For Brett Burkard, this truth is key to his approach to workplace safety.
A Rocky Start: From Cowboy Beginnings to Cultural Change
When Titan Environmental began, safety wasn’t top of mind. “To be frank, we were cowboys,” Burkard admits. “It wasn’t our priority.” Starting with just four people working out of a garage, the company’s early approach to safety was rudimentary at best. Burkard recalls safety reports scribbled on the backs of cigarette packs. “It was not good,” he says.
But as the company grew, so did the stakes. Minor incidents piled up, and near-misses served as wake-up calls. “We realized we couldn’t keep going like this,” he says. “We had to make safety a priority, not just for compliance but because it was the right thing to do.”
Burkard’s philosophy was simple: repetition builds habits. Safety meetings, which were once seen as a waste of time, became a daily ritual. “At first, people grumbled,” he recalls. “But over time, it became second nature. And when that happens, you stop having incidents.”
Safety wasn’t just about meetings, though. Burkard emphasized storytelling as a tool for cultural change.
“People don’t connect with numbers. They connect with stories. I’d share real incidents where shortcuts led to tragedy. That’s what sticks with people.“
Brett Burkard – Director
Tying Safety to Accountability
Burkard made safety a part of every operation at Titan from the jump. “We tied safety to daily reports and payroll,” he explains. “If you didn’t submit your safety paperwork, the system wouldn’t process your hours. And if the hours weren’t processed, people didn’t get paid.”
This integration ensured safety wasn’t an afterthought. I was a fundamental part of the workday. Automation played a big role in simplifying the process. “No more paperwork,” Burkard says. “It’s all done on phones. And when something’s easy, people actually do it.”
But technology alone wasn’t enough. Burkard understood that not everyone on a construction site was tech-savvy. “We had some old-school, alpha-male types who weren’t keen on automation,” he says. “So we told them, ‘You’re not responsible for doing it. You’re responsible for making sure it gets done.’”
The company delegated the task to younger, tech-savvy workers. This ensured compliance without resistance. “It was a game-changer,” Burkard says. “The paperwork came in, and everyone was happy.”
Titan’s approach also extended to accountability at all levels. They train supervisors to lead by example, ensuring safety protocols were always followed. “You can’t just talk about safety; you have to live it,” Burkard explains. “If the boss isn’t wearing their PPE, why would anyone else?”
Incentivizing Safety
Burkard also recognized the importance of incentivizing safety. At Titan, management rewarded safety coordinators for their efforts. “We gave them extra per diems,” he says. “If you were the safety lead on a site, maybe you got your own room instead of shared accommodations. Little things like that made a big difference.”
These incentives improved compliance and boosted morale. “When you recognize people for doing the right thing, it changes the culture,” Burkard says. “Safety stopped feeling like a chore and started feeling like something people wanted to do.”
Burkard also used recognition ceremonies to highlight outstanding safety practices. “We’d call people out in meetings and give them a round of applause,” he recalls. “It’s amazing how much a simple thank-you can motivate people.”
Lessons Learned: The High Cost of Complacency
Burkard’s early experiences in construction shaped his approach to safety. “I worked for companies that didn’t give a damn,” he says. “I spent a year working in pits with no shoring. Chunks of dirt would fall in, and we just kept going. We didn’t know any better.”
But those lessons came at a cost. Burkard recalls stories of colleagues who weren’t as lucky. One friend’s father, a lifelong construction worker, was killed in a cave-in. Another incident left a co-worker paralyzed. “It’s not like the movies,” Burkard says. “When something goes wrong, it’s instant. And it’s permanent.”
These experiences left a lasting impression. “When I started my own company, I knew we had to care,” he says. “We had to do better.”
“When you’ve done a job a thousand times, it’s easy to think nothing can go wrong, but that’s when you’re most at risk.“
Brett Burkard – Director
Looking Ahead: The Role of Technology in Safety
Although Burkard is retired, he remains optimistic about the future of safety. “Technology is the key,” he says. “Anything that simplifies safety and makes it easier for people to do their jobs is a win.”
