How Kevin Swinden built Global Hazmat by prioritizing competency, culture, and real-world preparedness
Why Competency Matters More Than Certification
The interesting thing about Kevin Swinden is that he “doesn’t do” titles. He feels they’re impractical and too high-minded. There’s no need, in his mind, to create an imbalance in the workplace. He is the founder and president of Global Hazmat, but more than that, he is, in his simple words, “the owner.”
His experience and knowledge includes three decades of navigating hazardous materials. He’s reshaping how organizations approach their safety culture. Kevin’s seen too many close calls and knows the cost of complacency. “Safety and hazmat are often very separate, but they shouldn’t be,” he says.
For Swinden, this divide is a critical flaw he’s spent 30 years working to correct. He’s blunt about the consequences. This disconnect is especially stark in Canada. Here, EHS managers juggle many roles. Their United States counterparts enjoy “more specialized” siloed positions.
“It’s a structural gap that leaves people vulnerable,” says Swinden. His passion for bridging this divide is evident in every aspect of his work.
“Hazmat is frequently sidelined and shuffled away. Most of the time, safety personnel have absolutely zero understanding of hazardous materials. Zero experience with dangerous goods or waste management.“
Kevin Swinden – President
Founding a Legacy
Swinden’s path to founding Global Hazmat wasn’t linear. He was “disillusioned” and frustrated by a lack of integrity in his previous roles. Clear objectives in the industry were few and far between, so he struck out on his own.
“I realized I couldn’t work for people who didn’t have a clear purpose, I felt like I was spinning my wheels” he says. “So, I decided to do it myself. I said… I’m going to go off and become your competitor.” Starting as a one-man operation, he built Global Hazmat brick by brick. Fueled by a relentless commitment to precision and education, he found his north star: “Doing things the right way.”
Over the years, Swinden’s vision has transformed Global Hazmat into a leader in the industry. The company’s name change 18 years ago The company’s name-change 18 years ago was a signal of its evolution – a shift towards something bigger. “You have to adapt constantly,” Swinden reflects. “Regulations change, industries shift, and things keep evolving. Staying stagnant really isn’t an option, it just isn’t.”
Lessons From the Field
Swinden’s career is full of moments that would rattle most people. He recounts a chlorine gas incident, the result of improperly packed/stored chemical waste. The reaction required evacuating over 100 homes and countless businesses. “One 45-gallon drum has a bad reaction and suddenly we’re evacuating a Canadian Tire, a Scotiabank, a Costco, a gym. Anything the wind could touch with this chlorine gas. It’s a perfect example of why competency matters more than a certification,” he says. “A certificate won’t save you in front of a judge, much less a gas leak. A certificate doesn’t mean a hill of beans if you aren’t competent. Show me you can do this.”
There’s not much of a margin for error in his industry, but there’s nuance. Training employees to understand chemical waste takes an eye for detail.
“A lot of people don’t realize that chemical-as-product and chemical-as-waste have identical properties and hazards,” he explains. “I’ve seen drums packed with incompatible chemicals create dangerous reactions.” His work, like any good safety initiative, focuses on potential consequences. The smallest misstep in understanding could mean big problems later.
Safety is a concrete reality, not a hypothetical concept. Practical knowledge will always beat rote learning. “You learn from error, but you have to make the choice to learn from the error.” Uncover the gap and fix it.
Bridging Gaps and Changing Minds
Swinden is candid about the challenges in the industry. His main frustration is with the industry’s reactive culture. “Employers often mandate training for their employees but don’t train themselves,” he explains. Safety changes often create a bottleneck when they need to be implemented. Moreover, many companies only focus on safety after accidents.
“The biggest problem is trying to change the organization’s culture. They need to shift to a proactive point of view. It takes time,” he acknowledges. “But it’s essential.”
One persistent issue is the handling of paperwork. Swinden recounts an audit where 83% of shipping documents were incorrect. It was a simple oversight that could lead to disaster.
“It’s ‘not that important’, until you get caught. Picture this,” he says. “You’re a responder showing up to an accident and the intel you have does not match what’s going on. What’s your priority then? You are responsible for the costs of a document’s flaws. And it could be millions Those flaws get pushed onto first responders during an accident.” Incorrect documentation is more than an admin mistake. It’s a critical failure. It can disrupt emergency response efforts and endanger everyone involved.”
