Companies are fitting workers with smart vests that predict heat exhaustion before it happens. AI systems scan job sites, spotting dangers human eyes miss. Entire emergency plans are rehearsed in virtual reality before a shovel ever hits the dirt. From oil rigs to office towers, technology is bulldozing its way into the world of hazard prevention. But here’s the million-dollar question: Is all this tech actually keeping people safer—or is it just a high-priced security blanket?
Wes Rundle, a safety manager with 12 years in the trenches, says the stakes are real: “Technology can give us incredible insight, but if you’re not building trust with your crews first, all the gadgets in the world won’t stop accidents.”
Robin Postnikoff, who’s trained workers for two decades, agrees — but with a warning. “You can explain a concept all day long. But until someone actually does the skill — under real-world pressure — they don’t truly know it. No amount of online theory will change that.”
As companies race to digitize their safety programs, a tough truth is emerging. Smart tech can assist. But it can’t replace human instincts, judgment, or responsibility. The future of safety might be wired and AI-enhanced — but it’s still human at the core.
The Rise of AI in Workplace Safety
Predictive Analytics: Seeing Trouble Before It Hits
Imagine foreseeing workplace accidents before they occur. That’s the promise of predictive analytics. By analyzing vast amounts of data—near-misses, weather patterns, equipment failures—companies can identify risks before they escalate.
At Newmont Mining Corp (formerly Goldcorp), implementing predictive safety tools led to a significant reduction in incident rates, providing managers with insights into previously unnoticed dangers. A Deloitte report highlighted that organizations integrating predictive analytics into their Environment, Health & Safety (EHS) programs experienced a 25% reduction in incidents within the first year. Moreover, in the oil refining sector, the adoption of AI-driven monitoring systems resulted – broadly — in a 50% decrease in safety incidents, underscoring the tangible benefits of predictive analytics in high-risk industries.
As Brett Burkard, a veteran of high-risk construction projects, aptly puts it: “Repetition builds awareness. Technology just gives us another set of eyes to catch what humans miss when we get complacent.”
By leveraging predictive analytics, companies not only enhance safety but also foster a proactive culture that prioritizes prevention over reaction.
Computer Vision: Watching Workers in Real Time
Forget random spot-checks. Imagine a job site where AI-powered cameras monitor compliance with personal protective equipment (PPE) in real-time. A study published in Sustainability developed a deep learning system achieving 97.5% accuracy in detecting PPE compliance, including hard hats, safety vests, and glasses.
These systems are being deployed across various industries, automatically flagging missing safety gear and ensuring that workers adhere to safety protocols without the need for constant human supervision. In the construction sector, AI-driven PPE compliance monitoring has reduced incident rates by ensuring workers consistently adhere to PPE requirements on-site. VCA Technology
Smart Sensors: Listening to the Body and the Air
Wearable sensors are revolutionizing workplace safety by monitoring vital signs and environmental conditions in real-time. A study published in PNAS Nexus explored using multimodal wearable sensors combined with machine learning to measure real-time fatigue among manufacturing workers. The research demonstrated that wearable technology and cutting-edge AI methods could accurately identify fatigue through multi-modal data analysis.
For instance, smart helmets equipped with sensors can detect signs of fatigue or overheating, prompting workers to take necessary breaks and reducing the risk of accidents. In construction, fatigue-related incidents account for approximately 20% of injuries, underscoring the importance of such technology.
Case Study: Amazon’s AI Safety Push — A Cautionary Tale
During the COVID-19 pandemic, Amazon introduced “Proxemics,” an AI tool designed to enforce social distancing by analyzing footage from security cameras and alerting managers to potential violations.
While the technology aimed to enhance safety, it sparked concerns among employees about constant surveillance and privacy. Some workers reported increased stress and anxiety, feeling that the monitoring was more about productivity than safety.
This case underscores the importance of balancing technological advancements with respect for employee privacy and well-being.
Automation: Taking Humans Out of Harm’s Way
When the Danger’s Too High, Send a Robot
In the past, when a bridge needed inspecting or a chemical drum needed moving, it was a human that stepped into the fire. Now, it’s a drone or a robotic arm.