From automation to AI, Burkard sees endless possibilities for innovation. Examples include digital platforms that track safety compliance. Also, wearable tech that monitors fatigue, and AI tools that predict hazards. “We’re only scratching the surface,” he says.
But he cautions against relying solely on tech. “You still need people to care,” he says. “Technology can help, but it can’t replace the human element.”
For Burkard, the future of safety lies in balance, combining the efficiency of automation with the empathy of leadership. “At the end of the day, it’s about making safety a part of the culture,” he says. “When it’s part of who you are, that’s when the real change happens.”
Burkard also envisions a future where safety training becomes more engaging. He believes that virtual reality and gamified training could change the industry. Interactive workshops could help, too. “People learn best when they’re engaged,” he says. “The more we can make training immersive, the better the results.”
Conclusion
Brett Burkard’s career is a story of transformation, both personal and professional. From his cowboy beginnings to building a culture of safety at Titan Environmental, he proved that safety isn’t just about rules. It’s about mindset, repetition, and a willingness to evolve.
And while he may have stepped away from the job site, Burkard’s legacy lives on in the systems, policies, and people he inspired. His message is clear: safety isn’t complicated. It’s about caring enough to make it a priority. And when you do, the results speak for themselves.
Work smart. Stay strong. Speak up.
Related Articles
- All Posts
- #EmergencyPreparedness
- 2025 safety trends
- 360 Immersive
- 360immersive
- 6S Safety
- accident prevention
- accidental careers
- adjustable workstations
- adult education
- AI automation
- AI implementation
- AI in business
- AI in operations
- AI in Safety
- AI podcast
- AI strategy
- AI transformation
- Alberta safety courses
- Allan James Moore
- artificial intelligence
- asking for help
- audit findings
- audit readiness
- Audit Reporting
- automation in safety
- automation strategy
- avoidable injuries
- awareness
- Aztec Safety
- back strain
- BambooHR integration
- behavior-based safety
- Behavioral Safety
- behavioural safety
- biometric sensors
- BIS Podcast
- BIS Safety Podcasts
- BIS Safety Software
- BIS Safety Spotlight
- black holes
- Blame Culture
- BP Texas City Explosion
- Brave Leadership
- Brett Burkard
- burnout
- business automation
- Canadian OHS
- Canadian safety
- Canadian safety history
- Canadian safety standards
- carbon monoxide
- Carolynne Heron
- CCOHS
- chemical
- chemical vapors
- chronic injuries
- chronic pain
- cloud-based safety tools
- Coming Soon
- community safety programs
- Competency in Safety
- complacency in safety
- Compliance
- compliance courses
- Compliance In Canada
- compliance issues
- Compliance management
- Compliance Reporting
- compliance software
- compliance tools
- compliance tracking
- compliance training
- compliance vs protection
- Construction advocacy
- Construction education
- Construction industry
- construction safety
- construction safety training
- continuous improvement
- continuous safety improvement
- corporate culture
- corporate training
- corrective actions
- crane
- CSA standards
- Customer Spotlight
- Customer Spotlight Kevin Swinden Global Hazmat Safety Culture Hazmat Management Dangerous Goods Competency in Safety Workplace Risk Mitigation BIS Training Clients Canadian EHS
- customized training
- daily trip inspection
- Damage Prevention
- Dangerous Goods
- dangerous goods classification
- Danny Sellers
- data-driven safety
- Decision Analysis
- defect management
- defect tracking
- defensive driving
- DEI in onboarding
- digital compliance
- digital forms
- Digital Hazard Reporting
- Digital Onboarding
- digital safety
- Digital Safety Audits
- Digital safety systems
- digital safety tools
- digital safety transformation
- Digital Training Tools
- digital transformation
- DMS features
- document control
- document management system
- Dr. Joanna Pagonis
- Dr. Tom Krause
- driver file management
- driver training
- driving instructor program
- DTRMS
- e-learning
- e-learning tools
- eadership in safety
- early intervention
