you are going to write a policy or a procedure, you must involve the people that are part of the process, [those people] who call the frontline people; the experts who do it every day. If you sit in an office and write a policy about someone in the warehouse and you know nothing about that position, how can you effectively communicate a policy to them when they are the experts? So why not get them involved? Have them assist in writing the policy. I find you get more buy-in from this process.”
3. Poor Attitude
Another deadly sin when it comes to safety culture is allowing cancerous attitudes and poor performance to flourish. You have probably met people with a poor attitude toward safety. these are the people who mutter, “this is bullshit” during a safety meeting or who believe, “this doesn’t apply to me” because they have been around for so long or they have a relationship with someone high up in the company. Standing by as these poor attitudes and behaviors go unchecked can be extremely dangerous due to their infectious nature. If these attitudes and behaviors are held by someone with a strong personality, they can quickly spread like a plague and destroy an effective safety culture.
“We have to reward good safety performance,” says Lane, “and we must have zero tolerance for bad safety performance. [We] don’t care who you are in that organization or how valuable you are to it. If you can’t comply with the safety rules, sooner or later, you have got to go. I’ve heard the excuses a lot: ‘I know he is not doing it, but he’s the boss’s son’ or ‘He’s the only guy that can do that’ or whatever. None of that. Zero tolerance for bad performance and rewards for good performance. You need to show people that you appreciate those who follow the rules – that’s where you get the big cultural change.”
4. Shifting Priorities
Constantly shifting priorities is a common management sin when it comes to sustaining or building safety cultures. All too often organizations claim that safety is their top priority, but then something changes, and safety takes a back seat to other things i.e. profitability or productivity. When this happens, a powerful and lasting message is sent throughout the entire organization – safety is important, but only when it is convenient. This quickly erodes a safety culture.
5. Not Walking the Talk
When supervisors, managers or company executives say something needs to be done or done in a particular way, and then do nothing to enforce it, or worse, they do the opposite, they can quickly destroy their organization’s safety culture.
“The worst thing leaders can do is not follow the company’s safety vision,” says Canter. “In other words, if you say, ‘Production done in the absence of safety will not be valued or rewarded’ and you allow that to happen, you will destroy the safety culture.”
6. Punishing Good Behavior
Some supervisors, managers and leaders inadvertently punish the very behaviors they are hoping to see more of.
“On one job, had a guy bump into a light fixture with a zoom boom,” says Chipman. “He broke a small little cover for the light. It was about $25 to buy a new cover and 30 minutes in labour, costs to change it. He came down off the zoom boom [and] he went in and reported himself. He was given 3 days off work with no pay to sit in camp. his can cause a huge problem encouraging people not to admit their mistakes. Actions like this send a bad message throughout the organization and some people just may stop doing the right thing.”
Punishing admirable behavior or reprimanding those who point out unsafe conditions acts to destroy a safety culture.
As Marcia Minto puts it, “If someone comes forward and then gets yelled at or screamed at from the line manager, this will decrease the likelihood of them coming forward in the future. Employees want to feel empowered to do that and not feel repercussions. If you feel those repercussions, you’re not going to be empowered to stand up and say something.”
7. Complacency
Complacency is the quiet killer of safety cultures. It can sneak up on organizations, divisions, departments or teams who have been doing things right for a long time without incident. With so much success behind them, it can become easy to forget the importance of ensuring adherence to the policies and procedures that were instrumental to their success. Assumptions are made that everyone knows what needs to be done and will continue to do so in a safe manner. Overconfidence can lead to the relaxing of rules and procedures, which can trigger a subtle domino effect that becomes the undoing of a safety culture.
TIPS AND STRATEGIES
At this point, it may seem that creating and sustaining a safety culture is not only difficult – which it is – but almost impossible. I assure you that it’s not. The following are helpful and inexpensive tips and strategies for creating a strong safety culture within your organization. Depending on your organization and its current culture, some suggestions might work better than others based on your situation. The key is to identify the ones that make the most sense for your organization then implement them with consistency and determination one at a time to increase your chances of long-term lasting success.
