That was Sarah Anderson’s original plan. Then everything changed.
Why Real-World Experience Shapes Better Safety Leaders
A catastrophe. An industrial disaster in India, one of the deadliest in history, made her rethink everything. Instead of staying outside the gates protesting, she decided to go inside.
“I figured I’d be more effective from within,” she says. She gave up her scholarship at the University of Illinois and transferred to Purdue to study industrial hygiene. She hadn’t even heard of the field before, but she knew it was the right move.
That decision led her deep into heavy industry. She’s spent her career making work safer, challenging perceptions. Anderson – now with Brystol Myers Squibb Pharmaceuticals, is pushing companies to take risk more seriously. From aluminum smelters to oil refineries, Anderson built her career on asking hard questions. She’s making workplaces safer, one difficult conversation at a time.
Trial by Fire: Entering a Male-Dominated Industry
Anderson’s first real exposure to industrial safety came at an aluminum smelter. It was a rough introduction. “I was young, inexperienced, and working in a unionized facility that had no mercy,” she says. “They didn’t care if I was new or that I was an intern. No one was going to take it easy on me.”
She quickly realized she wasn’t seen as an ally. “Workers didn’t think I was there to help them,” she says. “They saw me as part of corporate, another outsider who didn’t understand their world.”
That early experience shaped her approach to safety. “I thought people would automatically see I was there to protect them,” she says. “That’s not how it works. You have to build trust first.”
She learned to listen before speaking, to spend time in the field instead of the office. “You can’t just walk in and tell people what to do,” she says. “You have to show them you understand, that you respect what they do. Otherwise, they’ll tune you out.”
She also realized that building relationships with workers was about being present. It couldn’t just be speeches. “I made it a point to be on-site, not only in meetings,” she says. “People trust you more when they see you walking the same ground, wearing the same PPE. They trust you understand the challenges they face firsthand.”
The Moment That Changed Everything
Anderson’s commitment to safety was solidified during a tragic incident at an oil refinery. She and her husband, both working in the industry at the time, were driving back to work when they saw it: a black mushroom cloud rising into the sky.
“I turned to my husband and said, ‘That’s Texas City. There’s no way people didn’t die,’” she recalls.
She was right. A massive explosion had ripped through the BP Texas City refinery. She felt the shockwave in her car. “We saw it, then we heard it, then we felt it,” she says.
In the aftermath, she helped with investigations, root cause analyses, and compliance audits. The lessons were brutal but necessary. “That disaster changed everything,” she says. “It forced new safety regulations, better controls, and tighter oversight. But it came at a terrible cost.”
She believes the most dangerous companies aren’t the ones that experience accidents, it’s the ones that think they’re too good to fail. “If a company cuts back on maintenance, that’s a bad sign. If they cut internal audits, ignore engineering recommendations, that’s a red flag,” she says. “That’s where disasters happen.”
She also stresses that complacency is one of the biggest threats to safety. “When leadership believes they’re above failure, they stop looking for risks. And when you stop looking, you stop preventing.”
Building Trust with Workers: A Safety Lesson in the Field
One of Anderson’s key lessons came from an everyday job-site encounter. She spotted a worker straddling a 14-foot gap between a rooftop and a steel beam, completely untied.
“I didn’t want to startle him, so I motioned for him to step back onto the roof,” she says. “Then I met him on the ground.”
She sat with him in the break room, away from the site, and laid it out plainly. “I told him, ‘You’re close to retirement. You don’t need to go home in a box.’”
He admitted he hadn’t even thought about it. He was just trying to get the job done quickly. “I reminded him that it only takes a second for everything to go wrong,” she says. “And that split-second decision could cost him everything.”
Later, when she reported the incident to his managers, they weren’t surprised. “They already knew he worked like that,” she says. “And no one had done anything.”
That moment cemented one of her core beliefs: ignoring unsafe behavior is the same as endorsing it. “If leadership knows a problem exists and doesn’t act, they’re just as responsible,” she says.
She also emphasizes that accountability isn’t about punishment, it’s about prevention.
“You don’t want to catch someone after they’ve already made a mistake. You want to set up a culture where they don’t make that mistake in the first place“
Sarah Anderson – Global Director
AI and the Future of Safety
Anderson sees artificial intelligence as the next frontier in workplace safety. “We already have gas detection systems that warn workers about unsafe air quality,” she says. “Imagine if AI could do the same for every kind of hazard.”
