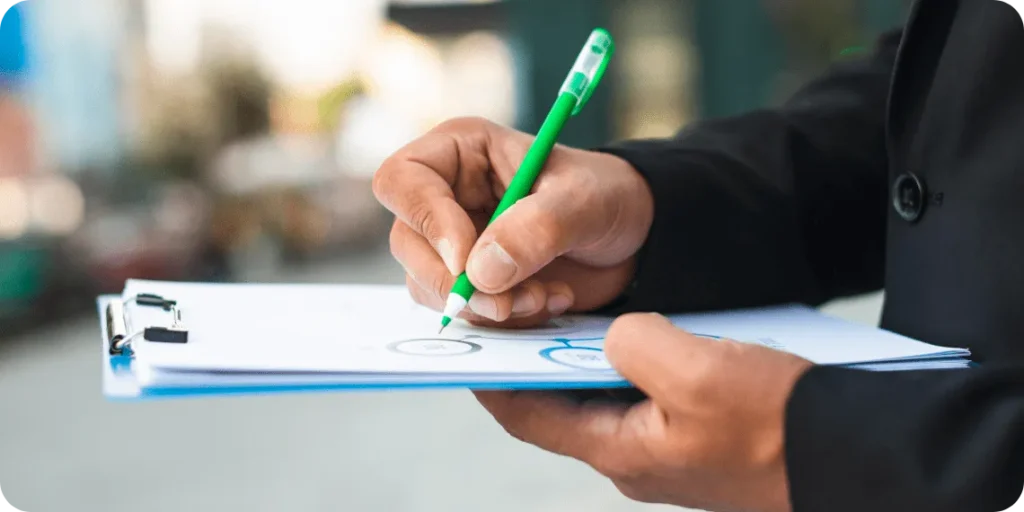
Safety audits are essential for ensuring workplace compliance and protecting employees. They bring to light the weak points in a safety program and provide actionable insights for improvement. However, common issues can derail audits, leading to penalties, operational disruptions, or worse—preventable incidents.
Avoiding these pitfalls doesn’t require perfection. It requires preparation, follow-through, and attention to detail. Here are ten common red flags auditors encounter and practical ways to address them.
1. Disorganized or Missing Documentation
The Issue: Incident reports, inspection logs, or training records are incomplete, outdated, or hard to locate.
Why It Matters: Documentation is the backbone of safety compliance. Gaps in records raise questions about whether processes are being followed consistently.
How to Address It: Store all safety-related documents in a centralized system, whether digital or physical. Automate reminders for updates to keep records current and ensure they’re easily accessible during an audit.
2. Training Records That Don’t Measure Up
The Issue: Employees have incomplete or outdated safety training records, including missed refresher courses.
Why It Matters: Training equips workers with the knowledge to manage risks effectively. Inadequate records suggest that critical skills and safety protocols may not be properly reinforced.
How to Address It: Use a Learning Management System (LMS) to track training participation and completion. Schedule refresher courses at regular intervals and focus on high-risk roles to ensure readiness across the workforce.
Key Takeaways
- Safety audits reveal your culture—not just your compliance. Messy records and repeat hazards tell a story. Make sure it’s the right one.
- Proactive systems prevent red flags. From training logs to maintenance checks, automation and structure are your best friends.
- Leadership sets the tone. When safety isn't a top-down priority, it shows—and so do the risks.
- Follow-through is everything. A strong audit isn’t just about finding issues—it’s about proving you’re fixing them.
3. Incomplete Equipment Maintenance Logs
The Issue: Maintenance records for machinery or equipment are inconsistent or nonexistent.
Why It Matters: Poorly maintained equipment increases the likelihood of accidents and signals a lack of proactive risk management.
How to Address It: Implement a maintenance tracking system to log inspections and repairs. Set up automated reminders for routine checks to prevent lapses and ensure that every piece of equipment is safe to operate.
