Identifying safety risks is a fundamental step in cultivating a safety-focused culture, the assessment of TRIF is vital for fostering a safer work environment. A low (good) TRIF is a obvious representation of great safety measures, a bad can raise insurance levels and get denied contracts and business.
Explore this Article:
Total Recordable Injury Frequency Formula
The Total Recordable Injury Frequency (TRIF) formula is a simple yet essential metric for measuring workplace safety. It is calculated using the following formula:
The Total Recordable Injury Frequency (TRIF) is calculated using a formula that standardizes the reporting of workplace injuries to compare safety performance across different environments and company sizes.
TRIF = (Number of injuries × 200,000) / Total hours worked<
- Number of injuries: Includes all recordable work-related injuries and illnesses.
- 200,000: Represents the hours worked by 100 full-time employees, assuming a 40-hour week over 50 weeks.
- Total hours worked: The cumulative number of hours worked by all employees during the period being measured.
Example of a TRIF Formula
Here’s an example: For a company with 150 employees recording three injuries last year, the TRIF calculation would be:
(3 x 200,000) / (300,000) = 2
For quarterly calculations, the 200,000 figure is simply adjusted to 50,000, which corresponds to the hours worked by 100 employees in a quarter.
Understanding Why We Track Total Recordable Injury Frequencys:
The primary aim of TRIF is to gauge the effectiveness of a company’s safety measures over the past year and to benchmark against peers in the industry. A high TRIF indicates a need for safety improvements, whereas a low TRIF suggests effective past safety measures. This tracking is particularly critical in high-risk sectors like construction and agriculture.
Advantages and Limitations:
Advantages and limitations of using Total Recordable Injury Frequency (TRIF) metrics can significantly influence how organizations perceive and manage their safety performance:
Advantages:
- Standardized Measurement: TRIF provides a consistent metric that allows businesses across different industries to measure and compare safety performance. This standardization is crucial for benchmarking and understanding relative performance levels.
- Simplicity of Calculation: The formula for TRIF is straightforward, requiring only the number of reported injuries and the total hours worked. This simplicity facilitates easier understanding and implementation within any organization.
- Performance Benchmarking: TRIF enables companies to benchmark their safety records against industry averages or sector-specific standards, which can guide strategic improvements and safety investments.
Limitations:
- Disproportionate Impact on Small Businesses: For smaller companies, a single incident can drastically alter the TRIF, potentially giving a skewed perception of their safety environment. This can lead to unfairly high TRIF scores that might not accurately reflect the company’s overall safety culture.
- Oversimplification of Data: TRIF calculations do not account for the severity or specific nature of injuries, treating minor incidents and major accidents equally. This lack of granularity can obscure deeper safety issues and prevent targeted interventions.
- Potential for Data Manipulation: Some companies might inflate the ‘hours worked’ figure by including low-risk or temporary workers to artificially lower their TRIF. This manipulation undermines the metric’s reliability and can lead to misinformed safety assessments.
- Does Not Predict Future Safety Performance: Relying solely on historical TRIF data can be misleading for predicting future safety outcomes. Past low TRIF scores might encourage complacency, detracting from proactive safety measures and vigilance.
Common Total Recordable Injury Frequencies Per Industry:
While monitoring your company’s Total Recordable Injury Frequency (TRIF) can be valuable for assessing workplace safety, it’s essential to understand its limitations. The TRIF offers a snapshot of the frequency of workplace injuries but may not fully capture the complexity of safety in various industries. Consider some statistics from 2020 regarding sectors in the US with the highest TRIFs:
- Health care/social assistance: 5.5
- Agriculture, forestry, fishing, and hunting: 4.6
- Transportation and warehousing: 4.0
- Retail trade: 3.1
- Construction: 2.5
These figures might raise questions, such as why the construction industry, typically considered highly hazardous, has a lower TRIF than sectors like retail trade or agriculture. The answer lies in the nature of the TRIF calculation. The TRIF metric counts incidents without weighting the severity or potential fatality of injuries. Therefore, industries where fatalities are more common, like construction, may not appear as risky if fatalities are fewer but more severe compared to numerous minor injuries in other sectors.