She envisions AI systems that predict risks in real time, alerting workers to hazards. Black ice, unstable structures, or dangerous weather patterns noted before they become a problem. “Think about how lifeguards use drones to detect sharks,” she says. “Why can’t we do the same for job sites?”
She acknowledges the privacy concerns. “There’s a fine line between protecting workers and making them feel like they’re under surveillance,” she says. “We need to use AI as a tool for prevention, not punishment.”
More than anything, she wants AI to be used for recognition, not just rule enforcement. “We should be tracking good decisions, not just bad ones,” she says. “AI should help reward proactive safety behaviors, not just flag violations.”
She also believes AI can make safety training more effective. “Right now, most training is one-size-fits-all. AI can tailor learning to individuals, reinforcing what they struggle with and cutting down on wasted time.”
The Biggest Challenge in Safety Today
According to Anderson, the biggest issue in workplace safety isn’t technology, training, or even compliance, it’s perception.
“Risk tolerance varies from person to person,” she says. “Some people will take every precaution. Others think, ‘I’ve done this a hundred times, nothing’s happened.’ That mindset is dangerous.”
The people with the most influence in an organization, those controlling budgets, making decisions, set the tone. “If leadership doesn’t see safety as a priority, it won’t be,” she says. “They decide where resources go. They decide what’s worth fixing. If they ignore risk, it trickles down to every level.”
Anderson believes that at its core, safety is about influence. “We don’t control the company. We don’t control the budget. What we control is how we communicate, how we frame risk, how we get buy-in.”
Her approach? Always bring solutions. “I never just present a problem,” she says. “I bring three solutions, budget, mid-range, and premium. That way, leadership isn’t deciding whether to fix something, they’re deciding how.”
Final Thoughts: Leading Through Influence
Disasters shaped Anderson’s career. She’s relentless in her belief that safety should never be an afterthought. She knows that leadership, trust, and communication are what make the difference. A workplace that values safety and one that just checks the boxes are a world apart.
“We influence. That’s our job,” she says. “We don’t own the company. We don’t control the money. But we control how we communicate risk. We control how we get people to care.”
That, she believes, is the key to real change. Not policies. Not punishments. But people.
Work smart. Stay strong. Speak up.
Related Articles
- All Posts
- #EmergencyPreparedness
- 2025 safety trends
- 360 Immersive
- 360immersive
- 6S Safety
- accident prevention
- accidental careers
- adjustable workstations
- adult education
- AI automation
- AI implementation
- AI in business
- AI in operations
- AI in Safety
- AI podcast
- AI strategy
- AI transformation
- Alberta safety courses
- Allan James Moore
- artificial intelligence
- asking for help
- audit findings
- audit readiness
- Audit Reporting
- automation in safety
- automation strategy
- avoidable injuries
- awareness
- Aztec Safety
- back strain
- BambooHR integration
- behavior-based safety
- Behavioral Safety
- behavioural safety
- biometric sensors
- BIS Podcast
- BIS Safety Podcasts
- BIS Safety Software
- BIS Safety Spotlight
- black holes
- Blame Culture
- BP Texas City Explosion
- Brave Leadership
- Brett Burkard
- burnout
- business automation
- Canadian OHS
- Canadian safety
- Canadian safety history
- Canadian safety standards
- carbon monoxide
- Carolynne Heron
- CCOHS
- chemical
- chemical vapors
- chronic injuries
- chronic pain
- cloud-based safety tools
- Coming Soon
- community safety programs
- Competency in Safety
- complacency in safety
- Compliance
- compliance courses
- Compliance In Canada
- compliance issues
- Compliance management
- Compliance Reporting
- compliance software
- compliance tools
- compliance tracking
- compliance training
- compliance vs protection
- Construction advocacy
- Construction education
- Construction industry
- construction safety
- construction safety training
- continuous improvement
- continuous safety improvement
- corporate culture
- corporate training
- corrective actions
- crane
- CSA standards
- Customer Spotlight
- Customer Spotlight Kevin Swinden Global Hazmat Safety Culture Hazmat Management Dangerous Goods Competency in Safety Workplace Risk Mitigation BIS Training Clients Canadian EHS
- customized training
- daily trip inspection
- Damage Prevention
- Dangerous Goods
- dangerous goods classification
- Danny Sellers
- data-driven safety
- Decision Analysis
- defect management
- defect tracking
- defensive driving
- DEI in onboarding