Across industries, machines are slipping into the most dangerous jobs — and not a moment too soon. Drones fly into unstable tunnels, scanning for cracks without risking a single life. Robotic arms, built for precision and resilience, handle toxic chemicals that could leave a worker hospitalized.
Brett Burkard, who once oversaw teams installing water tanks in war zones, knows firsthand the cost of human exposure. “You can plan for safety all you want,” says Burkard, “but some environments are just unpredictable. Drones don’t get tired, they don’t panic. They don’t bleed.”
At BASF, a global chemical giant, robotic systems now handle hazardous material packaging, slashing worker exposure and trimming accident rates.
Self-Monitoring Equipment: Machines That Know When They’re Failing
Before, you’d wait for a machine to break, then scramble. Now machines tattle on themselves.
Today’s heavy equipment — from cranes to compressors — is embedded with AI-powered sensors that monitor wear, detect overheating, and predict failures before they happen. It’s like having a mechanic living inside the engine, whispering warnings before disaster strikes. In a world where a snapped cable or a seized bearing can turn fatal, this kind of early warning isn’t just smart. It’s survival.
Automation and the End of “Fatigue Mistakes”
No matter how good a worker is, fatigue is the silent killer. Miss a bolt. Skip a checklist. One small error, one big tragedy. That’s why companies are automating more repetitive tasks — welding, labeling, sorting — stripping out the risk of human exhaustion.
As Allan Moore, a safety expert who’s walked oilfields from Canada to Taiwan, put it: “We all want to get home at the end of the day with ten fingers and ten toes. Taking the grunt work off people’s shoulders makes that a hell of a lot more likely.”
Case Study: Robots Reducing Risk, One Task at a Time
A sweeping report from the European Agency for Safety and Health at Work found that companies introducing robotics into high-risk tasks — like mining, shipping, and manufacturing — saw not just fewer injuries, but fewer severe injuries.
Automating the most dangerous jobs didn’t just help workers. It helped the companies’ bottom lines too, cutting downtime and slashing insurance costs. In the battle between flesh-and-blood workers and brutal environments, automation is proving to be the best ally they’ve ever had.
Emerging Technology: The New Guard (and Faces) of Safety Tools
From AI-powered cameras to wearables that scream when your posture slips, safety tech has officially gone next-gen. Here are the tools — and the people — rewriting the rules.
Platforms That Predict Before It Happens
A wave of new software is giving safety teams what they’ve always needed: foresight.
- Avetta One flags at-risk contractors before they step on site.
- SparkCognition EHS Insights predicts hazards using historical data and machine learning.
- Soter Analytics and Kinetic Reflex use wearables to catch dangerous body mechanics in real time, preventing the strains and tears that don’t always make headlines — but still ruin lives.
- Intenseye watches entire facilities through existing CCTV systems, using computer vision to spot hazards and noncompliance as they happen — and sometimes before.
Even giants like IBM and Honeywell are deep in the game. With platforms like Watson IoT for Worker Safety and Safety Watch, they’re mixing data from environmental sensors, wearables, and equipment into one powerful prediction engine.
As fatigue, exposure, and overexertion remain among the top causes of workplace incidents, tools like Fatigue Science’s ReadiWatch are becoming must-haves in heavy industry. Their AI can flag when a worker is likely to crash — not after lunch, but 18 hours before it happens.
The Canadians Leading the Charge
This isn’t just global innovation — it’s happening right here at home. Canada has quietly become a hub for safety tech, led by visionaries building tools to stop accidents before they start.
Jason Lee (SmartCone Technologies, Ottawa)
Invented an AI-equipped “smart cone” that sets digital boundaries on worksites. These cones create “no-go zones” and talk to nearby wearables, warning workers when they’re in danger — or about to be.
Noel Simpson (EHS Analytics, Calgary)
Helps high-risk industries build massive safety data warehouses. His team’s AI models can sift through thousands of incident reports and extract trends — predicting injury patterns and flagging hot spots before they hit the stats board.