1. Be Willing to Make Sacrifices
It is important to realize that changing a culture will be much more difficult in some organizations than in others. n extreme situations, the transition from a weak safety culture to a strong one can be a painful process but, to make the change, tough choices, sacrifices, and a lot of determination are needed. In situations like these, an organization is likely to take a step backward before it can take steps forward in a safer direction.
“[In] one of the major construction companies in Alberta that I dealt with years ago,” says Lane, “their lost time rate was going through the roof; they had some fatalities. They came and asked for help. I met with them starting with senior management all the way down to supervisors – who are a key element in effective safety – and workers. They determined that they were going to have a policy of zero tolerance, and they implemented it, and they stuck to it and they lost work because of it. They had to reduce their sales in the first year because they lost the cowboys who were working for them, and they didn’t have enough people to do the [work]. Within 3 to 4 years, they came back to where they were and bigger than where they were because they recruited the good guys, and these ones stayed even when the company was paying a little less than its competitors because they would rather be there. So, when they got back to the same level of sales, they were way more profitable because they were way more efficient, and they didn’t have the cost of all the accidents and injuries.”
2. Engage Employees
All too frequently safety policies and procedures are developed at the top of the organization and then passed down. A powerful way to improve employee engagement and compliance is to ask employees for their personal opinions, suggestions and solutions on safety related matters. If you are truly interested in their ideas and opinions, they will give them to you, and it can have a positive impact on the organization when you implement them.
“We promote the guys to do some of the things in their own way,” says Chipman. “We just recently had some safety tour paperwork that the guys typically fill out every day. We try to engage the folks in the field and one of the guys says, ‘What if we were to change it to pictures on a template and writing it up rather than just a two-page write up on the hazards that we find from that day?’ What a great idea, you have three pictures with a few sentences and then you can present that to everyone. his makes it easier to fill out the form, saves time, [it’s] easier to review and that idea came right up from the field.”
3. Encourage Candor
A key element of a strong safety culture is open, candid communication. All too often employees are either afraid to or are discouraged from speaking up when someone or something is unsafe, especially if management is involved. However, situations like these are the ones where candor is even more essential. Candid communication may initially feel uncomfortable to someone who is not used to an organizational climate where employees can be extremely blunt and forthright with anyone in the organization including any level of management, even senior ones. Though done respectfully, nothing is held back when it comes to suggestions for improving and enforcing safety.
A person from the frontline can’t approach a C-level executive and say, “John, you can never come back here without a hard hat.” It’s too much of a risk and it sends a bad message to everyone who works for you.
You need to lead by example. To achieve this level of openness, an organization requires a solid foundation of trust and respect for people at all levels. Once achieved, people are no longer afraid to openly call out issues or unsafe behaviors, regardless of the person they are speaking to.
Ted Lane’s method of assessing safety culture is practical and observation based. “I’ll go in as an inspector: I’ll be wearing my hard hat, my very scary Occupational Health & Safety jacket and [I’m usually] tailed around by a bunch of worried managers. I’ll leave something off – maybe my [ear plugs are only in] one ear or [I’m missing] my safety glasses or whatever. If some guy that is working a lathe, driving a forklift or tweaking the floor says, ‘Hey! Hey you! Get the hell out of here. You get that fixed. You can’t come in here like that!’ Guess what, that culture works.”
4. Lead By Example
Leading by example is an effective strategy for building a strong safety culture as actions speak louder than words. When leaders, managers and supervisors all set the example consistently by following policies and procedures and wearing required PPE, it sends a powerful message to all employees that safety is important.
5. Promote Transparency
Transparency is the state in which issues are exposed, and performance statistics are openly shared. This exposure indirectly puts pressure on everyone to perform in a safe manner, reducing the likeliness of incidents happening.