- education technology
- EHS
- EHS Adoption
- EHS Compliance
- EHS digital solutions
- EHS Inspections
- EHS Onboarding
- EHS software
- EHS systems
- EHS tools
- Einstein
- electrical safety
- Emergency Action Plan
- emergency preparedness
- emergency response
- emergency supplies
- emotional training
- employee behavior
- employee engagement
- employee health
- Employee onboarding
- Employee Readiness
- employee safety
- employee training
- Energy Isolation
- ergonomic consulting
- ergonomic design
- ergonomic risks
- ergonomics
- Evacuation Procedures
- evidence collection
- EWI Works
- exoskeleton
- exoskeletons
- failure analysis
- fall protection
- fast onboarding
- field experience
- field level hazard assessments
- field safety
- field safety assessments
- field safety leadership
- field safety services
- Field Safety Technology
- Field-Friendly Software
- Fire Drills
- fire prevention
- Fire Safety Training
- first aid kit
- first week on the job
- first workplace injury
- fleet management
- fleet safety
- FLHA engagement
- FLHA Integration
- FLHA software
- FMEA
- freight
- Frontline Engagement
- frontline safety
- fuel handling
- future of work
- Global Hazmat
- global onboarding
- gravitational waves
- gut feeling in safety
- hand injuries
- handling hazardous materials
- hands-on training
- hazard analysis
- hazard assessment compliance
- Hazard Awareness
- hazard communication
- Hazard Identification
- hazard prevention
- hazard recognition
- Hazardous Energy Control
- Hazmat Management
- Health & Safety Podcast
- health and safety
- hearing loss prevention
- hearing protection
- heavy equipment safety
- hidden workplace hazards
- high voltage systems
- HR automation
- HR software
- human factors
- human factors in safety
- human in the loop
- Human Performance
- human vs machine
- human-centered design
- human-centered safety
- humor in safety
- ICBC certification
- identification
- immersive learning
- Imposter Syndrome
- incident data
- incident investigation
- incident prevention
- incident reporting
- industrial AI
- Industrial Hygiene
- industrial safety
- influence vs control
- Infrastructure Risk
- injury consequences
- injury prevention
- injury prevention tips
- injury recovery
- injury reporting
- injury response
- injury response plan
- instructor development
- internal audits
- international workforce
- interpreting safety data
- invisible dangers
- ISO standards
- Jeff Mulligan
- Jennifer Lastra
- job site accountability
- job site hazards
- job site risks
- job site safety
- jobsite readiness
- Jody Young
- KBR Safety Training
- Kevin Swinden
- labor movement
- ladder safety
- Leadership
- leadership accountability
- leadership and empathy
- Leadership in Safety
- Leadership Management
- leadership messaging
- Lean Manufacturing
- Lean Workplace
- learning from incidents
- learning management
- lifting techniques
- LIGO
- Linda Miller
- LMS
- LMS features
- LMS software
- Lock Out Tag Out
- lockout tagout
- lone workers
- LOTO
- machine learning
- Machine Safety
- Maintenance Safety
- mental health at work
- MI Safety
- microlearning
- Mike Schwartz
- minor injuries
- mobile onboarding
- Mobile Safety Apps
- Mobile Safety Platforms
- Mobile Safety Tools
- movement in workplace
- multilingual training
- MyZone AI
- Near Miss Reporting
- new hire experience
- New Hire Safety
- New Worker Training
- new workers
- no-blame investigations
- noise exposure
- nonconformance
- Northern BC
- NRCA
- NSC Standard 13
- occupational fatigue
- occupational hazards
- occupational health
- occupational safety
- occupational therapy
- OH&S
- OHS
- OHSA
- oil and gas safety
- omni-training
- onboarding safety
- Onboarding Software
- online learning
- Online safety training
- operational efficiency
- Operational Excellence
- organizational culture
- organizational safety
- OSHA compliance
- OSHA standards
- outdated practices
- overconfidence
- overhead crane courses
- pain awareness
- personal protective equipment
- Pharmaceutical Safety
- physics careers
- pipeline safety
- podcast
- post-accident review
- post-incident protocol
- PPE
- PPE enforcement
- PPE improvement
- pre-trip inspection
- predictive analytics
- pretrip inspection
- preventive action
- proactive safety
- proactive safety measures.