“We’ve had to call in the bomb squad a couple of times in the past. Three years ago, I got called to a mobile trailer. They had stockpiled chemicals for 15 years and then skipped town.
We had to clean this trailer full of chemicals and hazardous items. Situations like that are nerve-wracking because there is no documentation. There is no compliance whatsoever, and so there’s no sense of safety.“
Kevin Swinden – President
A Philosophy of Preparedness
For Swinden, preparedness is personal, and a survival skill at that.
He recalls a near miss during an emergency response training session. “It’s not enough to assess [the spill]; you need to assess your entire area. We had a case where an employee was panicking. Part of their task was to go get the spill supplies. They were almost impaled by a forklift. The operator came around the corner with the forks up. The employee had to jump off to the side to avoid being struck. That hazard had nothing to do with the spill, but it still presented a danger in the workplace.”
Swinden’s emphasis on preparedness extends beyond immediate hazards. He understands safety culture’s broader implications. He urges organizations to adopt proactive measures, not just reactive fixes or band-aids. “It’s not only about preventing accidents, but fostering a mindset,” he explains. “It has to be cultural.”
Looking to the Future
As technology reshapes industries, Swinden remains optimistic. “I’m old school, as you’ve figured out. I’m always going to be a very, very strong believer in competency as the key. I’m 100% for any tech that makes things better, so long as it doesn’t hurt competency,” he says. “[This industry] is looking at different avenues, methods that are not as archaic as the old ways. But the core understanding must remain. It has to match workers’ skills and compliance. If it speeds things up and cuts corners, it’s useless. Jeopardizing competency is not an advantage; the biggest issue we see is confusion between being certified and being competent.”
Swinden also sees opportunities in digitizing processes like documentation. “Canada’s moving toward electronic paperwork, which is a step in the right direction,” he notes. “Switching over is going to be a long process, but it’s going to reduce errors. It will save you from trying to read pages that are soaking wet.”
Advice for Newcomers
For those new to the safety world, Swinden’s guidance is clear: find a mentor, network, and never stop learning. “You can’t learn everything in school,” he says. “Having the education is great, but most of what I’ve learned was either by making a mistake or talking to someone. [Mentors] will explain things to you, and you’ll go ‘oh, I’ve never thought about that.’ Experience and the willingness to listen are invaluable. You have to be willing to be a part of the safety industry as a whole; you can’t pretend you know everything.” He urges young pros to find seasoned experts, attend trade shows, and immerse themselves.
Swinden also stresses the importance of humility. “Having a master’s degree doesn’t make you a good safety professional. What matters is your experience, your network, your ability to listen and learn,” he asserts. “I see this often. A safety person markets themselves as a guru with 20 years of experience at 17 companies. I would never hire them in my life because they can’t invest in a safety culture for longer than a year.” His advice resonates in an industry where experience trumps degrees.
A Quiet Revolution
Kevin Swinden’s work with Global Hazmat shows the power of persistence and precision. He has built more than a company. He has fostered a culture of competence and care in a neglected corner of the safety world.
Swinden’s journey underscores the importance of bridging gaps between safety and hazmat. In a world where small mistakes can have grave results, Swinden’s mission reminds us of the impact one person can have on safety culture.
Work smart. Stay strong. Speak up.