Cody Slater (Blackline Safety, Calgary)
Drives global deployment of cloud-connected wearables that detect gas leaks, falls, or no-motion events in real time. His tools don’t just alert teams — they log data, analyze trends, and create feedback loops that change behavior.
Andrew Morden (Fatigue Science, Vancouver)
Put predictive fatigue on the map. His platform calculates sleep debt and stress levels, then turns them into a fatigue score that helps companies rework shifts, reassign jobs, or pull people before burnout leads to injury.
Neil Cawse (Geotab, Oakville)
Brought AI-powered driving behavior analytics to trucking and logistics. His platform watches for harsh braking, speeding, and signs of drowsiness, giving dispatchers a chance to intervene before collisions happen.
Christian Browne (Humo, Saskatchewan)
Grew frustrated with “post-mortem” safety. So he built Humo — wearable sensors that buzz workers when their posture or movement becomes dangerous, acting like a personal safety coach in real time.
Greg Brouwer (Teck Resources, Vancouver)
Runs the digital innovation team at one of Canada’s largest mining companies. He’s layering AI over everything from vehicle collision avoidance to predictive maintenance, helping prevent the kind of equipment failures that turn deadly underground.
These aren’t just tech products. They’re force multipliers — systems designed to work with the people on the ground, not over them. Their message is clear:
Don’t wait for the accident report. Predict it. Prevent it.
Wearable Tech: Turning Workers Into Walking Safety Monitors
The Hard Hat Just Got a Brain
Once, a hard hat was just a chunk of plastic between you and a cracked skull. Now it’s a command center. Smart helmets and augmented-reality glasses are hitting job sites across North America, giving workers real-time hazard alerts, step-by-step repair instructions, and even navigation help through mazes of scaffolding and machinery. At Shell, field technicians are already using AR helmets that display schematics while they work — meaning fewer mistakes, faster jobs, and a lot less risk.
As Kevin Swinden, founder of Global Hazmat, put it:
“You can hand someone a manual. You can give them a checklist. But real safety happens in the moment. That’s where tech needs to meet them — right in the field, right when it matters.“
Exoskeletons: Turning Humans into Heavy-Lifting Machines
It’s not science fiction anymore. Across warehouses and construction sites, exoskeletons — wearable mechanical suits — are being strapped onto workers to reduce back strain, shoulder injuries, and repetitive motion damage. Companies like Ford and Toyota have been testing exosuits for years, helping workers lift heavy parts or maintain awkward positions without wrecking their bodies.
And the early results? Fewer injuries. Fewer sick days. Fewer workers walking into retirement broken and bent.
Fatigue and Biometric Monitoring: Listening to the Body Before It Breaks
If exhaustion had a warning light, most accidents could be avoided. Now, it does.
Smartwatches, biometric vests, and even “smart” shirts are tracking worker heart rates, breathing, hydration levels, and sleep patterns. When a worker’s body starts sending distress signals — dehydration, heatstroke risk, microsleeps — supervisors get instant alerts.
Dr. Johanna Pagonis, an expert in psychological safety, says tech like this is only as good as the trust behind it. “You can have all the monitors you want,” says Dr. Pagonis “but if workers don’t feel safe speaking up when they’re burning out, you’ll still miss the warning signs.”
Some companies are already tying biometric data into their safety protocols — adjusting shift schedules, cooling down hot zones, and getting exhausted workers off the floor before it’s too late.
The Challenges of Safety Tech
The machines are getting smarter. But that doesn’t mean the problems are going away.
Privacy vs. Protection: Where’s the Line?
Your vest is tracking your vitals. Your smartwatch knows when you’re tired. Your helmet has a camera. Feels a bit like Big Brother in a hard hat. Smart tech promises protection, but it’s also raising eyebrows — and blood pressure. Workers are starting to ask: Are we being kept safe, or being watched?
Jennifer Lastra, a veteran of both the military and manufacturing worlds, doesn’t sugarcoat it: “You can’t build trust if people feel like they’re being policed. Safety tools have to serve the worker — not the other way around.”