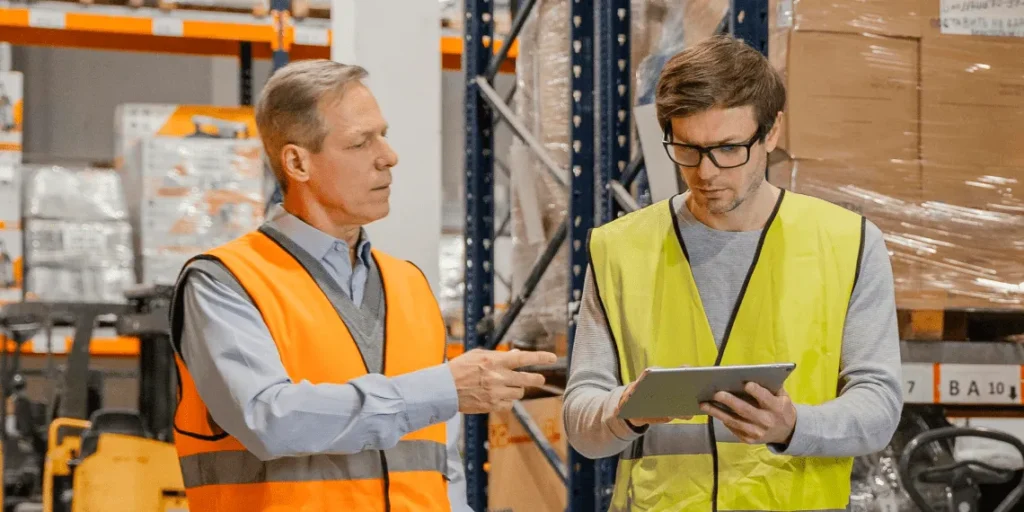
4. Lack of Reporting for Near-Misses
The Issue: Near-miss incidents are rarely reported or poorly documented.
Why It Matters: Near-misses provide a critical opportunity to address hazards before they escalate into injuries. A lack of reporting indicates potential blind spots
in risk identification.
How to Address It: Create a non-punitive reporting system that makes it easy for employees to flag near-misses. Mobile tools or simple forms can streamline the process and encourage participation.
5. PPE Non-Compliance
The Issue: Employees are either not wearing or improperly using personal protective equipment (PPE).
Why It Matters: Consistent PPE usage is fundamental to workplace safety. Visible lapses undermine compliance efforts and put workers at unnecessary risk.
How to Address It: Conduct regular safety observations to verify PPE use and reinforce training on proper practices. Signage in high-risk areas can also serve as a visual reminder.
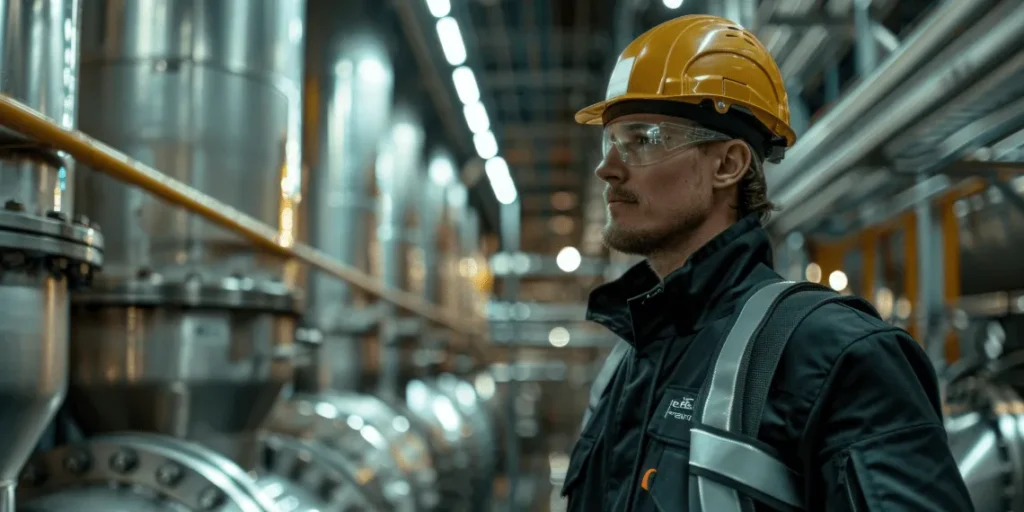
6. Emergency Plans That Are Outdated or Unpracticed
The Issue: Emergency response plans are outdated, incomplete, or haven’t been tested with drills.
Why It Matters: An unclear or untested plan can lead to confusion during emergencies, putting workers and operations at greater risk.
How to Address It: Review and update emergency plans annually. Conduct drills to test preparedness and ensure employees understand their roles and responsibilities during a crisis.
7. Hazards That Keep Reappearing
The Issue: Recurring issues identified in previous audits remain unresolved.
Why It Matters: Repeated hazards suggest a lack of accountability and undermine trust in the safety program.