- Proactive Safety Systems
- process improvement
- Professional development
- propane safety
- propane storage
- protective clothing
- psychological hazards
- psychological safety
- quality control
- quality management
- quality standard
- Real Safety Leadership
- Real-Time Reporting
- real-time safety
- recordkeeping
- regulatory updates
- repetition in safety
- repetitive motion injuries
- respirator safety
- respirators
- risk assessment
- risk management
- risk mitigation
- risk prevention
- Risk Prevention Tools
- risk reduction
- road safety
- Robin Postnikoff
- ROI with AI
- root cause analysis
- root cause correction
- routine task risks
- safe habits
- safe transport
- safe work habits
- safety
- safety accountability
- safety advice
- safety article
- Safety Audit Software
- safety automation
- safety awareness
- safety best practices
- safety communication
- safety compliance
- Safety Conversations
- safety culture
- safety data
- safety data sheets
- safety documentation
- safety engagement
- safety follow-up
- safety gear
- safety gloves
- safety goggles
- safety habits
- safety incentives
- safety innovation
- safety insights
- safety inspection
- safety instinct
- Safety Leaders
- safety leadership
- Safety Leadership Podcast
- safety legislation
- safety lessons
- safety management
- safety management system
- safety management systems
- safety metrics
- safety mindset
- safety motivation.
- safety myths
- safety onboarding
- safety planning
- safety podcast
- safety procedure updates
- Safety Procedures
- safety professionals
- safety reporting
- safety review process
- safety shortcuts
- safety software
- Safety Spotlight
- safety systems
- safety technology
- safety theater
- safety tips
- safety training
- safety transformation
- safety transparency
- Sarah Anderson
- scalable training solutions
- Scott Lyall
- shipping documentation
- silent dangers
- silica dust
- Sinogap Solutions
- slow-building hazards
- smart helmets
- smart PPE
- smart safety systems
- smart safety tools
- space science
- Spencer McDonald
- Standardized Work
- storytelling and safety
- storytelling in safety
- supervisor training
- system safety
- TDG
- team communication
- teamwork
- tech and ergonomics
- tech in safety
- tech-enabled learning
- Thinking Driver
- Titan Environmental
- Total Recordable Injury Formula
- tough guy mentality
- toxic air
- training
- training courses
- Training integration
- training management
- training matrix
- training record management
- training records
- training software
- transportation
- transportation of dangerous goods
- Trust and Accountability
- unseen workplace threats
- user experience
- Utility Safety Partners
- values-based onboarding
- vehicle safety
- version control
- veteran advice
- Virtual Reality
- VR safety training
- VR Technology
- wearable technology
- WHMIS
- witness statements
- women in leadership
- work-alone training
- work-related injuries
- worker accountability
- worker advocacy
- worker fatigue
- worker protection
- worker safety
- worker safety habits
- worker safety tips
- worker trust
- worker wellbeing
- workers' rights
- Workforce Automation
- workforce compliance
- Workforce development
- workforce engagement
- workforce management
- Workforce Readiness
- workforce training
- workplace accidents
- workplace air quality
- workplace best practices
- workplace certification
- workplace compliance
- Workplace Culture
- Workplace Hazard Tracking
- workplace hazards
- workplace health
- workplace incident response
- workplace injuries
- workplace injury prevention
- workplace mindset
- Workplace Organization
- workplace risk factors
- workplace risk management
- Workplace Risk Mitigation
- Workplace safety
- workplace safety culture
- Workplace Safety Leadership
- workplace safety rules
- workplace safety tech
- workplace safety tips
- Workplace Safety Tools
- workplace safety training
- workplace stress
- workplace tiredness
- workplace wellness
- WSPS

Discover how Catlin Chiasson uses empathy, storytelling, and real-world experience to drive lasting safety culture on the front lines.