The backlash isn’t theoretical. Amazon faced intense criticism when it rolled out AI-powered systems that tracked workers’ movements, flagged bathroom breaks, and even monitored internal communications to suppress union efforts. The company called it efficiency. Workers called it surveillance.
When Tech Makes Us Too Comfortable
There’s a hidden danger in automation: it can lull people into complacency.
“You hand someone a tool that promises to catch everything,” says Wes Rundle, “and pretty soon they stop looking for themselves. That’s when bad things happen.”
In one documented case on a construction site, a crew ignored a faulty piece of scaffolding because the system hadn’t flagged it yet. The only thing that saved them? A worker who still bothered to do a manual walkaround. Sometimes, old-school beats high-tech.
The Price of Safety — and Who Gets Left Behind
Safety technology doesn’t come cheap. For enterprise giants, it’s a rounding error. But for mom-and-pop contractors? Or nonprofits? It’s often out of reach. Smaller firms face a cruel irony: they’re more likely to need help managing safety, but less likely to afford the tools.
Guy Martin, who rebuilt an entire municipal safety system from scratch, knows the pain well: “You can’t just throw money at safety and expect it to stick. But the right tech — the stuff that actually helps — most small shops can’t even look at the price tag.”
The risk? A digital divide where only large companies get the benefit of next-gen safety, while smaller ones are left behind — stuck with paper logs and wishful thinking.
Just because it beeps doesn’t mean it’s got your back.
The Future: Where Do We Go From Here?
Tech can’t save us. But it can help us save ourselves.
No machine — no matter how smart — replaces gut instinct. The future of safety isn’t about trading hard hats for headsets. It’s about blending the two — AI that flags a risk, and a human who knows whether it’s real or just noise.
John Holmes, a president who came up through the trades, puts it bluntly: “AI’s great, but it doesn’t know what a gut check feels like. A system can warn you. Only you can stop the job.”
Let the tech watch your back. But don’t turn your back to the job.
Evolving Safety Standards: Catching Up to the Code
Regulators aren’t blind to the tech wave — they’re trying to ride it too. In Canada, agencies like CSA Group and WorkSafeBC are drafting new frameworks for AI and sensor-integrated PPE. In the U.S., OSHA has begun exploring how predictive analytics could play a role in inspections. But here’s the catch: technology moves fast. Government moves like molasses uphill in January.
That leaves a gap — a gray area where companies are using bleeding-edge tools under outdated rulebooks. The fix? Forward-thinking safety leaders are working with regulators to test and trial new tools before writing them into law.
“It’s coming,” says Rundle, “but it’ll be messy. We’re building the plane while we fly it.”
What’s Coming in the Next Decade?
Smart PPE will become the norm. Helmets that detect brain trauma. Vests that call for help before a worker passes out. Gloves that sense chemical exposure and alert you before you feel it. AI-driven enforcement is just getting started. Think systems that not only flag risk but issue corrective action plans automatically. No clipboard. No excuses. Behavioral safety tools will get sharper. The tech won’t just watch hazards — it’ll watch how we behave around them. Subtle signs of fatigue, distraction, or stress could become as measurable as a fall hazard.
But here’s the big truth:
No matter how smart the system, it’s still people who make the call.
And that might be the best safeguard of all. The future of safety isn’t human or machine. It’s both — shoulder to shoulder.
Conclusion: Tech Can’t Replace a Strong Safety Culture
Tools don’t make a safe workplace. People do.
You can wire a job site with sensors. Fit workers with smart gear. Feed data into algorithms faster than a safety officer can blink. But none of it matters if the culture’s broken.
“You can explain a concept all day long,” says Robin Postnikoff. “But until someone actually does the skill — under real-world pressure — they don’t truly know it.”
Tech helps. But it doesn’t lead. That job still falls to people who speak up, who shut things down when they feel wrong, who care enough to watch out for each other. AI, automation, and wearables only work when they’re backed by something stronger — training, communication, and accountability. The best workplaces in the next decade won’t just be high-tech. They’ll be high-trust. Because at the end of the day, the smartest system in the world can’t build a culture.
Only people can do that.
No algorithm has ever filled out an incident report. Keep the culture strong — the tech will follow.