Kinder Morgan is an example of a company that promotes transparency. On its public website, it’s possible to view safety reports including OS recordable injuries and illnesses, avoidable company vehicle accidents, gas pipeline incidents and releases from onshore pipeline rights-of-way, all current and all online.
6. Employee Empowerment
Empowerment is a great way to increase employee buy-in and compliance. t involves providing employees with the authority to make decisions that impact organizational safety. Empowerment sends a clear message that your employees are intelligent, capable people who can make important and sometimes tough decisions when it comes to safety.
“Our control centre operators do not have to get approval to shut down a pipeline if they feel there is an unsafe condition,” says Carter. “This is built into our procedures. It’s part of our training and they will exercise that option when required. This can cost the organization large sums of money for every minute a pipeline is shut down. In a lot of cases, it’s a false alarm, but we ensure there are no repercussions for the employee.”
7. Make It Personal
An important part of creating a strong safety culture is developing personal reasons for employees to work safely. When explaining why safety is important, do it in a way that employees can relate to and ensure that it makes sense for them personally. If you can make that personal connection, it will be more meaningful and can result in a significant change in safety behavior.
Sharon Cole had an especially memorable encounter when she was new in the OHS field. “I had a guy come up to me and say, ‘Safety is no good, and no one can get me to change.’ He was an offshore worker from Newfoundland who traveled back and forth to Alberta—very old school. After listening to him for a bit, I decided on my approach. I said, ‘If you don’t want to look after yourself, at least look after your peers, like your best friend on the rig.’ Their families were close, their kids played together. That got his attention.
I continued, ‘Imagine this: You and your friend are working, and you see him doing something unsafe. You could have reminded him of a safer way, but you didn’t. Later, there’s a knock on your door—you’re told your friend had an incident and didn’t make it. How would you feel, knowing you could’ve made a difference? How will you face his family?’
There was complete silence. Finally, he said, ‘I never thought about safety that way.’ From that day on, he became one of my most safety-conscious workers on the rig.”
8. Communicate Frequently
Frequent and regular communication is critical for successful development of a safety culture. To be motivated to become safer, it is important for everyone to know where the company began in terms of safety, where it is at any point in time, and how far it has come. Adam Czarnecki, Human Resource Manager for Great West Kenworth, suggests sending out monthly statistics on injuries. This information can be provided during tailgate meetings, toolbox meetings, through bulletin boards, newsletters, emails, texts, or a variety of other mediums. Keep in mind that communication needs to be two-way, not just top-down. Ask questions and seek ideas, suggestions, and opinions.
9. Use Appropriate Rewards and Recognitions
To help support the development of a strong safety culture ensure that safe behaviors and attitudes are rewarded and recognized, not by contests or in ways that might cause incidents to go unreported, but in long-term meaningful ways. Examples include consideration for internal promotions, raises, and bonuses.
“When we have safety positions that are available, we always hire from within,” says Chipman. “We have programs that are structured. Folks take safety courses and programs on their days off – on their own time – and they become safety stewards. They receive a little incentive, maybe a dollar per hour and when we need to hire three more safety guys for new projects, we go to our books and say, ‘Whose taken courses?’”
10. Start With Yourself
When it comes to building a safety culture, the most important thing to remember is that it needs to start with you. Too often, the focus is on what others need to do–top management, coworkers, employees, supervisors, and foremen–but no matter what your position is, you need to start with you. If everyone waits for someone else to improve safety within the organization, it is unlikely that change will ever happen.
THE REAL BOTTOM LINE
When it comes to building a safety culture, the most important thing to remember is that it needs to start with you.
When you see what people go through when someone dear to them is seriously injured or killed, you quickly realize that they would give almost anything to undo what happened. If a safety culture can prevent even one life from being lost or destroyed, it is worth the investment of time, money and effort. We shouldn’t wait for a divesting accident or the loss of lives to change our ways and we shouldn’t wait for other people to change first. We need to start with ourselves. With passion, time and consistency of purpose, you can positively impact the culture within your organization; it only requires the decision to make a difference.
