Every company says it. It’s on posters, hard hats, and PowerPoint slides. “Safety first.”
But here’s the truth: you don’t prove that with a motto, and you know that. You prove it in moments of pressure, when timelines tighten, budgets shrink, and someone spots a hazard no one wants to deal with.
The companies who truly put safety first? They show it. Every day. And they’re the ones workers trust! The ones that thrive in their industries.
What “Safety First” Actually Looks Like
▸Deadlines don’t come first, people do.
“When you’re outside at -50°, trying to get something done, safety needs to be part of how you think,” said Jeremy Desilets, founder of Clearline Safety. “That only happens when leadership walks the walk.”
▸ Training is built to stick.
Robin Postnikoff of MI Safety built his entire business on that idea. “You can explain to someone how to turn a wheel,” he said. “But until they drive the car, on ice, in traffic, they don’t get it. That’s how it works with safety. Until you do it, it’s not real.”
▸ Leaders lead with safety.
If the crew sees managers skipping PPE or brushing off hazards, they take that as permission. But when leaders show up prepared, stay curious, and prioritize safety over shortcuts? That’s when culture shifts.
▸ Safety lives in trust, and action.
Here’s how Allan Moore described it:
“When I worked on the rigs, everything was manual. No automation, no iron roughnecks. Just heavy tools, fast rhythms, and a thick injury report filled with things you never want to read about. I was new. Nobody knew me. And still, these guys had my back.
They’d say, ‘Don’t stand there. My buddy did and now he’s missing fingers.’ Or, ‘Come with me, I’ll show you the right way to do this.’ They didn’t lecture me. They protected me. That’s safety.
If they hadn’t stepped in, I might not be here today. That experience taught me what a real safety culture feels like. It’s about watching out for each other. Every day. Without being asked.”
Five Ways to Put Safety First
1. Pause the job.
If something feels off, stop. Fix it first. Your team needs to know that safety pauses are not only allowed, they’re expected.
2. Train hands-on.
Don’t rely on lectures. Get people doing, practicing, problem-solving. The goal isn’t memorization, it’s confidence.
3. Track what prevents problems.
Measure what matters: near-miss reports, hazard fixes, team engagement. That’s where real safety lives.
4. Empower every voice.
If workers hesitate to speak up, your system needs attention, and fast. Build trust by showing that concerns lead to action.
5. Lead visibly.
When execs model the same safety standards as frontline crews, the message is clear: this isn’t optional, it’s who we are.
Safety Culture Is a System, Not a Slogan
Companies that prioritize safety do what they say, and say what they’ll do. They build systems that reinforce safety, daily, visibly, consistently. They don’t wait for a serious incident to take safety seriously. They learn from close calls. They improve from feedback. And they make safety part of how the whole team thinks. Does your company prove “safety first” with action?
Because the difference isn’t just about productivity. It could be the reason your people go home safe. Be proud of when and how you prioritize safety – for yourself and others,
Related Articles
- All Posts
- #EmergencyPreparedness
- 2025 safety trends
- 360 Immersive
- 360immersive
- 6S Safety
- accident prevention
- accidental careers
- adjustable workstations
- adult education
- AI automation
- AI implementation
- AI in business
- AI in operations
- AI in Safety
- AI podcast
- AI strategy
- AI transformation
- Alberta safety courses
- Allan James Moore
- artificial intelligence
- asking for help
- audit findings
- audit readiness
- Audit Reporting
- automation in safety
- automation strategy
- avoidable injuries
- awareness
- Aztec Safety
- back strain
- BambooHR integration