How to Address It: Treat audit findings as action items with clear deadlines and responsibilities. Regularly track progress to ensure corrective actions are completed and prevent recurring issues.
8. Disengaged Leadership
The Issue: Managers and leadership are absent from safety initiatives or minimally involved in audits.
Why It Matters: Leadership involvement is critical for reinforcing a culture of safety. A lack of engagement sends a message that safety isn’t a priority.
How to Address It: Involve leaders in safety meetings, audits, and training sessions. Make safety metrics a regular part of leadership reviews to keep it on the agenda and emphasize its importance.
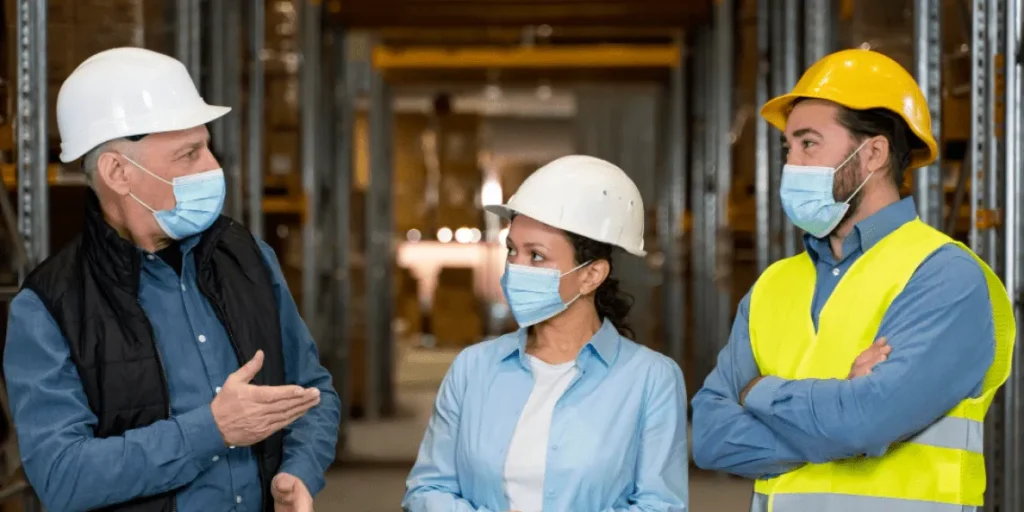
9. Poor Communication of Safety Updates
The Issue: Safety updates, protocols, or audit findings aren’t consistently shared with employees.
Why It Matters: Gaps in communication lead to confusion, reduced compliance, and repeated issues that could have been avoided with better transparency.
How to Address It: Develop a clear communication strategy for all safety updates. Use multiple channels like email, team meetings, and digital dashboards to ensure every employee stays informed. Safety software can track acknowledgment to verify employees receive critical information.
10. Neglected Audit Follow-Ups
The Issue: Recommendations from previous audits are not implemented or tracked.
Why It Matters: Ignoring audit findings demonstrates a lack of commitment to improving safety processes and creates repeated vulnerabilities.
How to Address It: Turn audit recommendations into actionable plans. Assign accountability for each task, set deadlines, and track progress until every item is resolved.
How Safety Software Helps You Stay Ahead
Preparing for audits doesn’t have to be an overwhelming task. Safety management software simplifies the process by automating key compliance requirements and centralizing data.
Key Features to Look For:
- Centralized Dashboards: Consolidate all safety data for quick access during audits.
- Automated Alerts: Stay on top of training, inspections, and maintenance schedules.
- Audit-Ready Reporting: Generate detailed reports that meet compliance standards with minimal effort.
