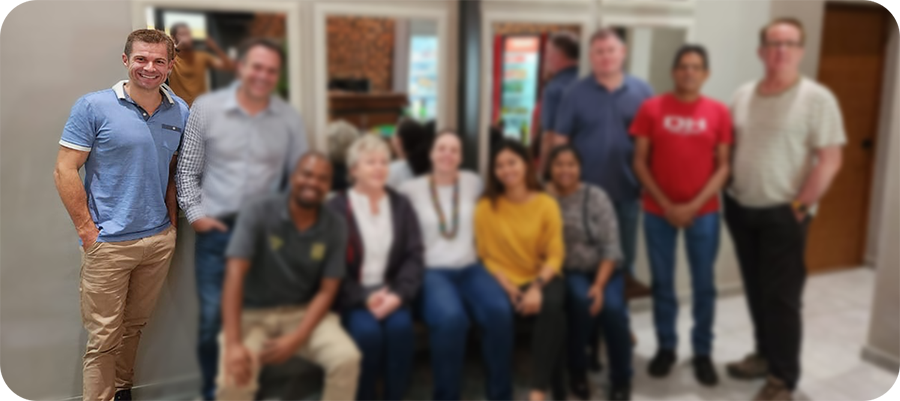
How Alex Hollingsworth Transformed Safety for 20,000 Workers
Background and Expertise
When Alex Hollingsworth joined South32 in 2022 as Manager of Group Training and Learning, he brought with him a wealth of experience in learning and development. His role required navigating the complexities of decentralized operations across Australia, South Africa, and the Americas—regions with vastly different regulatory landscapes, cultural contexts, and operational challenges.
—————————————————————————
“It’s about building safety systems together so that everyone involved
can be proud of the achievement and processes that make safety intuitive and achievable for everyone involved.”
—————————————————————————
In South Africa, Alex faced the challenge of adhering to stringent government legislation policies and training requirements that were unique to the region. Safety regulations were often deeply influenced by local labor laws, and the diversity of languages and cultural expectations added another layer of complexity. “In South Africa, you have to account for a workforce that speaks multiple languages, each with their own nuances, while ensuring compliance with highly specific training requirements,” Alex shared.
In Australia, where open-cut mining operations have dominated for decades, the focus for achieving safety performance with the power of digital transformation, was on ensuring seamless integration with legacy processes in a way that brought the workforce along for the journey.
Meanwhile, in the Americas, the challenges varied widely depending on whether the project was a well-established site or an emerging greenfield operation. In some areas, Alex’s focus was on building training programs from the ground up, ensuring that safety was embedded into every stage of development.
“At South32, I learned that no two regions are the same,” Alex explained. “The key was finding a balance between respecting local differences and maintaining a globally unified approach to safety. It’s about building systems and processes that make safety intuitive and achievable for everyone involved.”
This ability to adapt and lead across such diverse landscapes highlights Alex’s exceptional skill in fostering a global safety culture that remains effective no matter the regional challenges.
—————————————————————————
“Training isn’t something you set and forget. Every change—from new equipment to organizational structural shifts—requires reassessing and realigning on capability requirements.”
—————————————————————————
Lessons from Rio Tinto: A Foundation for Excellence
Before joining South32, Alex Hollingsworth spent 16 years with Rio Tinto, one of the world’s largest and most complex mining operations. During his tenure, Alex rose to the position of Senior Manager of Learning and Development, a role that involved overseeing training initiatives for thousands of workers across the globe.
“Rio Tinto’s iron ore network is the largest and most profitable single mining operation in the world,” Alex shared. “Managing training in such a high-stakes environment required setting an effective framework for the deployment of consistent and efficient training solutions balancing global consistency with local flexibility.”
To achieve this, Alex led a decentralized training model, where training operational teams partnered with operations tailored execution on identifying specific capability requirements and then delivered through a centralized framework to meet specific and local operations strategy requirements regional needs while adhering to global standards. This approach ensured uniform safety practices while addressing the specific challenges of individual sites, from environmental hazards to cultural and regulatory differences.
In managing such complexities, flexible and scalable software applications became indispensable. These tools allowed global companies like Rio Tinto to maintain oversight, ensure compliance, and streamlining of training across diverse regions. Few solutions on the market are capable of managing both the global and local demands of safety and training, making adaptable software an essential part of any safety strategy.
Key responsibilities during his time at Rio Tinto included:
- Developing High-Value Training Strategies:
Alex crafted comprehensive strategies to ensure consistency in safety and operational training across multiple continents. - Fostering a Culture of Safety:
Alex prioritized making safety a shared value across all teams, empowering workers to take ownership of their practices. “Safety isn’t just a policy; it’s a mindset,” Alex explained. His focus on collaboration created a unified approach to safety, strengthening practices across diverse sites. - Leading through Change:
As new technologies and regulatory frameworks emerged, Alex led initiatives to integrate them into training programs, ensuring Rio Tinto remained at the forefront of safety innovation.