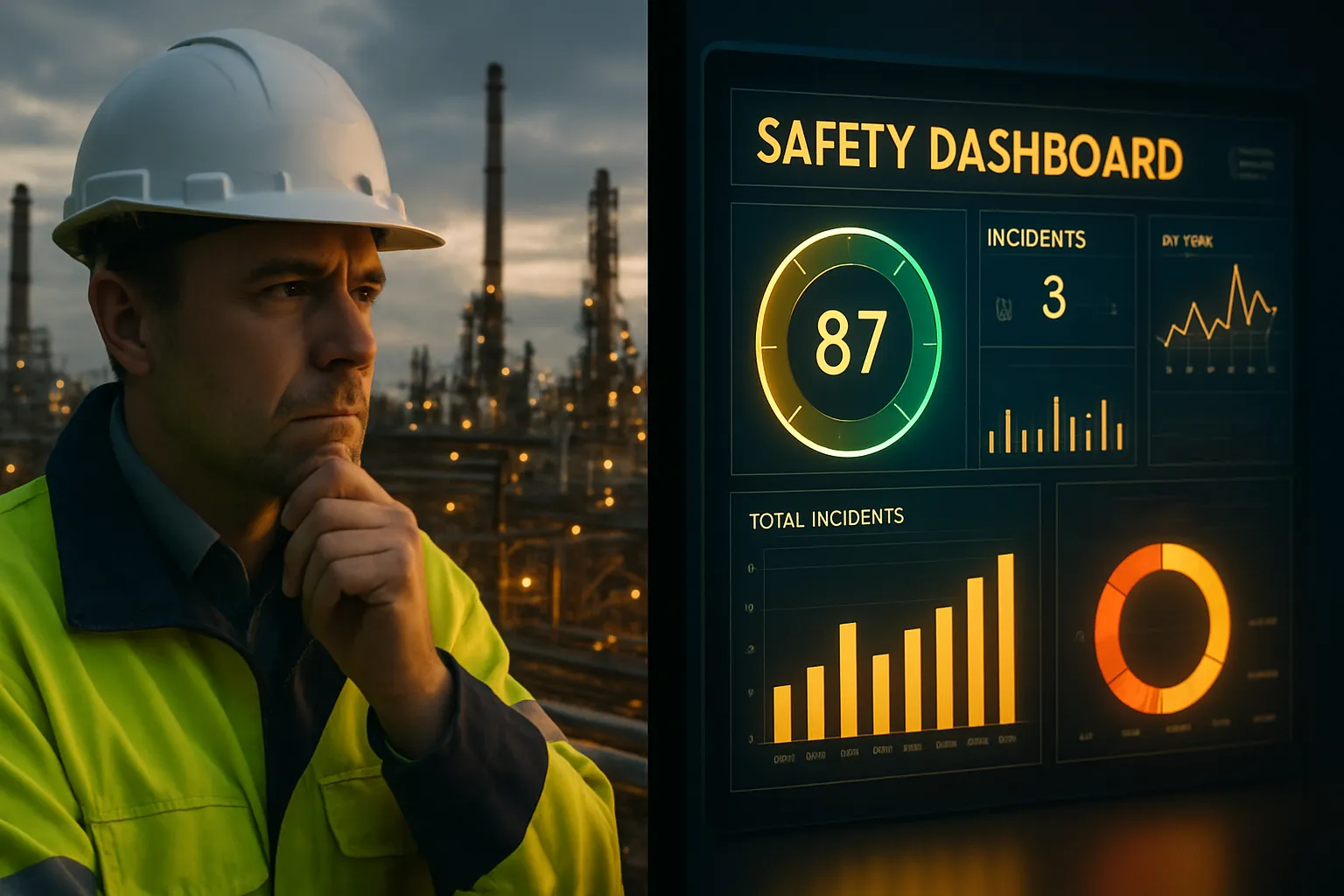
Even in a data-driven world, safety instinct still matters. Learn how gut feelings and analytics work together to create deeper,...