Moreover, using TRIF to forecast future safety performance can be misleading. A low TRIF is encouraging, suggesting effective safety measures, but it should not lead to complacency. Safety practices must continually evolve and adapt, regardless of past TRIF scores, to mitigate risks and protect workers effectively.
Considerations When Applying TRIF Calculations:
When implementing and interpreting Total Recordable Injury Frequency (TRIF) as a metric for workplace safety, it’s crucial to consider several factors to ensure its effectiveness and reliability. Here are some key considerations:
1. Industry Variability:
- Different industries have varying levels of risk and types of injuries, which TRIF might not fully capture. It’s important to contextualize TRIF scores with industry-specific data to understand the true safety landscape.
2. Severity of Injuries:
- TRIF counts all recordable injuries equally, regardless of their severity. Consider complementing TRIF with other metrics that account for the severity and potential long-term impact of injuries, such as Lost Time Injury Frequency (LTIF) or Severity Rate.
3. Size of the Workforce:
- The size and composition of the workforce can significantly affect TRIF scores. Smaller companies might see more fluctuation in their TRIF due to fewer hours worked and less frequent but significant incidents.
4. Historical Comparison and Trends:
- While TRIF provides a snapshot of safety performance, it’s also useful to track TRIF over time to identify trends, improvements, or deteriorations in safety performance.
- Avoid relying solely on TRIF for predicting future performance. Safety conditions can rapidly change, and past scores may not always be indicative of future risks.
5. Data Integrity:
- Ensure accurate and honest reporting of all incidents and hours worked. Manipulation of data to achieve better TRIF scores can lead to misinformed decisions and potentially unsafe working conditions.
6. Use in Safety Culture:
- TRIF should be one of several tools used to promote a culture of safety. It’s a starting point for discussions and improvements, not an end goal.
- Engage employees in safety training and awareness programs that encourage reporting and proactive management of safety risks.
7. Regulatory and Compliance Aspects:
- Be aware of how TRIF and other safety metrics are viewed by regulatory bodies in your industry. Compliance with industry standards and regulations should always be a priority.
Related Articles
- All Posts
- #EmergencyPreparedness
- 2025 safety trends
- 360 Immersive
- 360immersive
- 6S Safety
- accident prevention
- accidental careers
- adjustable workstations
- adult education
- AI automation
- AI implementation
- AI in business
- AI in operations
- AI in Safety
- AI podcast
- AI strategy
- AI transformation
- Alberta safety courses
- Allan James Moore
- artificial intelligence
- asking for help
- audit findings
- audit readiness
- Audit Reporting
- automation in safety
- automation strategy
- avoidable injuries
- awareness
- Aztec Safety
- back strain
- BambooHR integration
- behavior-based safety
- Behavioral Safety
- behavioural safety
- biometric sensors
- BIS Podcast
- BIS Safety Podcasts
- BIS Safety Software
- BIS Safety Spotlight
- black holes
- Blame Culture
- BP Texas City Explosion
- Brave Leadership
- Brett Burkard
- burnout
- business automation
- Canadian OHS
- Canadian safety
- Canadian safety history
- Canadian safety standards