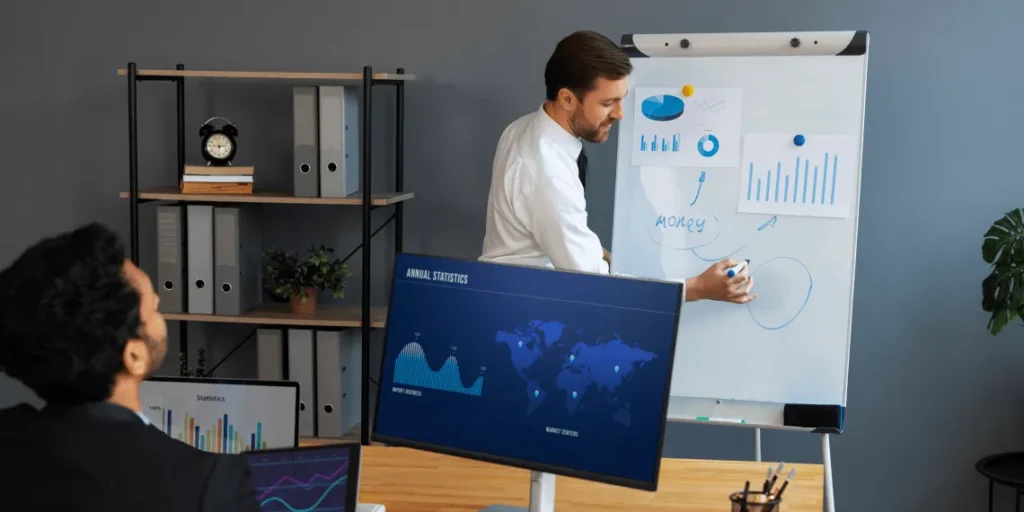
The Bottom Line: Audit Preparation Simplified
Safety audits are opportunities to demonstrate your organization’s dedication to protecting employees and maintaining compliance. Avoiding common red flags requires consistent follow-through, organized documentation, and proactive leadership.
By addressing these issues and leveraging the right tools, you can streamline the audit process, improve safety outcomes, and build a culture of accountability.
Preparation starts now—because the best way to succeed is to always be ready.
Related Articles
- All Posts
- 360 Immersive
- 360immersive
- accident prevention
- Alberta safety courses
- Allan James Moore
- asking for help
- avoidable injuries
- awareness
- back strain
- BambooHR integration
- biometric sensors
- BIS Podcast
- BIS Safety Software
- black holes
- Brave Leadership
- burnout
- Canadian safety history
- carbon monoxide
- CCOHS
- chemical
- chemical vapors
- chronic injuries
- chronic pain
- Coming Soon
- community safety programs
- Compliance
- compliance courses
- compliance tools
- compliance vs protection
- Construction advocacy
- Construction education
- Construction industry
- construction safety training
- continuous safety improvement
- crane
- customized training
- daily trip inspection
- Danny Sellers
- data-driven safety
- digital forms
- Dr. Joanna Pagonis
- driver file management
- driver training
- early intervention
- EHS
- Einstein
- electrical safety
- emergency preparedness
- emergency response
- emergency supplies
- emotional training
- employee health
- employee safety
- employee training
- ergonomic risks
- ergonomics
- evidence collection
- exoskeletons
- fall protection
- field safety
- field safety services
- fire prevention
- first aid kit
- first week on the job
- first workplace injury
- fleet management
- frontline safety
- gravitational waves
- hand injuries
- hands-on training
- hazard communication
- hazard prevention
- hazard recognition
- Health & Safety Podcast
- hearing loss prevention
- heavy equipment safety
- hidden workplace hazards
- high voltage systems
- HR automation
- HR software
- human-centered safety
- humor in safety
- immersive learning
- Imposter Syndrome
- incident data
- incident investigation
- incident reporting
- industrial safety
- injury consequences
- injury prevention
- injury prevention tips
- injury recovery
- injury reporting
- injury response
- injury response plan
- internal audits
- invisible dangers
- Jennifer Lastra
- job site hazards
- job site risks
- job site safety
- Jody Young
- KBR Safety Training
- labor movement
- ladder safety
- Leadership
- leadership accountability
- leadership and empathy
- learning from incidents
- lifting techniques
- LIGO
- LMS
- lockout tagout
- lone workers
- mental health at work
- MI Safety
- minor injuries
- new workers
- no-blame investigations
- noise exposure
- Northern BC
- NRCA
- NSC Standard 13
- occupational fatigue
- occupational hazards
- occupational health
- occupational safety
- OHSA
- oil and gas safety
- onboarding safety
- Online safety training
- organizational safety
- OSHA compliance
- OSHA standards
- overhead crane courses
- pain awareness
- personal protective equipment
- physics careers
- pipeline safety
- podcast
- post-accident review
- post-incident protocol
- PPE
- PPE enforcement
- PPE improvement
- pre-trip inspection
- pretrip inspection
- proactive safety measures.
- Professional development
- psychological hazards
- psychological safety
- repetitive motion injuries
- respirator safety
- risk management
- risk reduction
- road safety
- Robin Postnikoff
- root cause analysis
- routine task risks
- safe work habits
- safety
- safety accountability
- safety advice
- safety article
- safety awareness
- safety best practices
- safety communication
- safety compliance
- Safety Conversations
- safety culture
- safety engagement
- safety follow-up
- safety gear
- safety habits
- safety innovation
- safety insights
- safety inspection
- Safety Leaders
- safety leadership
- safety legislation
- safety lessons
- safety management
- safety management system
- safety metrics
- safety motivation.