Related Articles
- All Posts
- #EmergencyPreparedness
- 2025 safety trends
- 360 Immersive
- 360immersive
- 6S Safety
- accident prevention
- accidental careers
- adjustable workstations
- adult education
- AI automation
- AI implementation
- AI in business
- AI in operations
- AI in Safety
- AI podcast
- AI strategy
- AI transformation
- Alberta safety courses
- Allan James Moore
- artificial intelligence
- asking for help
- audit findings
- audit readiness
- automation in safety
- automation strategy
- avoidable injuries
- awareness
- Aztec Safety
- back strain
- BambooHR integration
- behavior-based safety
- Behavioral Safety
- biometric sensors
- BIS Podcast
- BIS Safety Podcasts
- BIS Safety Software
- BIS Safety Spotlight
- black holes
- Blame Culture
- BP Texas City Explosion
- Brave Leadership
- Brett Burkard
- burnout
- business automation
- Canadian OHS
- Canadian safety
- Canadian safety history
- Canadian safety standards
- carbon monoxide
- Carolynne Heron
- CCOHS
- chemical
- chemical vapors
- chronic injuries
- chronic pain
- cloud-based safety tools
- Coming Soon
- community safety programs
- Competency in Safety
- complacency in safety
- Compliance
- compliance courses
- Compliance In Canada
- compliance issues
- Compliance Reporting
- compliance tools
- compliance training
- compliance vs protection
- Construction advocacy
- Construction education
- Construction industry
- construction safety
- construction safety training
- continuous improvement
- continuous safety improvement
- corporate culture
- corporate training
- corrective actions
- crane
- CSA standards
- Customer Spotlight
- Customer Spotlight Kevin Swinden Global Hazmat Safety Culture Hazmat Management Dangerous Goods Competency in Safety Workplace Risk Mitigation BIS Training Clients Canadian EHS
- customized training
- daily trip inspection
- Damage Prevention
- Dangerous Goods
- dangerous goods classification
- Danny Sellers
- data-driven safety
- Decision Analysis
- defect management
- defect tracking
- defensive driving
- digital compliance
- digital forms
- digital safety
- digital safety tools
- digital safety transformation
- digital transformation
- DMS features
- document control
- document management system
- Dr. Joanna Pagonis
- Dr. Tom Krause
- driver file management
- driver training
- driving instructor program
- DTRMS
- e-learning
- e-learning tools
- early intervention
- education technology
- EHS
- EHS digital solutions
- EHS tools
- Einstein
- electrical safety
- Emergency Action Plan
- emergency preparedness
- emergency response
- emergency supplies
- emotional training
- employee behavior
- employee engagement
- employee health
- Employee Readiness
- employee safety
- employee training
- Energy Isolation
- ergonomic consulting
- ergonomic design
- ergonomic risks
- ergonomics
- Evacuation Procedures
- evidence collection
- EWI Works
- exoskeleton
- exoskeletons
- failure analysis
- fall protection
- field experience
- field safety
- field safety services
- Fire Drills
- fire prevention
- Fire Safety Training
- first aid kit
- first week on the job
- first workplace injury
- fleet management
- fleet safety
- FMEA
- freight
- frontline safety
- future of work
- Global Hazmat
- gravitational waves
- hand injuries
- handling hazardous materials
- hands-on training
- hazard analysis
- Hazard Awareness
- hazard communication
- hazard prevention
- hazard recognition
- Hazardous Energy Control
- Hazmat Management
- Health & Safety Podcast
- health and safety
- hearing loss prevention
- hearing protection