- carbon monoxide
- Carolynne Heron
- CCOHS
- chemical
- chemical vapors
- chronic injuries
- chronic pain
- cloud-based safety tools
- Coming Soon
- community safety programs
- Competency in Safety
- complacency in safety
- Compliance
- compliance courses
- Compliance In Canada
- compliance issues
- Compliance management
- Compliance Reporting
- compliance software
- compliance tools
- compliance tracking
- compliance training
- compliance vs protection
- Construction advocacy
- Construction education
- Construction industry
- construction safety
- construction safety training
- continuous improvement
- continuous safety improvement
- corporate culture
- corporate training
- corrective actions
- crane
- CSA standards
- Customer Spotlight
- Customer Spotlight Kevin Swinden Global Hazmat Safety Culture Hazmat Management Dangerous Goods Competency in Safety Workplace Risk Mitigation BIS Training Clients Canadian EHS
- customized training
- daily trip inspection
- Damage Prevention
- Dangerous Goods
- dangerous goods classification
- Danny Sellers
- data-driven safety
- Decision Analysis
- defect management
- defect tracking
- defensive driving
- DEI in onboarding
- digital compliance
- digital forms
- Digital Hazard Reporting
- Digital Onboarding
- digital safety
- Digital Safety Audits
- Digital safety systems
- digital safety tools
- digital safety transformation
- Digital Training Tools
- digital transformation
- DMS features
- document control
- document management system
- Dr. Joanna Pagonis
- Dr. Tom Krause
- driver file management
- driver training
- driving instructor program
- DTRMS
- e-learning
- e-learning tools
- eadership in safety
- early intervention
- education technology
- EHS
- EHS Adoption
- EHS Compliance
- EHS digital solutions
- EHS Inspections
- EHS Onboarding
- EHS software
- EHS systems
- EHS tools
- Einstein
- electrical safety
- Emergency Action Plan
- emergency preparedness
- emergency procedures
- emergency response
- emergency supplies
- emotional training
- employee behavior
- employee engagement
- employee health
- Employee onboarding
- Employee Readiness
- employee safety
- employee training
- Energy Isolation
- ergonomic consulting
- ergonomic design
- ergonomic risks
- ergonomics
- Evacuation Procedures
- evidence collection
- EWI Works
- exoskeleton
- exoskeletons
- failure analysis
- fall protection
- fast onboarding
- field experience
- field level hazard assessments
- field operations
- field safety
- field safety assessments
- field safety leadership
- field safety services
- Field Safety Technology
- Field-Friendly Software
- Fire Drills
- fire prevention
- Fire Safety Training
- first aid kit
- first week on the job
- first workplace injury
- fleet management
- fleet safety
- FLHA engagement
- FLHA Integration
- FLHA software
- FMEA
- freight
- Frontline Engagement
- frontline safety
- fuel handling
- future of work
- Global Hazmat
- global onboarding
- gravitational waves
- gut feeling in safety
- hand injuries
- handling hazardous materials
- hands-on training
- hazard analysis
- hazard assessment compliance
- Hazard Awareness
- hazard communication
- Hazard Identification
- hazard prevention
- hazard recognition
- Hazardous Energy Control
- Hazmat Management
- Health & Safety Podcast
- health and safety
- hearing loss prevention
- hearing protection
- heavy equipment safety
- hidden workplace hazards
- high voltage systems
- HR automation
- HR software