Related Articles
- All Posts
- #EmergencyPreparedness
- 2025 safety trends
- 360 Immersive
- 360immersive
- 6S Safety
- accident prevention
- accidental careers
- adjustable workstations
- adult education
- AI automation
- AI implementation
- AI in business
- AI in operations
- AI in Safety
- AI podcast
- AI strategy
- AI transformation
- Alberta safety courses
- Allan James Moore
- artificial intelligence
- asking for help
- audit findings
- audit readiness
- Audit Reporting
- automation in safety
- automation strategy
- avoidable injuries
- awareness
- Aztec Safety
- back strain
- BambooHR integration
- behavior-based safety
- Behavioral Safety
- behavioural safety
- biometric sensors
- BIS Podcast
- BIS Safety Podcasts
- BIS Safety Software
- BIS Safety Spotlight
- black holes
- Blame Culture
- BP Texas City Explosion
- Brave Leadership
- Brett Burkard
- burnout
- business automation
- Canadian OHS
- Canadian safety
- Canadian safety history
- Canadian safety standards
- carbon monoxide
- Carolynne Heron
- CCOHS
- chemical
- chemical vapors
- chronic injuries
- chronic pain
- cloud-based safety tools
- Coming Soon
- community safety programs
- Competency in Safety
- complacency in safety
- Compliance
- compliance courses
- Compliance In Canada
- compliance issues
- Compliance management
- Compliance Reporting
- compliance software
- compliance tools
- compliance tracking
- compliance training
- compliance vs protection
- Construction advocacy
- Construction education
- Construction industry
- construction safety
- construction safety training
- continuous improvement
- continuous safety improvement
- corporate culture
- corporate training
- corrective actions
- crane
- CSA standards
- Customer Spotlight
- Customer Spotlight Kevin Swinden Global Hazmat Safety Culture Hazmat Management Dangerous Goods Competency in Safety Workplace Risk Mitigation BIS Training Clients Canadian EHS
- customized training
- daily trip inspection
- Damage Prevention
- Dangerous Goods
- dangerous goods classification
- Danny Sellers
- data-driven safety
- Decision Analysis
- defect management
- defect tracking
- defensive driving
- DEI in onboarding
- digital compliance
- digital forms
- Digital Hazard Reporting
- Digital Onboarding
- digital safety
- Digital Safety Audits
- Digital safety systems
- digital safety tools
- digital safety transformation
- Digital Training Tools
- digital transformation
- DMS features
- document control
- document management system
- Dr. Joanna Pagonis
- Dr. Tom Krause
- driver file management
- driver training
- driving instructor program
- DTRMS
- e-learning
- e-learning tools
- eadership in safety
- early intervention
- education technology
- EHS
- EHS Adoption
- EHS Compliance
- EHS digital solutions
- EHS Inspections
- EHS Onboarding
- EHS software
- EHS systems
- EHS tools
- Einstein
- electrical safety
- Emergency Action Plan
- emergency preparedness
- emergency procedures
- emergency response
- emergency supplies
- emotional training
- employee behavior
- employee engagement
- employee health
- Employee onboarding
- Employee Readiness
- employee safety
- employee training
- Energy Isolation
- ergonomic consulting
- ergonomic design
- ergonomic risks
- ergonomics
- Evacuation Procedures
- evidence collection
- EWI Works
- exoskeleton
- exoskeletons
- failure analysis
- fall protection
- fast onboarding
- field experience
- field level hazard assessments
- field operations
- field safety
- field safety assessments
- field safety leadership
- field safety services
- Field Safety Technology
- Field-Friendly Software
- Fire Drills
- fire prevention
- Fire Safety Training
- first aid kit
- first week on the job
- first workplace injury
- fleet management
- fleet safety
- FLHA engagement
- FLHA Integration
- FLHA software
- FMEA
- freight
- Frontline Engagement
- frontline safety
- fuel handling
- future of work
- Global Hazmat
- global onboarding
- gravitational waves
- gut feeling in safety
- hand injuries
- handling hazardous materials
- hands-on training
- hazard analysis
- hazard assessment compliance
- Hazard Awareness
- hazard communication
- Hazard Identification
- hazard prevention
- hazard recognition
- Hazardous Energy Control