- behavior-based safety
- Behavioral Safety
- behavioural safety
- biometric sensors
- BIS Podcast
- BIS Safety Podcasts
- BIS Safety Software
- BIS Safety Spotlight
- black holes
- Blame Culture
- BP Texas City Explosion
- Brave Leadership
- Brett Burkard
- burnout
- business automation
- Canadian OHS
- Canadian safety
- Canadian safety history
- Canadian safety standards
- carbon monoxide
- Carolynne Heron
- CCOHS
- chemical
- chemical vapors
- chronic injuries
- chronic pain
- cloud-based safety tools
- Coming Soon
- community safety programs
- Competency in Safety
- complacency in safety
- Compliance
- compliance courses
- Compliance In Canada
- compliance issues
- Compliance management
- Compliance Reporting
- compliance software
- compliance tools
- compliance tracking
- compliance training
- compliance vs protection
- Construction advocacy
- Construction education
- Construction industry
- construction safety
- construction safety training
- continuous improvement
- continuous safety improvement
- corporate culture
- corporate training
- corrective actions
- crane
- CSA standards
- Customer Spotlight
- Customer Spotlight Kevin Swinden Global Hazmat Safety Culture Hazmat Management Dangerous Goods Competency in Safety Workplace Risk Mitigation BIS Training Clients Canadian EHS
- customized training
- daily trip inspection
- Damage Prevention
- Dangerous Goods
- dangerous goods classification
- Danny Sellers
- data-driven safety
- Decision Analysis
- defect management
- defect tracking
- defensive driving
- DEI in onboarding
- digital compliance
- digital forms
- Digital Hazard Reporting
- Digital Onboarding
- digital safety
- Digital Safety Audits
- Digital safety systems
- digital safety tools
- digital safety transformation
- Digital Training Tools
- digital transformation
- DMS features
- document control
- document management system
- Dr. Joanna Pagonis
- Dr. Tom Krause
- driver file management
- driver training
- driving instructor program
- DTRMS
- e-learning
- e-learning tools
- eadership in safety
- early intervention
- education technology
- EHS
- EHS Adoption
- EHS Compliance
- EHS digital solutions
- EHS Inspections
- EHS Onboarding
- EHS software
- EHS systems
- EHS tools
- Einstein
- electrical safety
- Emergency Action Plan
- emergency preparedness
- emergency procedures
- emergency response
- emergency supplies
- emotional training
- employee behavior
- employee engagement
- employee health
- Employee onboarding
- Employee Readiness
- employee safety
- employee training
- Energy Isolation
- ergonomic consulting
- ergonomic design
- ergonomic risks
- ergonomics
- Evacuation Procedures
- evidence collection
- EWI Works
- exoskeleton
- exoskeletons
- failure analysis
- fall protection
- fast onboarding
- field experience
- field level hazard assessments
- field operations
- field safety
- field safety assessments
- field safety leadership
- field safety services
- Field Safety Technology
- Field-Friendly Software
- Fire Drills
- fire prevention
- Fire Safety Training
- first aid kit
- first week on the job
- first workplace injury
- fleet management
- fleet safety
- FLHA engagement
- FLHA Integration
- FLHA software
- FMEA
- freight
- Frontline Engagement
- frontline safety
- fuel handling
- future of work
- Global Hazmat
- global onboarding
- gravitational waves
- gut feeling in safety
- hand injuries
- handling hazardous materials
- hands-on training
- hazard analysis
- hazard assessment compliance
- Hazard Awareness
- hazard communication
- Hazard Identification
- hazard prevention
- hazard recognition
- Hazardous Energy Control
- Hazmat Management
- Health & Safety Podcast
- health and safety
- hearing loss prevention
- hearing protection
- heavy equipment safety
- hidden workplace hazards
- high voltage systems
- HR automation
- HR software
- human factors
- human factors in safety
- human in the loop
- Human Performance
- human vs machine