- human factors
- human factors in safety
- human in the loop
- Human Performance
- human vs machine
- human-centered design
- human-centered safety
- humor in safety
- ICBC certification
- identification
- immersive learning
- Imposter Syndrome
- incident data
- incident investigation
- incident prevention
- incident reporting
- industrial AI
- Industrial Hygiene
- industrial safety
- influence vs control
- Infrastructure Risk
- injury consequences
- injury prevention
- injury prevention tips
- injury recovery
- injury reporting
- injury response
- injury response plan
- instructor development
- internal audits
- international workforce
- interpreting safety data
- invisible dangers
- ISO standards
- Jeff Mulligan
- Jennifer Lastra
- job site accountability
- job site hazards
- job site risks
- job site safety
- jobsite readiness
- Jody Young
- KBR Safety Training
- Kevin Swinden
- labor movement
- ladder safety
- Leadership
- leadership accountability
- leadership and empathy
- Leadership in Safety
- Leadership Management
- leadership messaging
- Lean Manufacturing
- Lean Workplace
- learning from incidents
- learning management
- lifting techniques
- LIGO
- Linda Miller
- LMS
- LMS features
- LMS software
- Lock Out Tag Out
- lockout tagout
- lone workers
- LOTO
- machine learning
- Machine Safety
- Maintenance Safety
- mental health at work
- MI Safety
- microlearning
- Mike Schwartz
- minor injuries
- mobile onboarding
- Mobile Safety Apps
- Mobile Safety Platforms
- Mobile Safety Tools
- movement in workplace
- multilingual training
- MyZone AI
- Near Miss Reporting
- new hire experience
- New Hire Safety
- New Worker Training
- new workers
- no-blame investigations
- noise exposure
- nonconformance
- Northern BC
- NRCA
- NSC Standard 13
- occupational fatigue
- occupational hazards
- occupational health
- occupational safety
- occupational therapy
- OH&S
- OHS
- OHSA
- oil and gas safety
- omni-training
- onboarding safety
- Onboarding Software
- online learning
- Online safety training
- operational efficiency
- Operational Excellence
- organizational culture
- organizational safety
- OSHA compliance
- OSHA standards
- outdated practices
- overconfidence
- overhead crane courses
- pain awareness
- personal protective equipment
- Pharmaceutical Safety
- physics careers
- pipeline safety
- playbook software
- podcast
- post-accident review
- post-incident protocol
- PPE
- PPE enforcement
- PPE improvement
- pre-trip inspection
- predictive analytics
- pretrip inspection
- preventive action
- proactive safety
- proactive safety measures.
- Proactive Safety Systems
- process improvement
- Professional development
- propane safety
- propane storage
- protective clothing
- psychological hazards
- psychological safety
- quality control
- quality management
- quality standard
- Real Safety Leadership
- Real-Time Reporting
- real-time safety
- recordkeeping
- regulatory updates
- repetition in safety
- repetitive motion injuries
- respirator safety
- respirators
- risk assessment
- risk management
- risk mitigation
- risk prevention
- Risk Prevention Tools
- risk reduction
- road safety
- Robin Postnikoff
- ROI with AI
- root cause analysis
- root cause correction
- routine task risks
- safe habits
- safe transport
- safe work habits
- safety
- safety accountability
- safety advice
- safety article
- Safety Audit Software
- safety automation
- safety awareness
- safety best practices
- safety communication