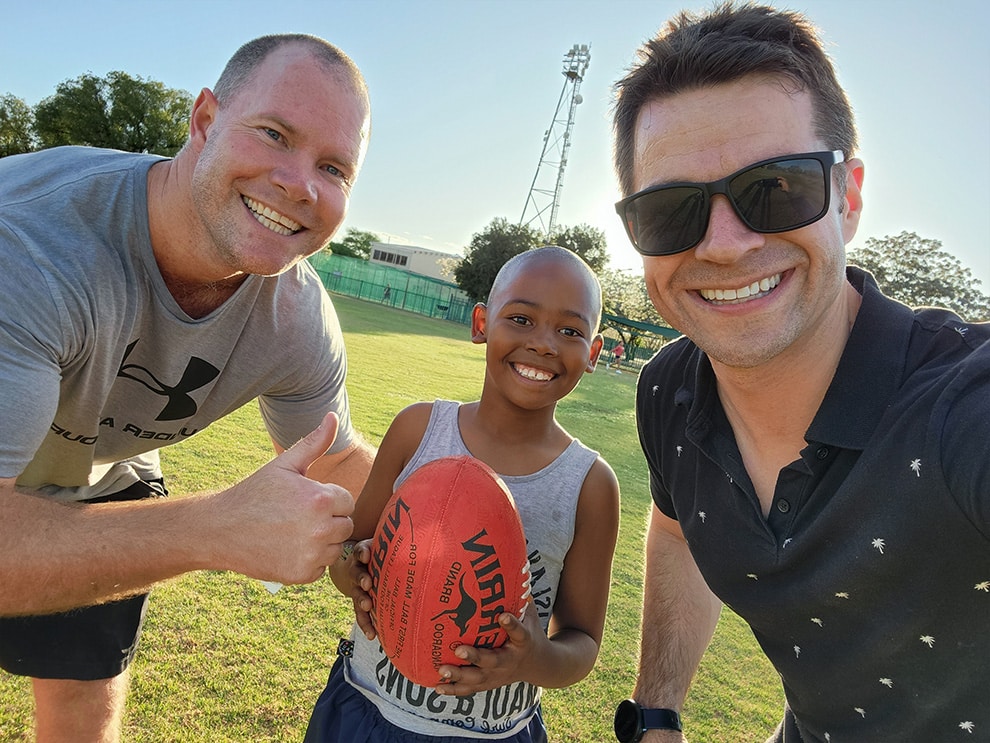
—————————————————————————
“Rio Tinto prepared me to think big, act decisively, and never lose sight of the people behind the numbers. That focus on people—ensuring every worker is safe and supported—has been at the core of everything I do.“
—————————————————————————
This foundation proved invaluable when Alex transitioned to South32, where he applied the lessons learned at Rio Tinto to tackle new challenges in safety management. His ability to navigate complexity, implement large-scale strategies, and foster collaboration positioned him as a transformative leader in the safety training industry.
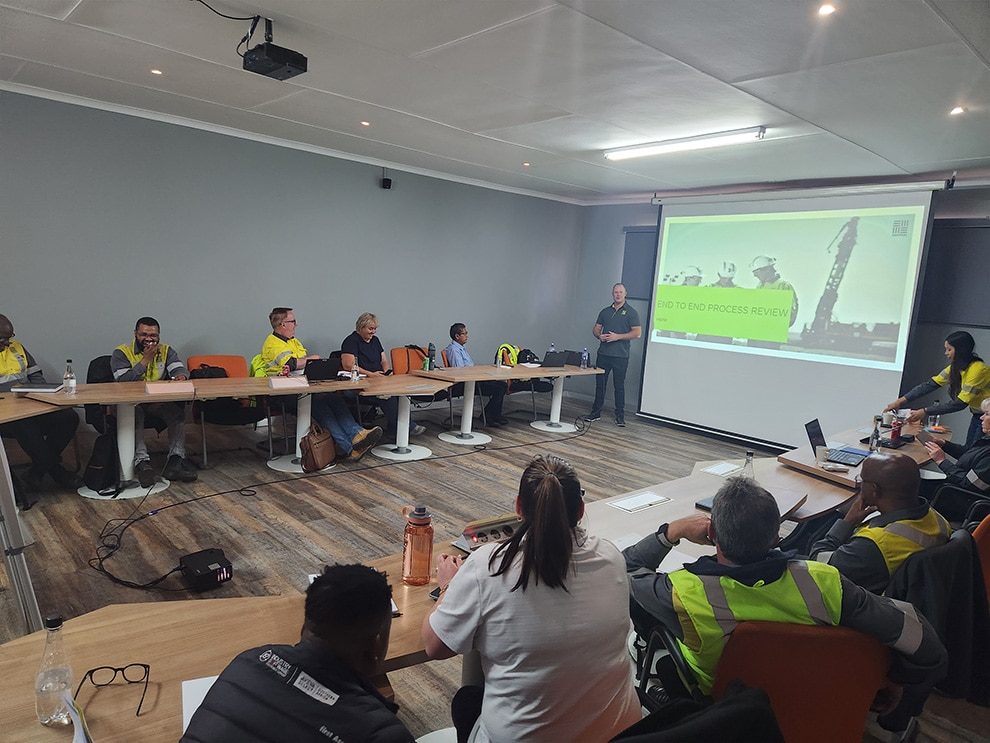
Challenges in Safety Management
Imagine managing safety for 20,000 workers, including 10,000 contractors, spread across multiple continents, each with its own set of regulations, environmental challenges, and cultural norms. For Alex Hollingsworth, this was the reality at South32. It was a role that demanded more than just technical expertise—it required innovation, persistence, and the ability to lead through complexity.