- digital compliance
- digital forms
- Digital Hazard Reporting
- Digital Onboarding
- digital safety
- Digital Safety Audits
- Digital safety systems
- digital safety tools
- digital safety transformation
- Digital Training Tools
- digital transformation
- DMS features
- document control
- document management system
- Dr. Joanna Pagonis
- Dr. Tom Krause
- driver file management
- driver training
- driving instructor program
- DTRMS
- e-learning
- e-learning tools
- eadership in safety
- early intervention
- education technology
- EHS
- EHS Adoption
- EHS Compliance
- EHS digital solutions
- EHS Inspections
- EHS Onboarding
- EHS software
- EHS systems
- EHS tools
- Einstein
- electrical safety
- Emergency Action Plan
- emergency preparedness
- emergency procedures
- emergency response
- emergency supplies
- emotional training
- employee behavior
- employee engagement
- employee health
- Employee onboarding
- Employee Readiness
- employee safety
- employee training
- Energy Isolation
- ergonomic consulting
- ergonomic design
- ergonomic risks
- ergonomics
- Evacuation Procedures
- evidence collection
- EWI Works
- exoskeleton
- exoskeletons
- failure analysis
- fall protection
- fast onboarding
- field experience
- field level hazard assessments
- field operations
- field safety
- field safety assessments
- field safety leadership
- field safety services
- Field Safety Technology
- Field-Friendly Software
- Fire Drills
- fire prevention
- Fire Safety Training
- first aid kit
- first week on the job
- first workplace injury
- fleet management
- fleet safety
- FLHA engagement
- FLHA Integration
- FLHA software
- FMEA
- freight
- Frontline Engagement
- frontline safety
- fuel handling
- future of work
- Global Hazmat
- global onboarding
- gravitational waves
- gut feeling in safety
- hand injuries
- handling hazardous materials
- hands-on training
- hazard analysis
- hazard assessment compliance
- Hazard Awareness
- hazard communication
- Hazard Identification
- hazard prevention
- hazard recognition
- Hazardous Energy Control
- Hazmat Management
- Health & Safety Podcast
- health and safety
- hearing loss prevention
- hearing protection
- heavy equipment safety
- hidden workplace hazards
- high voltage systems
- HR automation
- HR software
- human factors
- human factors in safety
- human in the loop
- Human Performance
- human vs machine
- human-centered design
- human-centered safety
- humor in safety
- ICBC certification
- identification
- immersive learning
- Imposter Syndrome
- incident data
- incident investigation
- incident prevention
- incident reporting
- industrial AI
- Industrial Hygiene
- industrial safety
- influence vs control
- Infrastructure Risk
- injury consequences
- injury prevention
- injury prevention tips
- injury recovery
- injury reporting
- injury response
- injury response plan
- instructor development
- internal audits
- international workforce
- interpreting safety data
- invisible dangers
- ISO standards
- Jeff Mulligan
- Jennifer Lastra
- job site accountability
- job site hazards
- job site risks
- job site safety
- jobsite readiness
- Jody Young
- KBR Safety Training
- Kevin Swinden
- labor movement
- ladder safety
- Leadership
- leadership accountability
- leadership and empathy
- Leadership in Safety
- Leadership Management
- leadership messaging
- Lean Manufacturing
- Lean Workplace
- learning from incidents
- learning management
- lifting techniques
- LIGO
- Linda Miller
- LMS
- LMS features
- LMS software
- Lock Out Tag Out
- lockout tagout
- lone workers
- LOTO
- machine learning
- Machine Safety
- Maintenance Safety
- mental health at work
- MI Safety
- microlearning
- Mike Schwartz
- minor injuries
- mobile onboarding
- Mobile Safety Apps
- Mobile Safety Platforms
- Mobile Safety Tools
- movement in workplace
- multilingual training
- MyZone AI
- Near Miss Reporting
- new hire experience
- New Hire Safety
- New Worker Training
- new workers
- no-blame investigations
- noise exposure
- nonconformance
- Northern BC
- NRCA
- NSC Standard 13
- occupational fatigue
- occupational hazards
- occupational health
- occupational safety
- occupational therapy
- OH&S
- OHS
- OHSA
- oil and gas safety
- omni-training
- onboarding safety
- Onboarding Software
- online learning
- Online safety training
- operational efficiency
- Operational Excellence
- organizational culture
- organizational safety
- OSHA compliance
- OSHA standards
- outdated practices
- overconfidence
- overhead crane courses
- pain awareness
- personal protective equipment
- Pharmaceutical Safety
- physics careers
- pipeline safety
- podcast
- post-accident review
- post-incident protocol
- PPE
- PPE enforcement
- PPE improvement
- pre-trip inspection
- predictive analytics
- pretrip inspection
- preventive action
- proactive safety
- proactive safety measures.