- Hazmat Management
- Health & Safety Podcast
- health and safety
- hearing loss prevention
- hearing protection
- heavy equipment safety
- hidden workplace hazards
- high voltage systems
- HR automation
- HR software
- human factors
- human factors in safety
- human in the loop
- Human Performance
- human vs machine
- human-centered design
- human-centered safety
- humor in safety
- ICBC certification
- identification
- immersive learning
- Imposter Syndrome
- incident data
- incident investigation
- incident prevention
- incident reporting
- industrial AI
- Industrial Hygiene
- industrial safety
- influence vs control
- Infrastructure Risk
- injury consequences
- injury prevention
- injury prevention tips
- injury recovery
- injury reporting
- injury response
- injury response plan
- instructor development
- internal audits
- international workforce
- interpreting safety data
- invisible dangers
- ISO standards
- Jeff Mulligan
- Jennifer Lastra
- job site accountability
- job site hazards
- job site risks
- job site safety
- jobsite readiness
- Jody Young
- KBR Safety Training
- Kevin Swinden
- labor movement
- ladder safety
- Leadership
- leadership accountability
- leadership and empathy
- Leadership in Safety
- Leadership Management
- leadership messaging
- Lean Manufacturing
- Lean Workplace
- learning from incidents
- learning management
- lifting techniques
- LIGO
- Linda Miller
- LMS
- LMS features
- LMS software
- Lock Out Tag Out
- lockout tagout
- lone workers
- LOTO
- machine learning
- Machine Safety
- Maintenance Safety
- mental health at work
- MI Safety
- microlearning
- Mike Schwartz
- minor injuries
- mobile onboarding
- Mobile Safety Apps
- Mobile Safety Platforms
- Mobile Safety Tools
- movement in workplace
- multilingual training
- MyZone AI
- Near Miss Reporting
- new hire experience
- New Hire Safety
- New Worker Training
- new workers
- no-blame investigations
- noise exposure
- nonconformance
- Northern BC
- NRCA
- NSC Standard 13
- occupational fatigue
- occupational hazards
- occupational health
- occupational safety
- occupational therapy
- OH&S
- OHS
- OHSA
- oil and gas safety
- omni-training
- onboarding safety
- Onboarding Software
- online learning
- Online safety training
- operational efficiency
- Operational Excellence
- organizational culture
- organizational safety
- OSHA compliance
- OSHA standards
- outdated practices
- overconfidence
- overhead crane courses
- pain awareness
- personal protective equipment
- Pharmaceutical Safety
- physics careers
- pipeline safety
- playbook software
- podcast
- post-accident review
- post-incident protocol
- PPE
- PPE enforcement
- PPE improvement
- pre-trip inspection
- predictive analytics
- pretrip inspection
- preventive action
- proactive safety
- proactive safety measures.
- Proactive Safety Systems
- process improvement
- Professional development
- propane safety
- propane storage
- protective clothing
- psychological hazards
- psychological safety
- quality control
- quality management
- quality standard
- Real Safety Leadership
- Real-Time Reporting
- real-time safety
- recordkeeping
- regulatory updates
- repetition in safety
- repetitive motion injuries
- respirator safety
- respirators
- risk assessment
- risk management
- risk mitigation
- risk prevention
- Risk Prevention Tools
- risk reduction
- road safety
- Robin Postnikoff
- ROI with AI
- root cause analysis
- root cause correction
- routine task risks
- safe habits
- safe transport
- safe work habits
- safety
- safety accountability
- safety advice
- safety article
- Safety Audit Software
- safety automation
- safety awareness
- safety best practices
- safety communication
- safety compliance
- Safety Conversations
- safety culture
- safety data
- safety data sheets
- safety documentation
- safety engagement
- safety follow-up
- safety gear
- safety gloves
- safety goggles
- safety habits
- safety incentives
- safety innovation
- safety insights
- safety inspection
- safety instinct
- Safety Leaders
- safety leadership
- Safety Leadership Podcast
- safety legislation
- safety lessons
- safety management
- safety management system
- safety management systems
- safety metrics
- safety mindset
- safety motivation.