- human-centered design
- human-centered safety
- humor in safety
- ICBC certification
- identification
- immersive learning
- Imposter Syndrome
- incident data
- incident investigation
- incident prevention
- incident reporting
- industrial AI
- Industrial Hygiene
- industrial safety
- influence vs control
- Infrastructure Risk
- injury consequences
- injury prevention
- injury prevention tips
- injury recovery
- injury reporting
- injury response
- injury response plan
- instructor development
- internal audits
- international workforce
- interpreting safety data
- invisible dangers
- ISO standards
- Jeff Mulligan
- Jennifer Lastra
- job site accountability
- job site hazards
- job site risks
- job site safety
- jobsite readiness
- Jody Young
- KBR Safety Training
- Kevin Swinden
- labor movement
- ladder safety
- Leadership
- leadership accountability
- leadership and empathy
- Leadership in Safety
- Leadership Management
- leadership messaging
- Lean Manufacturing
- Lean Workplace
- learning from incidents
- learning management
- lifting techniques
- LIGO
- Linda Miller
- LMS
- LMS features
- LMS software
- Lock Out Tag Out
- lockout tagout
- lone workers
- LOTO
- machine learning
- Machine Safety
- Maintenance Safety
- mental health at work
- MI Safety
- microlearning
- Mike Schwartz
- minor injuries
- mobile onboarding
- Mobile Safety Apps
- Mobile Safety Platforms
- Mobile Safety Tools
- movement in workplace
- multilingual training
- MyZone AI
- Near Miss Reporting
- new hire experience
- New Hire Safety
- New Worker Training
- new workers
- no-blame investigations
- noise exposure
- nonconformance
- Northern BC
- NRCA
- NSC Standard 13
- occupational fatigue
- occupational hazards
- occupational health
- occupational safety
- occupational therapy
- OH&S
- OHS
- OHSA
- oil and gas safety
- omni-training
- onboarding safety
- Onboarding Software
- online learning
- Online safety training
- operational efficiency
- Operational Excellence
- organizational culture
- organizational safety
- OSHA compliance
- OSHA standards
- outdated practices
- overconfidence
- overhead crane courses
- pain awareness
- personal protective equipment
- Pharmaceutical Safety
- physics careers
- pipeline safety
- playbook software
- podcast
- post-accident review
- post-incident protocol
- PPE
- PPE enforcement
- PPE improvement
- pre-trip inspection
- predictive analytics
- pretrip inspection
- preventive action
- proactive safety
- proactive safety measures.
- Proactive Safety Systems
- process improvement
- Professional development
- propane safety
- propane storage
- protective clothing
- psychological hazards
- psychological safety
- quality control
- quality management
- quality standard
- Real Safety Leadership
- Real-Time Reporting
- real-time safety
- recordkeeping
- regulatory updates
- repetition in safety
- repetitive motion injuries
- respirator safety
- respirators
- risk assessment
- risk management
- risk mitigation
- risk prevention
- Risk Prevention Tools
- risk reduction
- road safety
- Robin Postnikoff
- ROI with AI
- root cause analysis
- root cause correction
- routine task risks
- safe habits
- safe transport
- safe work habits
- safety
- safety accountability
- safety advice
- safety article
- Safety Audit Software
- safety automation
- safety awareness
- safety best practices
- safety communication
- safety compliance
- Safety Conversations
- safety culture
- safety data
- safety data sheets
- safety documentation
- safety engagement
- safety follow-up
- safety gear
- safety gloves
- safety goggles
- safety habits
- safety incentives
- safety innovation
- safety insights
- safety inspection
- safety instinct
- Safety Leaders
- safety leadership
- Safety Leadership Podcast
- safety legislation
- safety lessons
- safety management
- safety management system
- safety management systems
- safety metrics
- safety mindset
- safety motivation.