- Proactive Safety Systems
- process improvement
- Professional development
- propane safety
- propane storage
- protective clothing
- psychological hazards
- psychological safety
- quality control
- quality management
- quality standard
- Real Safety Leadership
- Real-Time Reporting
- real-time safety
- recordkeeping
- regulatory updates
- repetition in safety
- repetitive motion injuries
- respirator safety
- respirators
- risk assessment
- risk management
- risk mitigation
- risk prevention
- Risk Prevention Tools
- risk reduction
- road safety
- Robin Postnikoff
- ROI with AI
- root cause analysis
- root cause correction
- routine task risks
- safe habits
- safe transport
- safe work habits
- safety
- safety accountability
- safety advice
- safety article
- Safety Audit Software
- safety automation
- safety awareness
- safety best practices
- safety communication
- safety compliance
- Safety Conversations
- safety culture
- safety data
- safety data sheets
- safety documentation
- safety engagement
- safety follow-up
- safety gear
- safety gloves
- safety goggles
- safety habits
- safety incentives
- safety innovation
- safety insights
- safety inspection
- safety instinct
- Safety Leaders
- safety leadership
- Safety Leadership Podcast
- safety legislation
- safety lessons
- safety management
- safety management system
- safety management systems
- safety metrics
- safety mindset
- safety motivation.
- safety myths
- safety onboarding
- safety planning
- safety podcast
- safety procedure updates
- Safety Procedures
- safety professionals
- safety reporting
- safety review process
- safety shortcuts
- safety software
- Safety Spotlight
- safety systems
- safety technology
- safety theater
- safety tips
- safety training
- safety transformation
- safety transparency
- Sarah Anderson
- scalable training solutions
- Scott Lyall
- shipping documentation
- silent dangers
- silica dust
- Sinogap Solutions
- slow-building hazards
- smart helmets
- smart PPE
- smart safety systems
- smart safety tools
- SOPs
- space science
- Spencer McDonald