- safety myths
- safety onboarding
- safety planning
- safety podcast
- safety procedure updates
- Safety Procedures
- safety professionals
- safety reporting
- safety review process
- safety shortcuts
- safety software
- Safety Spotlight
- safety systems
- safety technology
- safety theater
- safety tips
- safety training
- safety transformation
- safety transparency
- Sarah Anderson
- scalable training solutions
- Scott Lyall
- shipping documentation
- silent dangers
- silica dust
- Sinogap Solutions
- slow-building hazards
- smart helmets
- smart PPE
- smart safety systems
- smart safety tools
- SOPs
- space science
- Spencer McDonald
- Standardized Work
- storytelling and safety
- storytelling in safety
- supervisor training
- system safety
- TDG
- team communication
- teamwork
- tech and ergonomics
- tech in safety
- tech-enabled learning
- Thinking Driver
- Titan Environmental
- Total Recordable Injury Formula
- tough guy mentality
- toxic air
- training
- training courses
- Training integration
- training management
- training matrix
- training record management
- training records
- training software
- transportation
- transportation of dangerous goods
- Trust and Accountability
- unseen workplace threats
- user experience
- Utility Safety Partners
- values-based onboarding
- vehicle safety
- version control
- veteran advice
- Virtual Reality
- VR safety training
- VR Technology
- wearable technology
- WHMIS
- witness statements
- women in leadership
- work-alone training
- work-related injuries
- worker accountability
- worker advocacy
- worker fatigue
- worker protection
- worker safety
- worker safety habits
- worker safety tips
- worker trust
- worker wellbeing
- workers' rights
- Workforce Automation
- workforce compliance
- Workforce development
- workforce engagement
- workforce management
- Workforce Readiness
- workforce training
- workplace accidents
- workplace air quality
- workplace best practices
- workplace certification
- workplace compliance
- Workplace Culture
- Workplace Hazard Tracking
- workplace hazards
- workplace health
- workplace incident response
- workplace injuries
- workplace injury prevention
- workplace mindset
- Workplace Organization
- workplace risk factors
- workplace risk management
- Workplace Risk Mitigation
- Workplace safety
- workplace safety culture
- Workplace Safety Leadership
- workplace safety rules
- workplace safety tech
- workplace safety tips
- Workplace Safety Tools
- workplace safety training
- workplace stress
- workplace tiredness
- workplace wellness
- WSPS
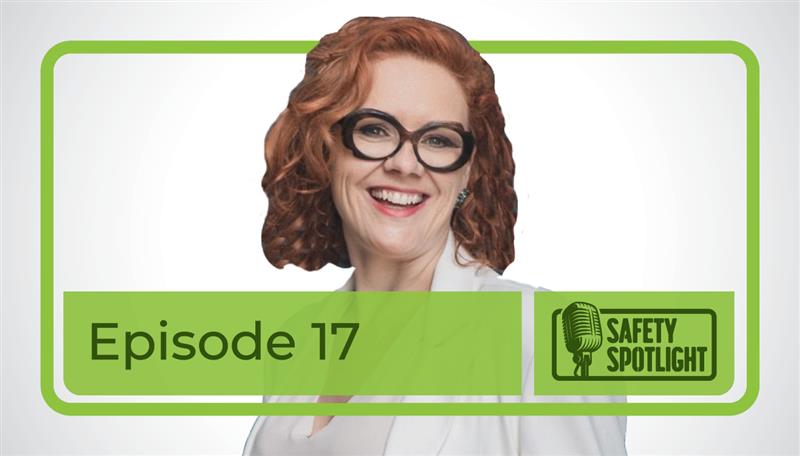
What happens when we stop treating safety as just rules and checklists, and start focusing on people, connection, and how...
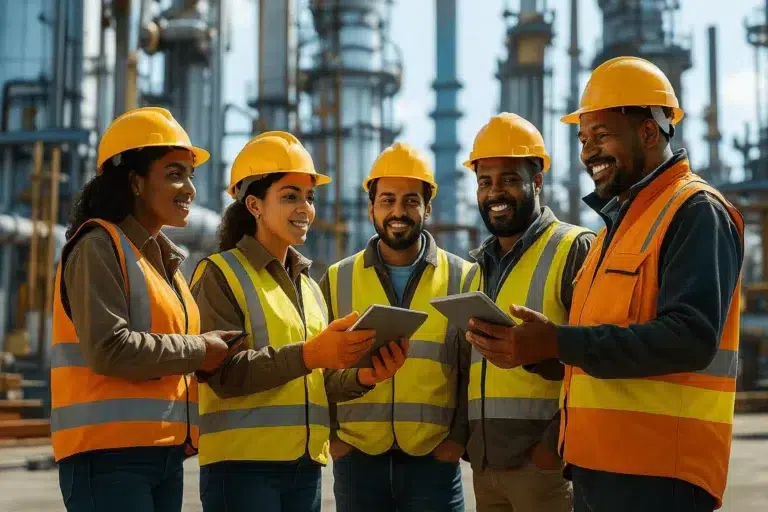
Playbook Software centralizes and standardizes safety procedures, policies, and response plans. Give your team instant access to the latest, most...