- safety myths
- safety onboarding
- safety planning
- safety podcast
- safety procedure updates
- Safety Procedures
- safety professionals
- safety reporting
- safety review process
- safety shortcuts
- safety software
- Safety Spotlight
- safety systems
- safety technology
- safety theater
- safety tips
- safety training
- safety transformation
- safety transparency
- Sarah Anderson
- scalable training solutions
- Scott Lyall
- shipping documentation
- silent dangers
- silica dust
- Sinogap Solutions
- slow-building hazards
- smart helmets
- smart PPE
- smart safety systems
- smart safety tools
- SOPs
- space science
- Spencer McDonald
- Standardized Work
- storytelling and safety
- storytelling in safety
- supervisor training
- system safety
- TDG
- team communication
- teamwork
- tech and ergonomics
- tech in safety
- tech-enabled learning
- Thinking Driver
- Titan Environmental
- Total Recordable Injury Formula
- tough guy mentality
- toxic air
- training
- training courses
- Training integration
- training management
- training matrix
- training record management
- training records
- training software
- transportation
- transportation of dangerous goods
- Trust and Accountability
- unseen workplace threats
- user experience
- Utility Safety Partners
- values-based onboarding
- vehicle safety
- version control
- veteran advice
- Virtual Reality
- VR safety training
- VR Technology
- wearable technology
- WHMIS
- witness statements
- women in leadership
- work-alone training
- work-related injuries
- worker accountability
- worker advocacy
- worker fatigue
- worker protection
- worker safety
- worker safety habits
- worker safety tips
- worker trust
- worker wellbeing
- workers' rights
- Workforce Automation
- workforce compliance
- Workforce development
- workforce engagement
- workforce management
- Workforce Readiness
- workforce training
- workplace accidents
- workplace air quality
- workplace best practices
- workplace certification
- workplace compliance
- Workplace Culture
- Workplace Hazard Tracking
- workplace hazards
- workplace health
- workplace incident response
- workplace injuries
- workplace injury prevention
- workplace mindset
- Workplace Organization
- workplace risk factors
- workplace risk management
- Workplace Risk Mitigation
- Workplace safety
- workplace safety culture
- Workplace Safety Leadership
- workplace safety rules
- workplace safety tech
- workplace safety tips
- Workplace Safety Tools
- workplace safety training
- workplace stress
- workplace tiredness
- workplace wellness
- WSPS
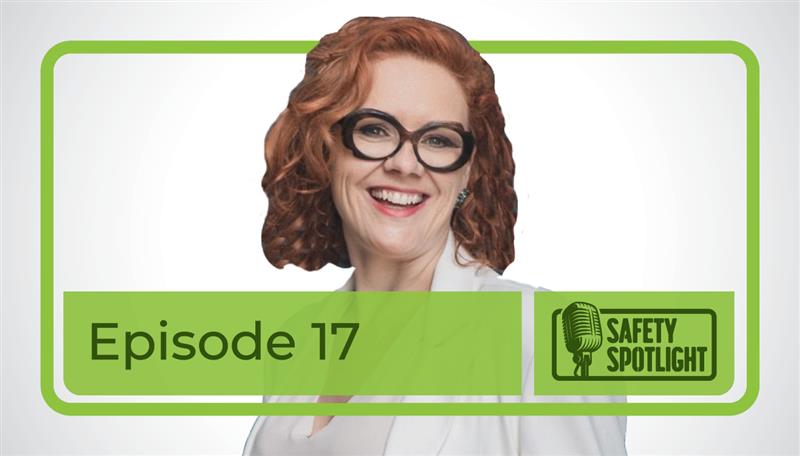
What happens when we stop treating safety as just rules and checklists, and start focusing on people, connection, and how...
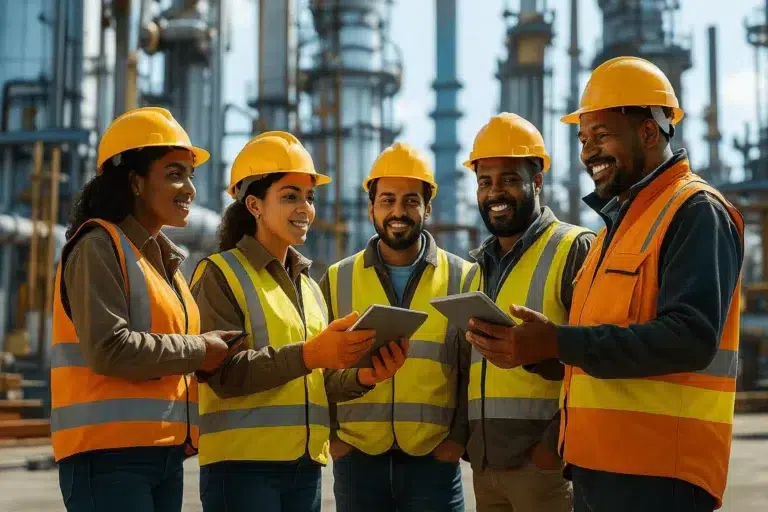
Playbook Software centralizes and standardizes safety procedures, policies, and response plans. Give your team instant access to the latest, most...