- heavy equipment safety
- hidden workplace hazards
- high voltage systems
- HR automation
- HR software
- human factors
- human in the loop
- Human Performance
- human vs machine
- human-centered design
- human-centered safety
- humor in safety
- ICBC certification
- immersive learning
- Imposter Syndrome
- incident data
- incident investigation
- incident prevention
- incident reporting
- industrial AI
- Industrial Hygiene
- industrial safety
- Infrastructure Risk
- injury consequences
- injury prevention
- injury prevention tips
- injury recovery
- injury reporting
- injury response
- injury response plan
- instructor development
- internal audits
- invisible dangers
- ISO standards
- Jeff Mulligan
- Jennifer Lastra
- job site accountability
- job site hazards
- job site risks
- job site safety
- Jody Young
- KBR Safety Training
- Kevin Swinden
- labor movement
- ladder safety
- Leadership
- leadership accountability
- leadership and empathy
- Leadership in Safety
- Leadership Management
- Lean Manufacturing
- Lean Workplace
- learning from incidents
- learning management
- lifting techniques
- LIGO
- Linda Miller
- LMS
- LMS features
- Lock Out Tag Out
- lockout tagout
- lone workers
- LOTO
- machine learning
- Machine Safety
- Maintenance Safety
- mental health at work
- MI Safety
- Mike Schwartz
- minor injuries
- movement in workplace
- MyZone AI
- Near Miss Reporting
- new workers
- no-blame investigations
- noise exposure
- nonconformance
- Northern BC
- NRCA
- NSC Standard 13
- occupational fatigue
- occupational hazards
- occupational health
- occupational safety
- occupational therapy
- OH&S
- OHS
- OHSA
- oil and gas safety
- omni-training
- onboarding safety
- online learning
- Online safety training
- operational efficiency
- Operational Excellence
- organizational culture
- organizational safety
- OSHA compliance
- OSHA standards
- outdated practices
- overconfidence
- overhead crane courses
- pain awareness
- personal protective equipment
- Pharmaceutical Safety
- physics careers
- pipeline safety
- podcast
- post-accident review
- post-incident protocol
- PPE
- PPE enforcement
- PPE improvement
- pre-trip inspection
- predictive analytics
- pretrip inspection
- preventive action
- proactive safety
- proactive safety measures.
- process improvement
- Professional development
- protective clothing
- psychological hazards
- psychological safety
- quality control
- quality management
- quality standard
- Real Safety Leadership
- real-time safety
- recordkeeping
- regulatory updates
- repetition in safety
- repetitive motion injuries
- respirator safety
- respirators
- risk assessment
- risk management
- risk mitigation
- risk prevention
- risk reduction
- road safety
- Robin Postnikoff
- ROI with AI
- root cause analysis
- root cause correction
- routine task risks
- safe habits
- safe work habits
- safety
- safety accountability
- safety advice
- safety article
- safety automation
- safety awareness
- safety best practices
- safety communication
- safety compliance
- Safety Conversations
- safety culture
- safety data
- safety data sheets
- safety documentation
- safety engagement
- safety follow-up
- safety gear
- safety gloves
- safety goggles
- safety habits
- safety incentives
- safety innovation
- safety insights
- safety inspection
- Safety Leaders
- safety leadership
- Safety Leadership Podcast
- safety legislation
- safety lessons
- safety management
- safety management system
- safety management systems
- safety metrics
- safety mindset
- safety motivation.