Work smart. Stay strong. Speak up.
Related Articles
- All Posts
- 360 Immersive
- 360immersive
- accident prevention
- accidental careers
- adjustable workstations
- adult education
- AI automation
- AI implementation
- AI in business
- AI in operations
- AI in Safety
- AI podcast
- AI strategy
- AI transformation
- Alberta safety courses
- Allan James Moore
- artificial intelligence
- asking for help
- audit readiness
- automation in safety
- automation strategy
- avoidable injuries
- awareness
- Aztec Safety
- back strain
- BambooHR integration
- behavior-based safety
- Behavioral Safety
- biometric sensors
- BIS Podcast
- BIS Safety Podcasts
- BIS Safety Software
- BIS Safety Spotlight
- black holes
- Blame Culture
- BP Texas City Explosion
- Brave Leadership
- Brett Burkard
- burnout
- business automation
- Canadian safety history
- Canadian safety standards
- carbon monoxide
- Carolynne Heron
- CCOHS
- chemical
- chemical vapors
- chronic injuries
- chronic pain
- cloud-based safety tools
- Coming Soon
- community safety programs
- Competency in Safety
- complacency in safety
- Compliance
- compliance courses
- compliance tools
- compliance vs protection
- Construction advocacy
- Construction education
- Construction industry
- construction safety
- construction safety training
- continuous improvement
- continuous safety improvement
- corporate culture
- crane
- Customer Spotlight
- Customer Spotlight Kevin Swinden Global Hazmat Safety Culture Hazmat Management Dangerous Goods Competency in Safety Workplace Risk Mitigation BIS Training Clients Canadian EHS
- customized training
- daily trip inspection
- Damage Prevention
- Dangerous Goods
- dangerous goods classification
- Danny Sellers
- data-driven safety
- Decision Analysis
- defensive driving
- digital compliance
- digital forms
- digital safety tools
- digital safety transformation
- digital transformation
- DMS features
- document control
- document management system
- Dr. Joanna Pagonis
- Dr. Tom Krause
- driver file management
- driver training
- driving instructor program
- DTRMS
- e-learning
- early intervention
- education technology
- EHS
- EHS digital solutions
- Einstein
- electrical safety
- emergency preparedness
- emergency response
- emergency supplies
- emotional training
- employee behavior
- employee engagement
- employee health
- employee safety
- employee training
- ergonomic consulting
- ergonomic design
- ergonomic risks
- ergonomics
- evidence collection
- EWI Works
- exoskeleton
- exoskeletons
- fall protection
- field experience
- field safety
- field safety services
- fire prevention
- first aid kit
- first week on the job
- first workplace injury
- fleet management
- fleet safety
- freight
- frontline safety
- future of work
- Global Hazmat
- gravitational waves
- hand injuries
- handling hazardous materials
- hands-on training
- Hazard Awareness
- hazard communication
- hazard prevention
- hazard recognition
- Hazmat Management
- Health & Safety Podcast
- health and safety
- hearing loss prevention
- hearing protection
- heavy equipment safety
- hidden workplace hazards
- high voltage systems
- HR automation
- HR software
- human factors
- human in the loop
- Human Performance
- human vs machine
- human-centered design
- human-centered safety
- humor in safety
- ICBC certification
- immersive learning
- Imposter Syndrome
- incident data
- incident investigation
- incident prevention
- incident reporting
- industrial AI
- Industrial Hygiene
- industrial safety
- Infrastructure Risk
- injury consequences
- injury prevention
- injury prevention tips
- injury recovery
- injury reporting
- injury response
- injury response plan
- instructor development
- internal audits
- invisible dangers
- Jeff Mulligan
- Jennifer Lastra
- job site accountability
- job site hazards
- job site risks
- job site safety
- Jody Young
- KBR Safety Training
- Kevin Swinden
- labor movement
- ladder safety
- Leadership
- leadership accountability
- leadership and empathy
- Leadership in Safety
- Leadership Management
- learning from incidents
- lifting techniques
- LIGO
- Linda Miller
- LMS
- lockout tagout
- lone workers
- machine learning
- mental health at work
- MI Safety
- Mike Schwartz
- minor injuries
- movement in workplace
- MyZone AI
- new workers
- no-blame investigations
- noise exposure
- Northern BC
- NRCA
- NSC Standard 13
- occupational fatigue
- occupational hazards
- occupational health
- occupational safety
- occupational therapy
- OH&S
- OHS
- OHSA
- oil and gas safety
- omni-training
- onboarding safety
- Online safety training
- operational efficiency
- organizational culture
- organizational safety
- OSHA compliance
- OSHA standards
- outdated practices
- overconfidence
- overhead crane courses
- pain awareness
- personal protective equipment
- Pharmaceutical Safety
- physics careers
- pipeline safety
- podcast
- post-accident review
- post-incident protocol
- PPE
- PPE enforcement
- PPE improvement
- pre-trip inspection
- predictive analytics
- pretrip inspection
- proactive safety
- proactive safety measures.