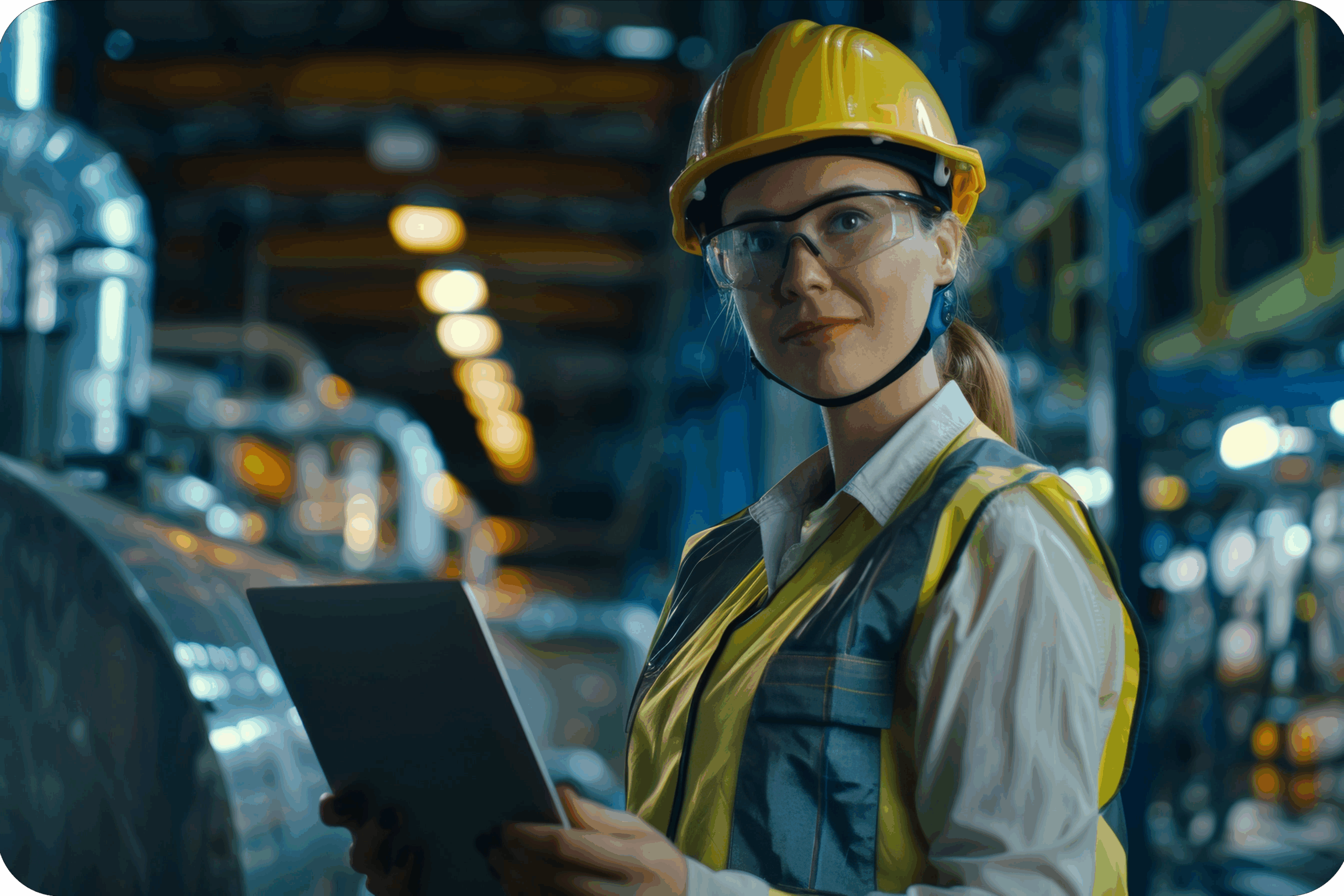
Strong, accessible documentation is key to safer, more efficient worksites. Learn why it matters, where it fails, and how to...