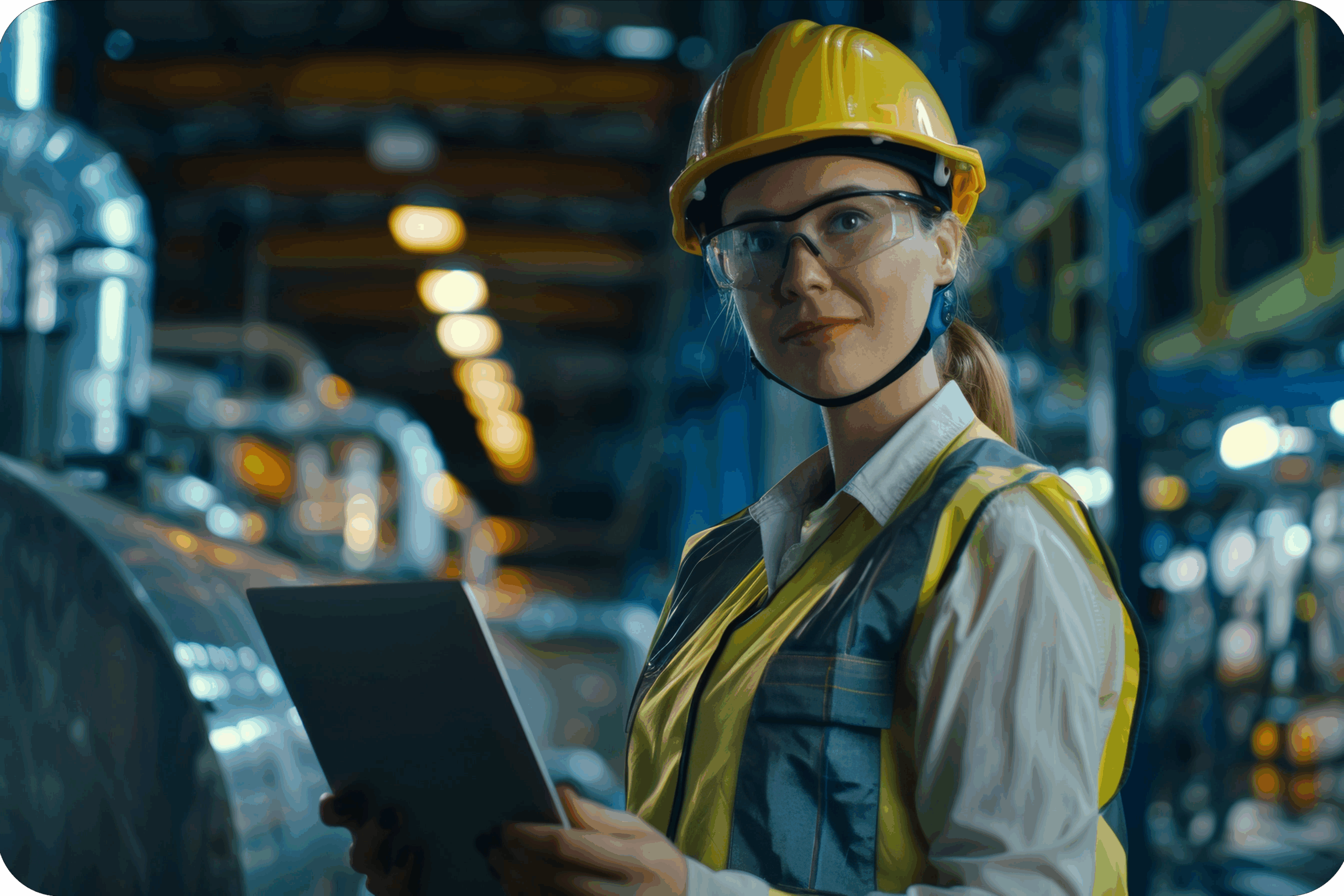
Strong, accessible documentation is key to safer, more efficient worksites. Learn why it matters, where it fails, and how to...