- Standardized Work
- storytelling and safety
- storytelling in safety
- supervisor training
- system safety
- TDG
- team communication
- teamwork
- tech and ergonomics
- tech in safety
- tech-enabled learning
- Thinking Driver
- Titan Environmental
- Total Recordable Injury Formula
- tough guy mentality
- toxic air
- training
- training courses
- Training integration
- training management
- training matrix
- training record management
- training records
- training software
- transportation
- transportation of dangerous goods
- Trust and Accountability
- unseen workplace threats
- user experience
- Utility Safety Partners
- values-based onboarding
- vehicle safety
- version control
- veteran advice
- Virtual Reality
- VR safety training
- VR Technology
- wearable technology
- WHMIS
- witness statements
- women in leadership
- work-alone training
- work-related injuries
- worker accountability
- worker advocacy
- worker fatigue
- worker protection
- worker safety
- worker safety habits
- worker safety tips
- worker trust
- worker wellbeing
- workers' rights
- Workforce Automation
- workforce compliance
- Workforce development
- workforce engagement
- workforce management
- Workforce Readiness
- workforce training
- workplace accidents
- workplace air quality
- workplace best practices
- workplace certification
- workplace compliance
- Workplace Culture
- Workplace Hazard Tracking
- workplace hazards
- workplace health
- workplace incident response
- workplace injuries
- workplace injury prevention
- workplace mindset
- Workplace Organization
- workplace risk factors
- workplace risk management
- Workplace Risk Mitigation
- Workplace safety
- workplace safety culture
- Workplace Safety Leadership
- workplace safety rules
- workplace safety tech
- workplace safety tips
- Workplace Safety Tools
- workplace safety training
- workplace stress
- workplace tiredness
- workplace wellness
- WSPS
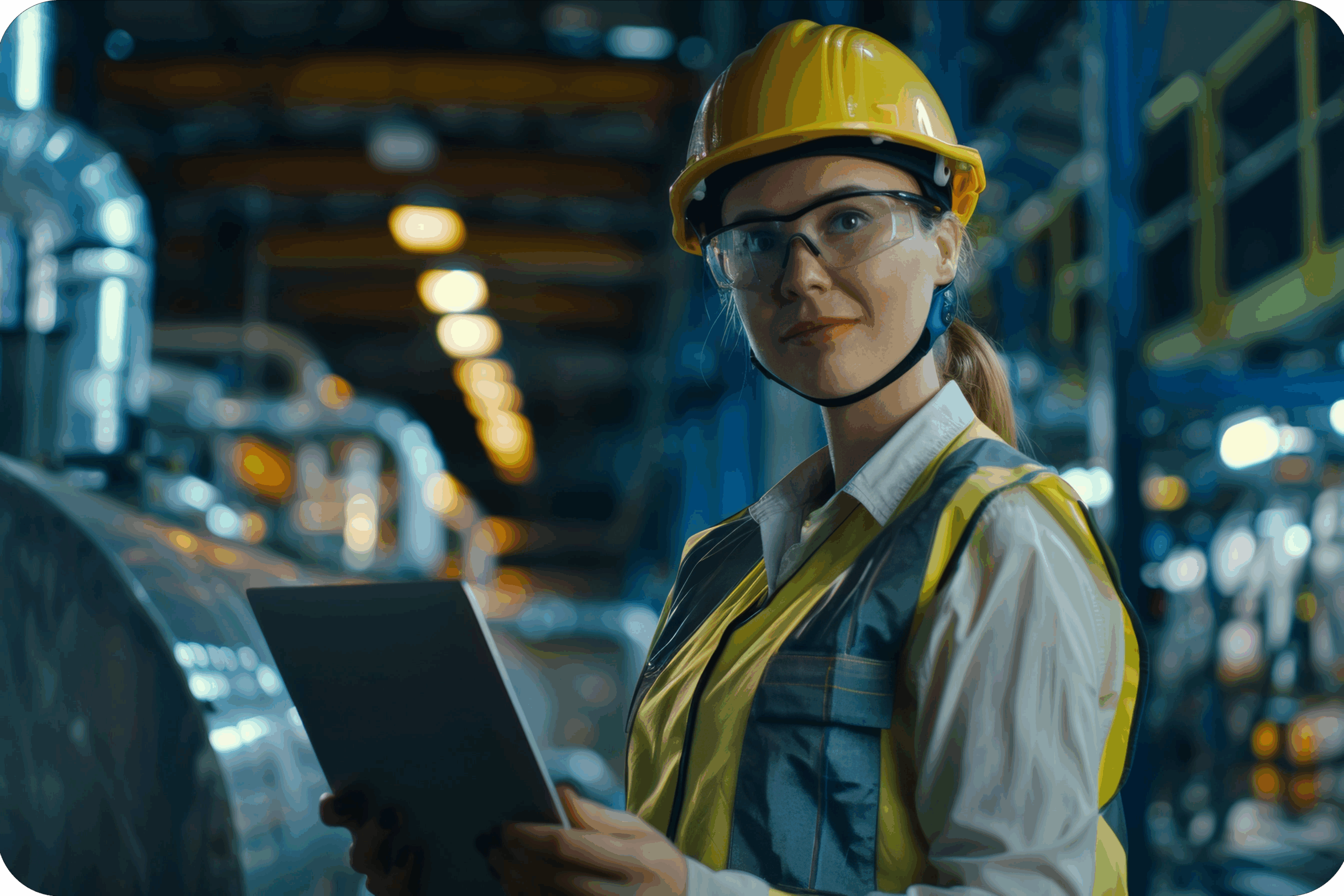
Strong, accessible documentation is key to safer, more efficient worksites. Learn why it matters, where it fails, and how to...