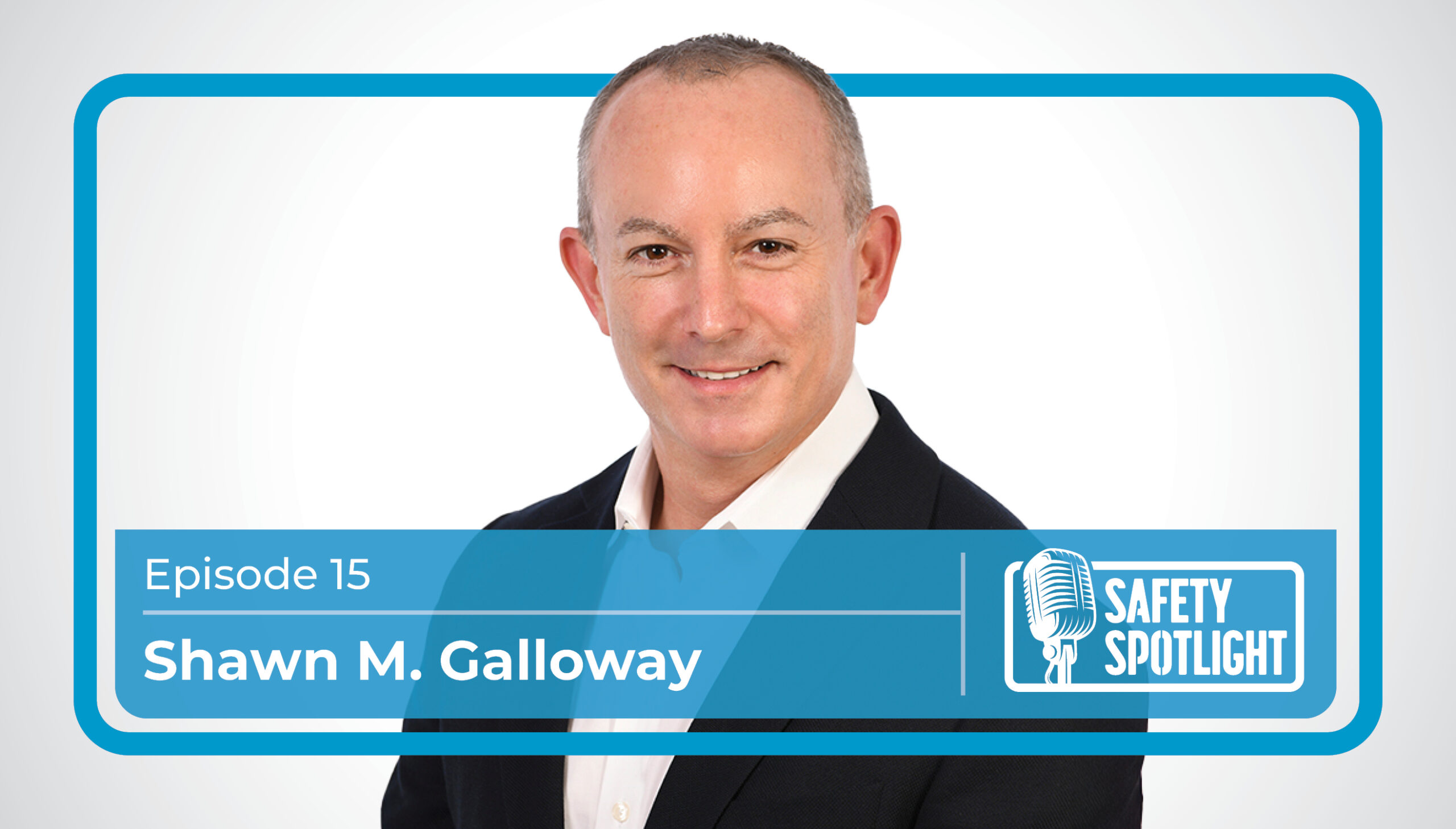
In this episode, global safety strategist Shawn Galloway breaks down what it really takes to achieve safety excellence.