- safety compliance
- Safety Conversations
- safety culture
- safety data
- safety data sheets
- safety documentation
- safety engagement
- safety follow-up
- safety gear
- safety gloves
- safety goggles
- safety habits
- safety incentives
- safety innovation
- safety insights
- safety inspection
- safety instinct
- Safety Leaders
- safety leadership
- Safety Leadership Podcast
- safety legislation
- safety lessons
- safety management
- safety management system
- safety management systems
- safety metrics
- safety mindset
- safety motivation.
- safety myths
- safety onboarding
- safety planning
- safety podcast
- safety procedure updates
- Safety Procedures
- safety professionals
- safety reporting
- safety review process
- safety shortcuts
- safety software
- Safety Spotlight
- safety systems
- safety technology
- safety theater
- safety tips
- safety training
- safety transformation
- safety transparency
- Sarah Anderson
- scalable training solutions
- Scott Lyall
- shipping documentation
- silent dangers
- silica dust
- Sinogap Solutions
- slow-building hazards
- smart helmets
- smart PPE
- smart safety systems
- smart safety tools
- SOPs
- space science
- Spencer McDonald
- Standardized Work
- storytelling and safety
- storytelling in safety
- supervisor training
- system safety
- TDG
- team communication
- teamwork
- tech and ergonomics
- tech in safety
- tech-enabled learning
- Thinking Driver
- Titan Environmental
- Total Recordable Injury Formula
- tough guy mentality
- toxic air
- training
- training courses
- Training integration
- training management
- training matrix
- training record management
- training records
- training software
- transportation
- transportation of dangerous goods
- Trust and Accountability
- unseen workplace threats
- user experience
- Utility Safety Partners
- values-based onboarding
- vehicle safety
- version control
- veteran advice
- Virtual Reality
- VR safety training
- VR Technology
- wearable technology
- WHMIS
- witness statements
- women in leadership
- work-alone training
- work-related injuries
- worker accountability
- worker advocacy
- worker fatigue
- worker protection
- worker safety
- worker safety habits
- worker safety tips
- worker trust
- worker wellbeing
- workers' rights
- Workforce Automation
- workforce compliance
- Workforce development
- workforce engagement
- workforce management
- Workforce Readiness
- workforce training
- workplace accidents
- workplace air quality
- workplace best practices
- workplace certification
- workplace compliance
- Workplace Culture
- Workplace Hazard Tracking
- workplace hazards
- workplace health
- workplace incident response
- workplace injuries
- workplace injury prevention
- workplace mindset
- Workplace Organization
- workplace risk factors
- workplace risk management
- Workplace Risk Mitigation
- Workplace safety
- workplace safety culture
- Workplace Safety Leadership
- workplace safety rules
- workplace safety tech
- workplace safety tips
- Workplace Safety Tools
- workplace safety training
- workplace stress
- workplace tiredness
- workplace wellness
- WSPS
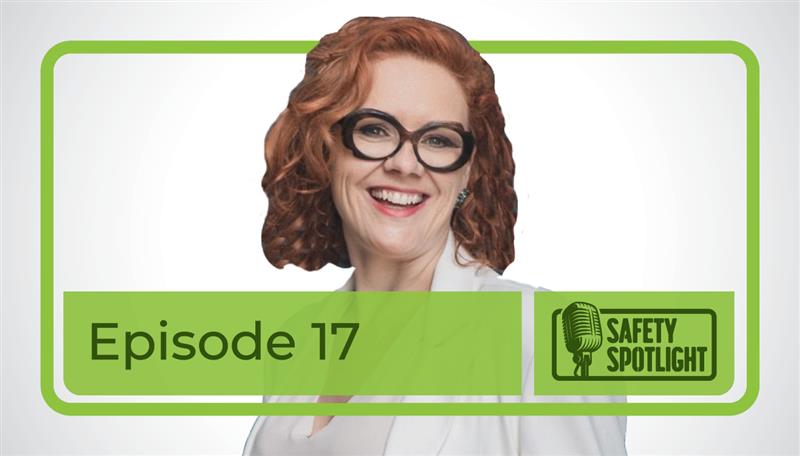
What happens when we stop treating safety as just rules and checklists, and start focusing on people, connection, and how...
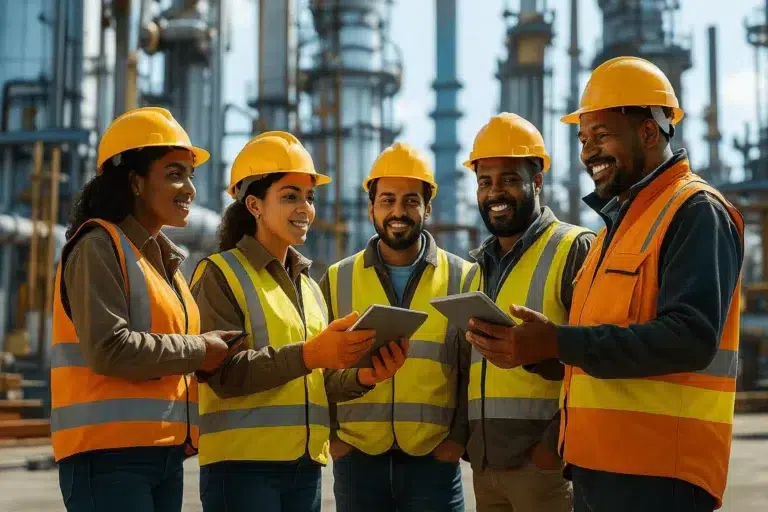
Playbook Software centralizes and standardizes safety procedures, policies, and response plans. Give your team instant access to the latest, most...