- safety myths
- safety planning
- safety podcast
- safety procedure updates
- Safety Procedures
- safety professionals
- safety reporting
- safety review process
- safety shortcuts
- safety software
- Safety Spotlight
- safety systems
- safety technology
- safety theater
- safety tips
- safety training
- safety transformation
- safety transparency
- Sarah Anderson
- Scott Lyall
- shipping documentation
- silent dangers
- silica dust
- Sinogap Solutions
- slow-building hazards
- smart helmets
- smart PPE
- smart safety systems
- smart safety tools
- space science
- Spencer McDonald
- Standardized Work
- storytelling and safety
- storytelling in safety
- supervisor training
- system safety
- TDG
- team communication
- teamwork
- tech and ergonomics
- tech in safety
- tech-enabled learning
- Thinking Driver
- Titan Environmental
- Total Recordable Injury Formula
- tough guy mentality
- toxic air
- training
- training courses
- training management
- training matrix
- training record management
- training records
- training software
- transportation
- transportation of dangerous goods
- Trust and Accountability
- unseen workplace threats
- user experience
- Utility Safety Partners
- vehicle safety
- version control
- veteran advice
- Virtual Reality
- VR safety training
- VR Technology
- wearable technology
- WHMIS
- witness statements
- women in leadership
- work-alone training
- work-related injuries
- worker accountability
- worker advocacy
- worker fatigue
- worker protection
- worker safety
- worker safety habits
- worker safety tips
- worker trust
- worker wellbeing
- workers' rights
- workforce compliance
- workforce management
- workforce training
- workplace accidents
- workplace air quality
- workplace best practices
- workplace certification
- workplace compliance
- Workplace Culture
- workplace hazards
- workplace health
- workplace incident response
- workplace injuries
- workplace injury prevention
- workplace mindset
- Workplace Organization
- workplace risk factors
- workplace risk management
- Workplace Risk Mitigation
- Workplace safety
- workplace safety culture
- Workplace Safety Leadership
- workplace safety rules
- workplace safety tips
- workplace safety training
- workplace stress
- workplace tiredness
- workplace wellness
- WSPS
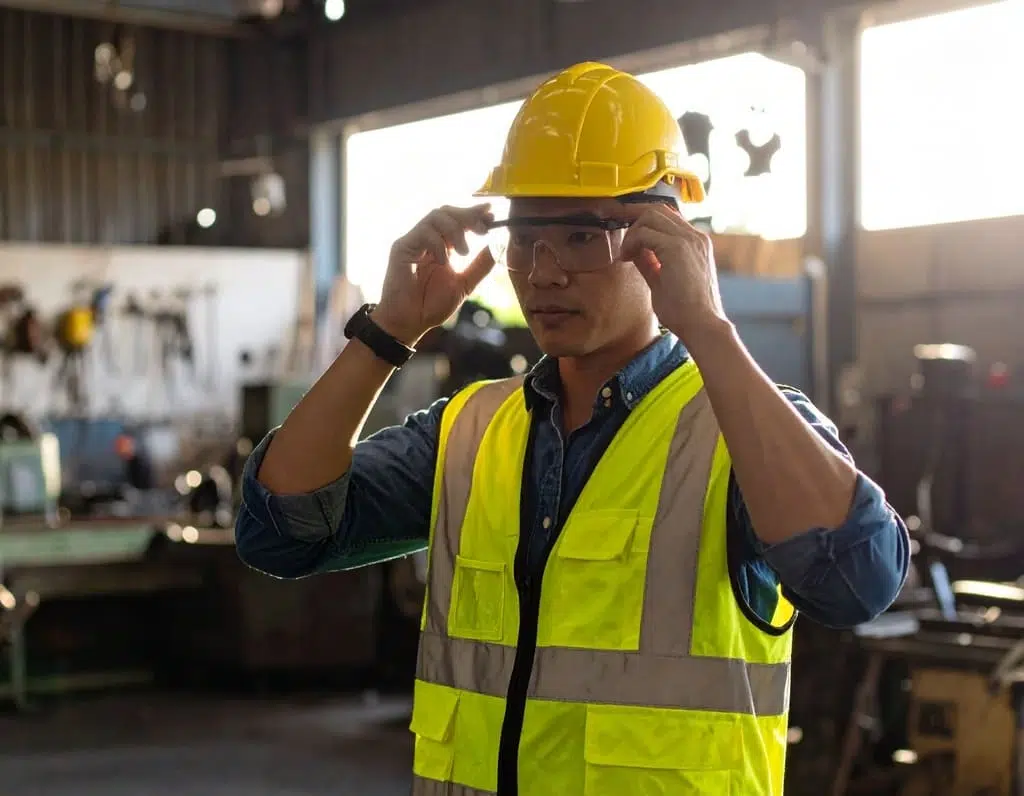
PPE is the last line of defense against workplace hazards—from hard hats to respirators. To be effective, it must be...