- safety myths
- safety podcast
- safety procedure updates
- safety review process
- safety shortcuts
- Safety Spotlight
- safety systems
- safety technology
- safety theater
- safety tips
- safety training
- safety transparency
- silent dangers
- silica dust
- Sinogap Solutions
- slow-building hazards
- smart helmets
- space science
- supervisor training
- team communication
- teamwork
- Total Recordable Injury Formula
- tough guy mentality
- toxic air
- training
- training courses
- training matrix
- training record management
- transportation
- Trust and Accountability
- unseen workplace threats
- vehicle safety
- veteran advice
- Virtual Reality
- VR safety training
- VR Technology
- wearable technology
- WHMIS
- witness statements
- women in leadership
- work-alone training
- work-related injuries
- worker accountability
- worker advocacy
- worker fatigue
- worker protection
- worker safety
- worker safety habits
- worker trust
- workers' rights
- workforce management
- workforce training
- workplace accidents
- workplace air quality
- workplace best practices
- workplace certification
- Workplace Culture
- workplace hazards
- workplace health
- workplace incident response
- workplace injuries
- workplace injury prevention
- workplace mindset
- workplace risk factors
- workplace risk management
- Workplace safety
- workplace safety culture
- workplace safety rules
- workplace safety tips
- workplace safety training
- workplace stress
- workplace tiredness
- workplace wellness
- WSPS
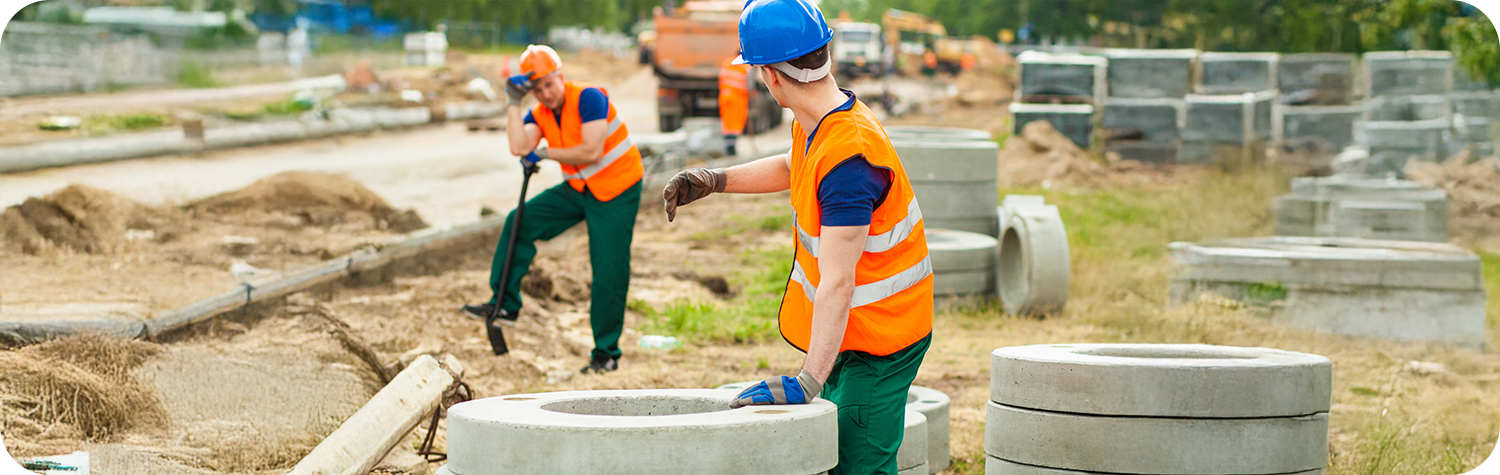
Too many workers risk injury by refusing help to appear tough. This article explains how asking for help and supporting...