- Professional development
- protective clothing
- psychological hazards
- psychological safety
- Real Safety Leadership
- real-time safety
- recordkeeping
- regulatory updates
- repetition in safety
- repetitive motion injuries
- respirator safety
- respirators
- risk management
- risk reduction
- road safety
- Robin Postnikoff
- ROI with AI
- root cause analysis
- routine task risks
- safe work habits
- safety
- safety accountability
- safety advice
- safety article
- safety automation
- safety awareness
- safety best practices
- safety communication
- safety compliance
- Safety Conversations
- safety culture
- safety data
- safety data sheets
- safety documentation
- safety engagement
- safety follow-up
- safety gear
- safety gloves
- safety goggles
- safety habits
- safety incentives
- safety innovation
- safety insights
- safety inspection
- Safety Leaders
- safety leadership
- Safety Leadership Podcast
- safety legislation
- safety lessons
- safety management
- safety management system
- safety management systems
- safety metrics
- safety mindset
- safety motivation.
- safety myths
- safety podcast
- safety procedure updates
- safety professionals
- safety reporting
- safety review process
- safety shortcuts
- safety software
- Safety Spotlight
- safety systems
- safety technology
- safety theater
- safety tips
- safety training
- safety transformation
- safety transparency
- Sarah Anderson
- Scott Lyall
- shipping documentation
- silent dangers
- silica dust
- Sinogap Solutions
- slow-building hazards
- smart helmets
- smart PPE
- smart safety systems
- space science
- Spencer McDonald
- storytelling and safety
- storytelling in safety
- supervisor training
- TDG
- team communication
- teamwork
- tech and ergonomics
- tech in safety