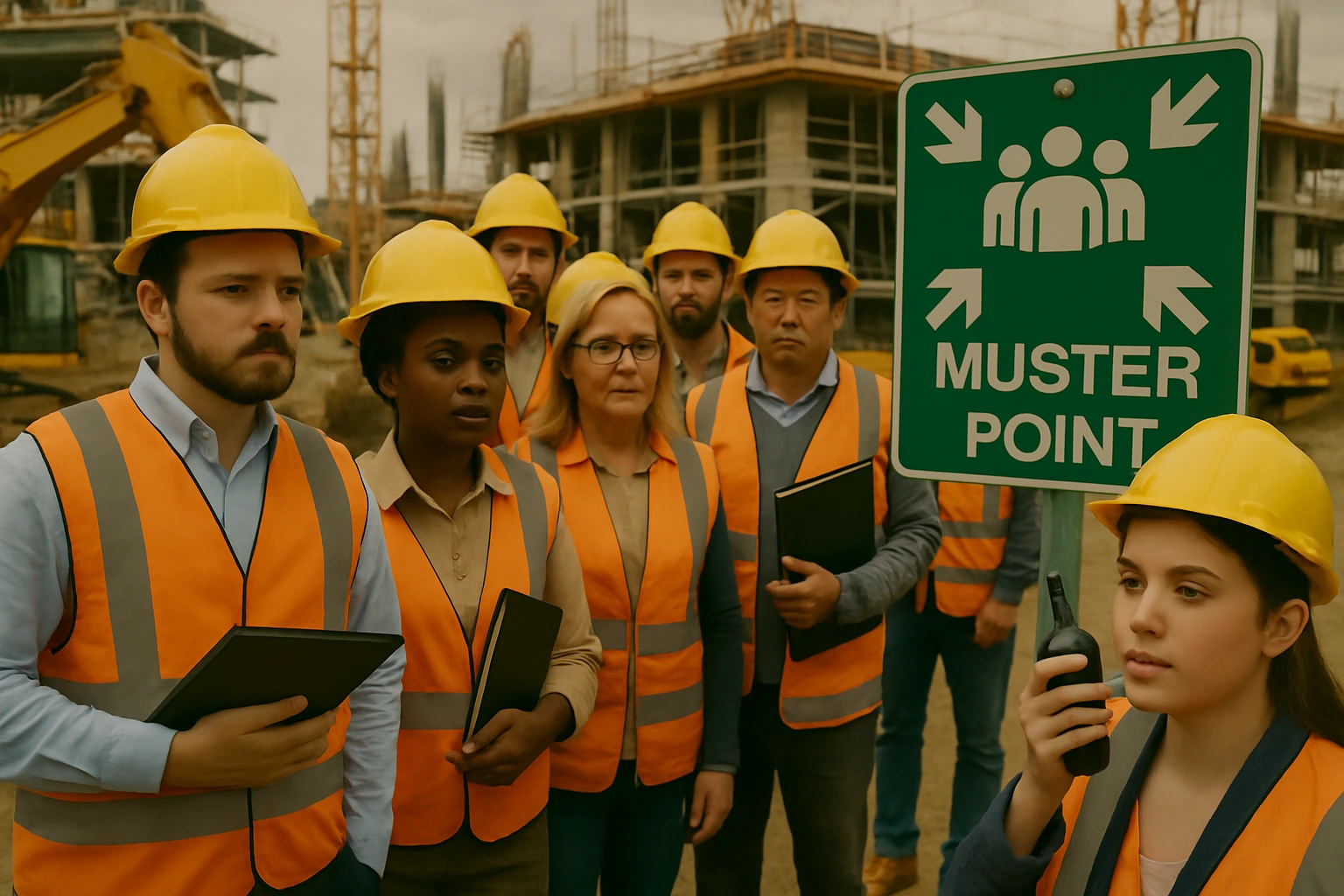
Conducting regular fire drills is more than a formality—it’s essential for building confidence, reinforcing roles, and ensuring workplace teams respond...