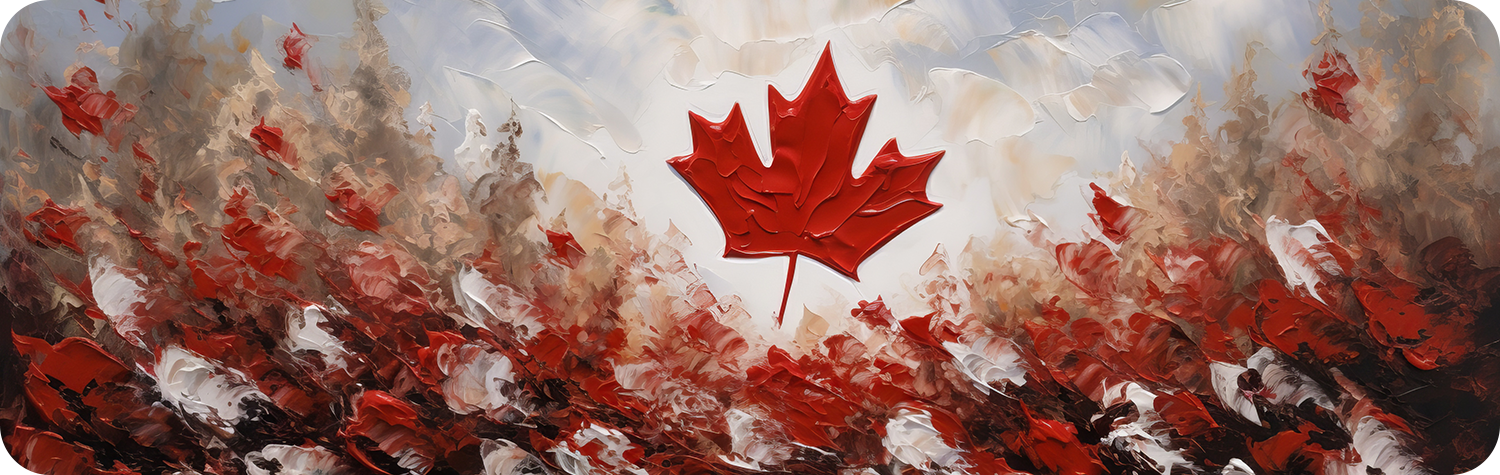
Canada’s safety standards weren’t handed down—they were hard-won. This article explores the rise of workplace safety from the early industrial...
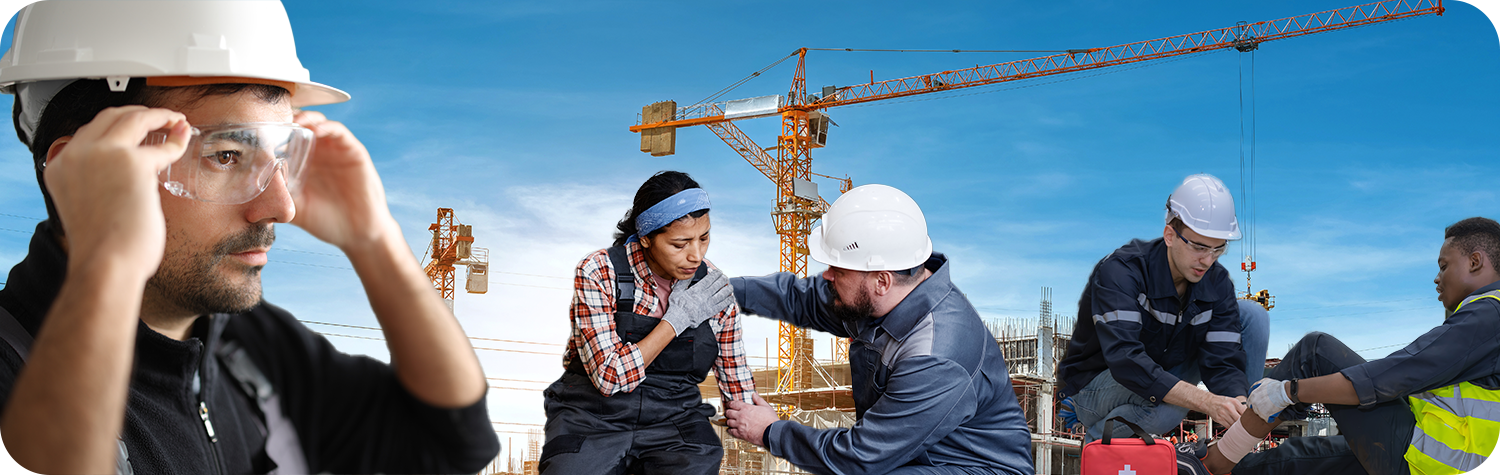
Workplace safety cultures fall into three categories: the good, the bad, and the ugly. Some organizations set the gold standard...