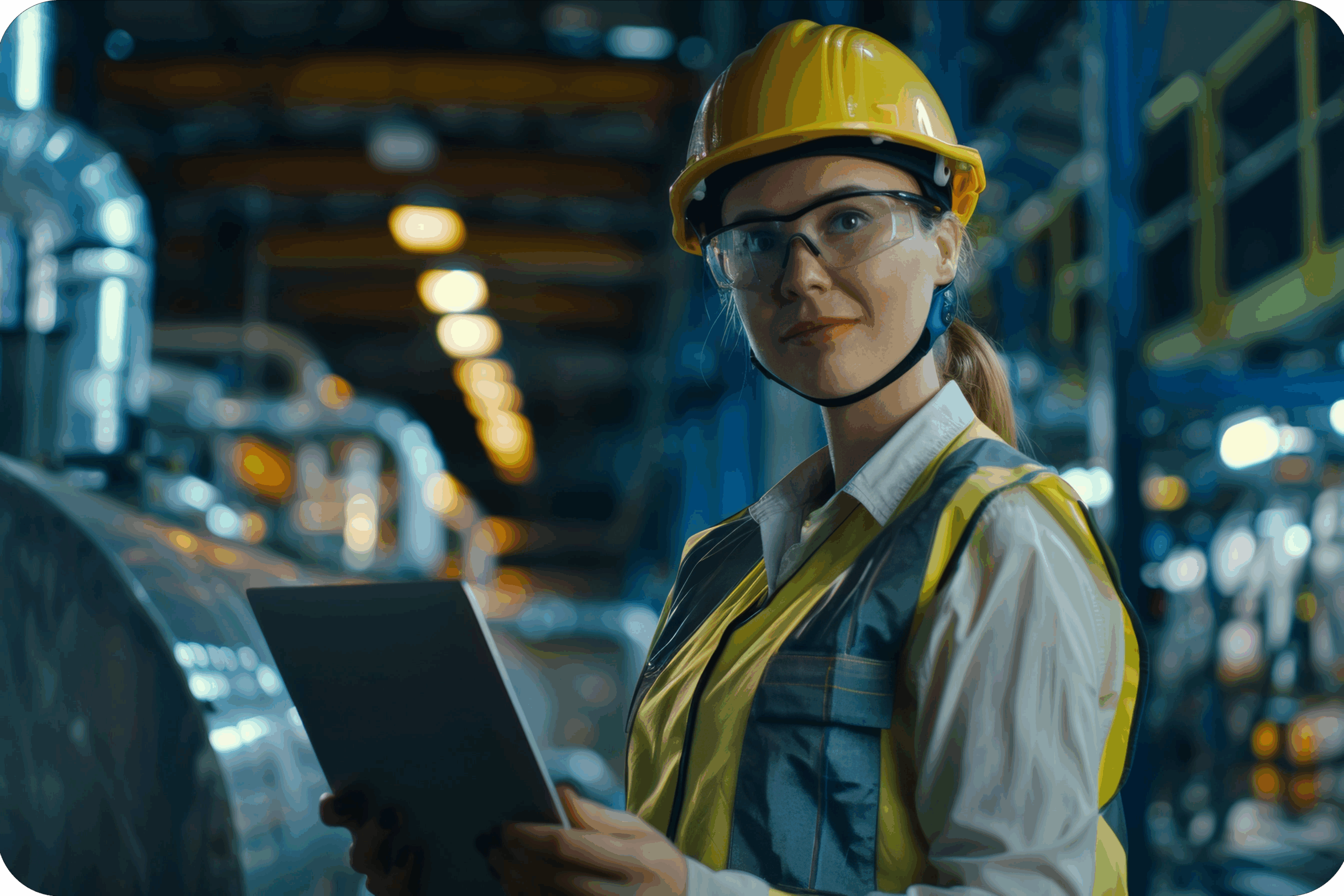
Strong, accessible documentation is key to safer, more efficient worksites. Learn why it matters, where it fails, and how to...