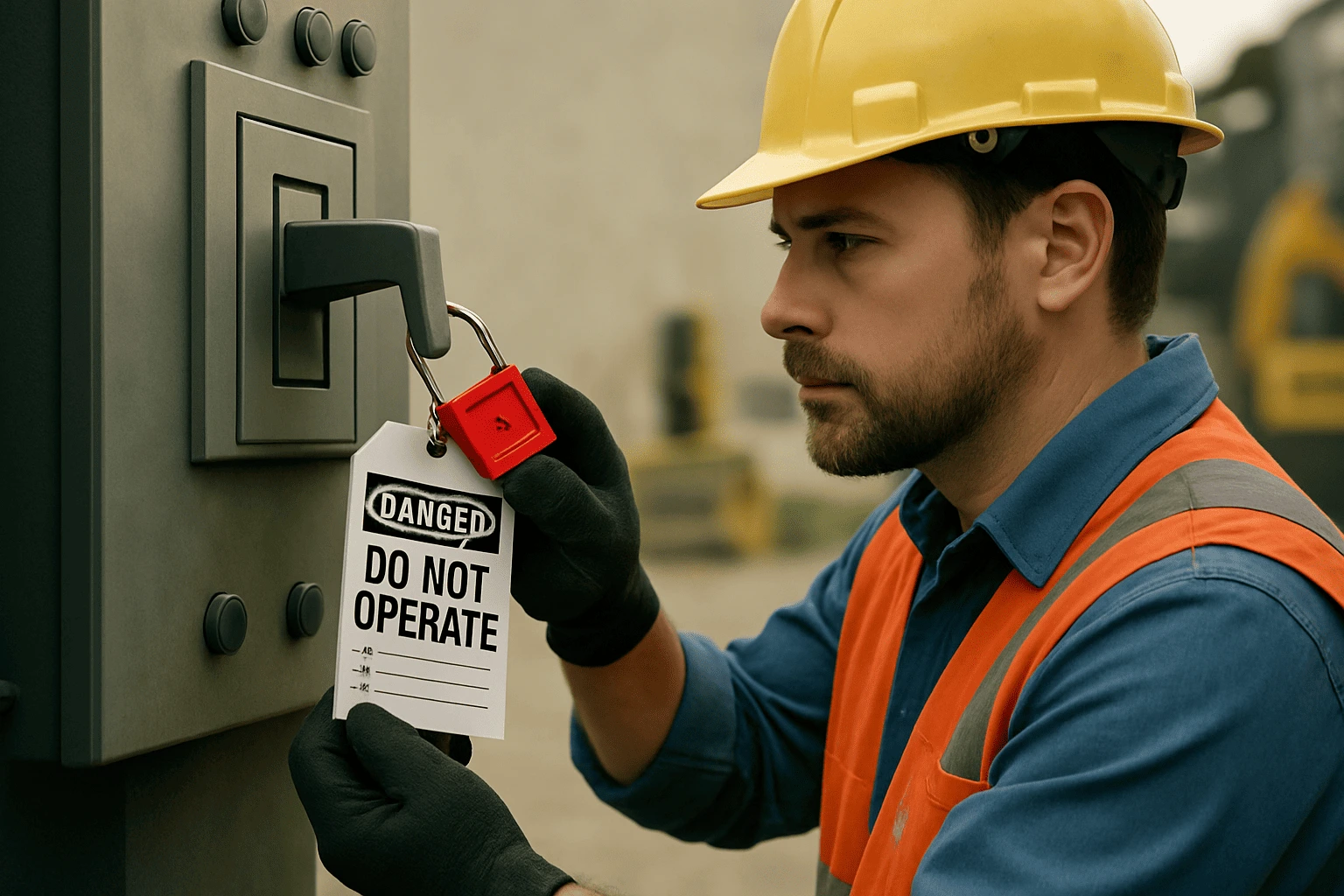
LOTO compliance protects workers in Canadian industries by requiring equipment to be locked and tagged during repair or inspection activities.