- tech-enabled learning
- Thinking Driver
- Titan Environmental
- Total Recordable Injury Formula
- tough guy mentality
- toxic air
- training
- training courses
- training matrix
- training record management
- training records
- transportation
- transportation of dangerous goods
- Trust and Accountability
- unseen workplace threats
- Utility Safety Partners
- vehicle safety
- version control
- veteran advice
- Virtual Reality
- VR safety training
- VR Technology
- wearable technology
- WHMIS
- witness statements
- women in leadership
- work-alone training
- work-related injuries
- worker accountability
- worker advocacy
- worker fatigue
- worker protection
- worker safety
- worker safety habits
- worker safety tips
- worker trust
- worker wellbeing
- workers' rights
- workforce compliance
- workforce management
- workforce training
- workplace accidents
- workplace air quality
- workplace best practices
- workplace certification
- Workplace Culture
- workplace hazards
- workplace health
- workplace incident response
- workplace injuries
- workplace injury prevention
- workplace mindset
- workplace risk factors
- workplace risk management
- Workplace Risk Mitigation
- Workplace safety
- workplace safety culture
- Workplace Safety Leadership
- workplace safety rules
- workplace safety tips
- workplace safety training
- workplace stress
- workplace tiredness
- workplace wellness
- WSPS
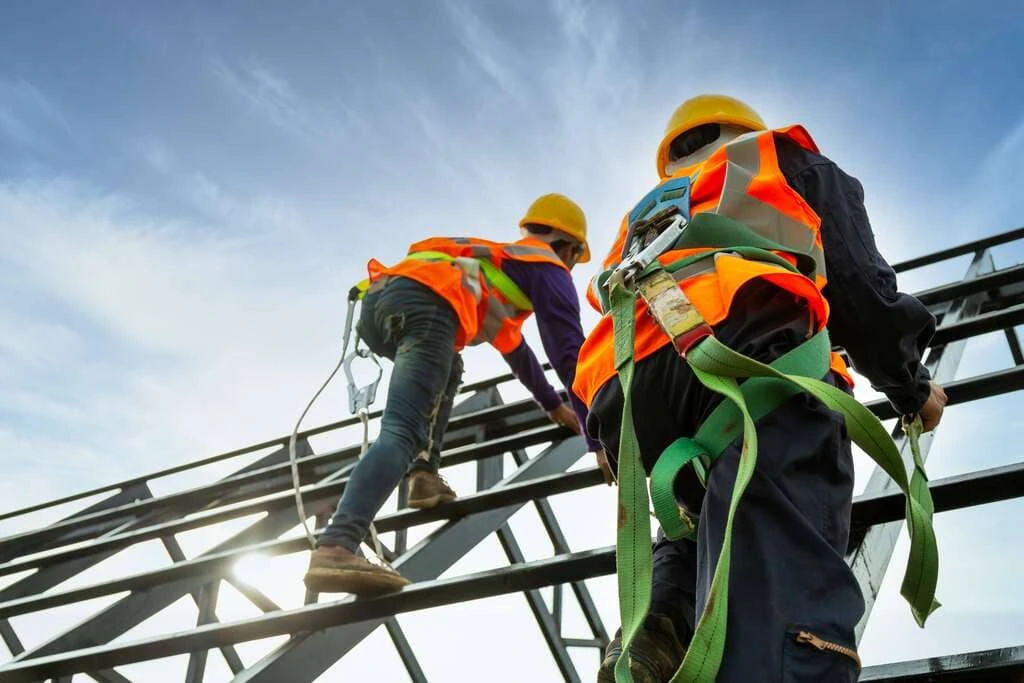
In 2025, the Risk Assessment Softwares are reshaping how safety leaders handle workplace hazards. From oil fields to factory floors,...
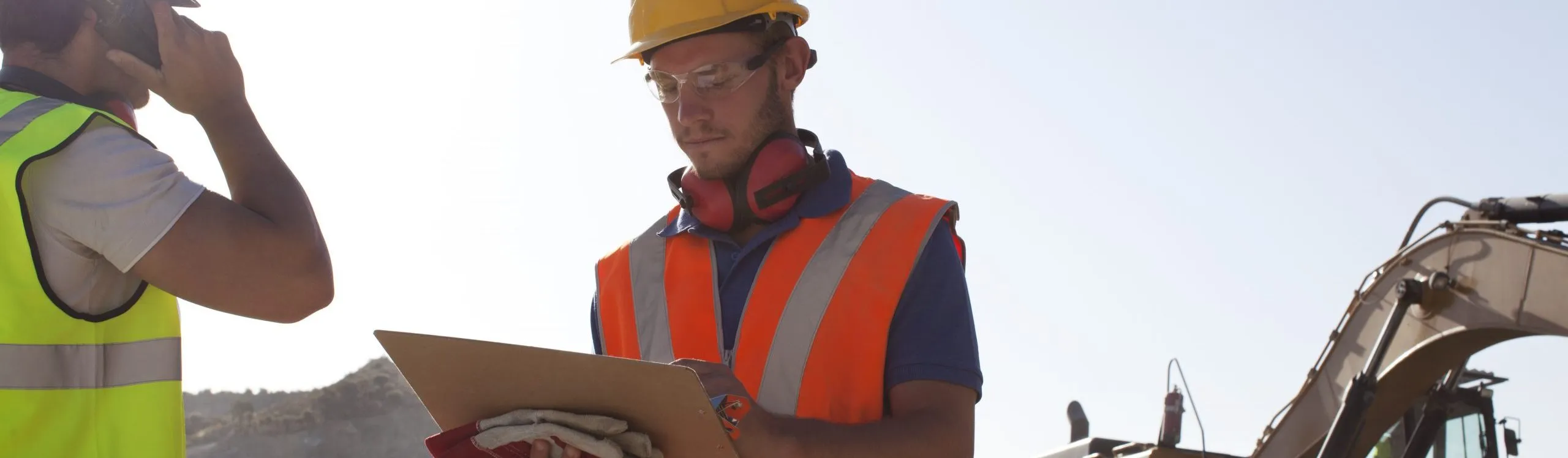
Discover six essential features every top Learning Management System should have to enhance employee training, ensure compliance, and build a...