Discover how Catlin Chiasson uses empathy, storytelling, and real-world experience to drive lasting safety culture on the front lines.
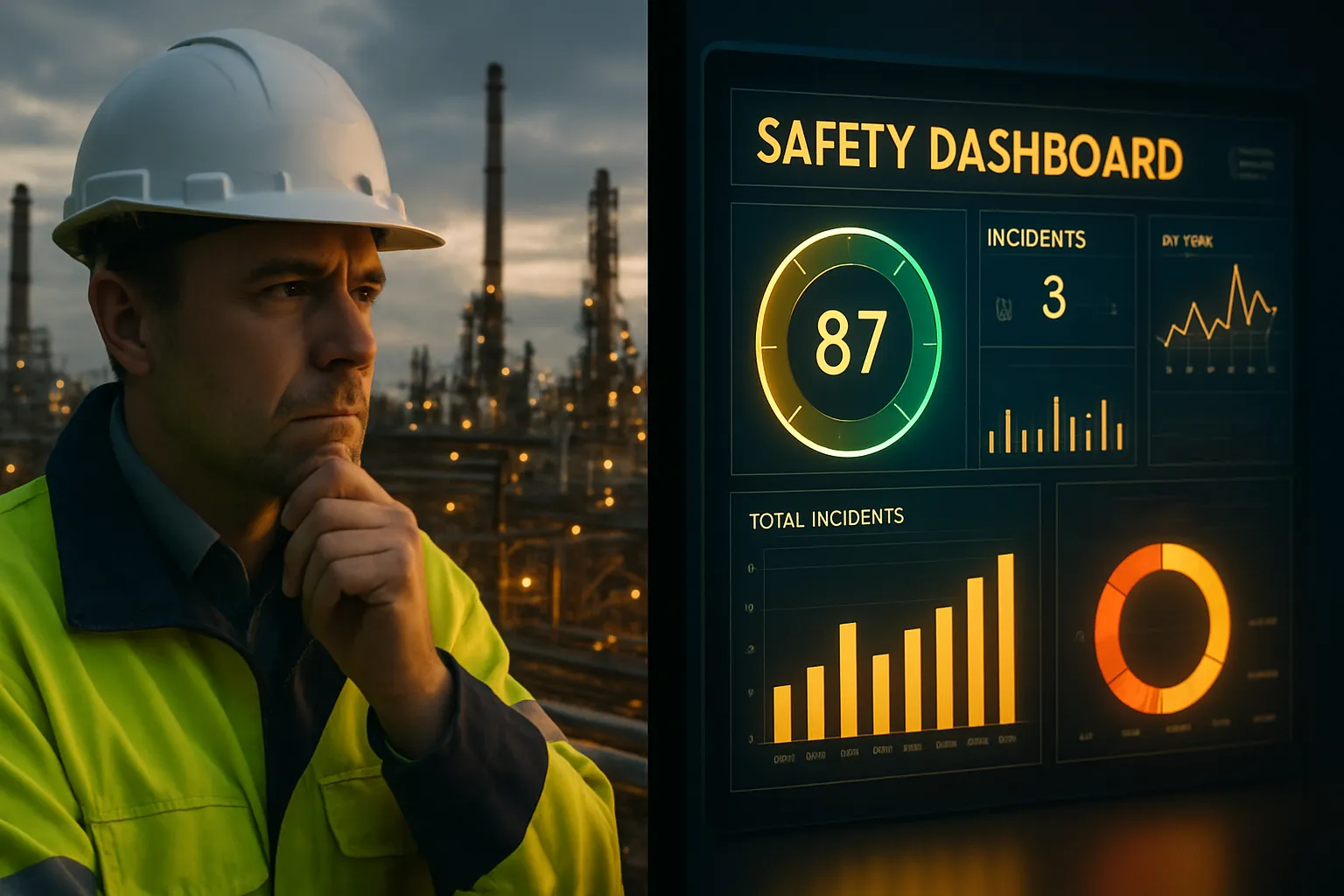
Even in a data-driven world, safety instinct still matters. Learn how gut feelings and analytics work together to create deeper,...