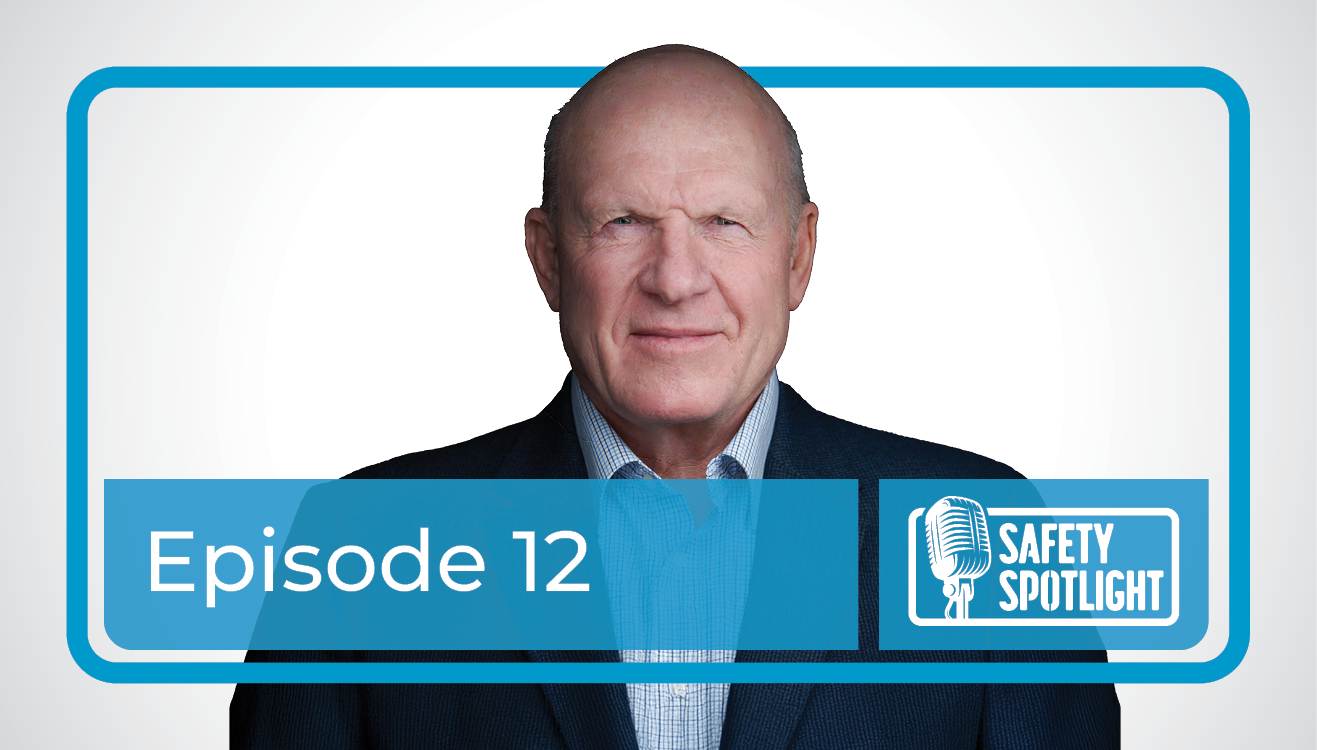
Dr. Tom Krause shares lessons from decades in safety leadership—covering behavior-based safety, decision analysis, and why real change goes beyond...