One of the most pressing challenges Alex faced was the company’s reliance on paper-based processes for managing training and certifications. “We printed 150,000 sheets of paper monthly for training documentation,” Alex explained. “It was highly error-prone and laborious, leading to low confidence in our systems.” Picture towering stacks of paper—training sign-off sheets, certifications, competency records—each representing hours of manual effort. A gust of wind, a spilled coffee, or simple human error could set the process back, causing delays and disruptions.
But inefficiencies in documentation were only part of the problem. The sheer scale of operations meant navigating a labyrinth of regulatory requirements, each unique to the jurisdictions where South32 operated. Ensuring compliance wasn’t just a logistical challenge; it was a critical aspect of maintaining worker safety and avoiding operational shutdowns.
Another significant hurdle was managing the competency of external contractors, who made up half of the workforce. “With our employees, we could set training and competency standards internally,” Alex said. “But for contractors, it was much harder to track their qualifications and ensure they met our safety standards.” This lack of visibility posed a major risk, as unqualified workers could inadvertently create hazardous situations.
Despite these challenges, Alex saw an opportunity to not only modernize systems but to rebuild confidence in the organization’s safety training processes. “It wasn’t just about fixing inefficiencies,” he reflected. “It was about creating a system that everyone—from leadership to frontline workers—could trust.”
This trust would become the cornerstone of the transformation Alex would lead, paving the way for a safer, more efficient future at South32.
Transition to Digital Solutions
- Cost Efficiency: Ensuring the solution was financially sustainable.
- Integration: Seamlessly connecting medical, gate access, and learning systems.
- Sustainability: Building a system that could evolve with the organization’s needs.
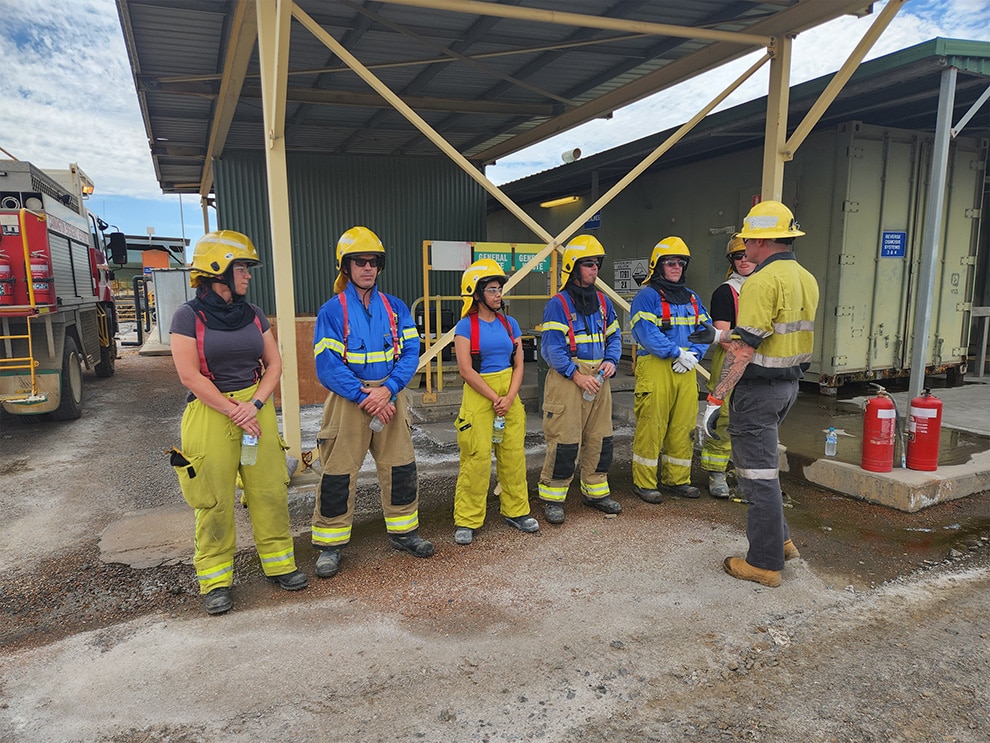
Alex’s Leadership Insights
For Alex Hollingsworth, safety leadership was as much about mindset as it was about strategy. His approach emphasized adaptability and continuous cultural improvement, recognizing that safety is a dynamic field requiring constant attention. “Training isn’t something you set and forget,” Alex said. “Every change—from new equipment to organizational structural shifts—requires reassessing and realigning on capability requirements.”
This philosophy underpinned Alex’s leadership style. He understood that effective safety training management meant not just reacting to change but anticipating it. Whether integrating new technologies or addressing shifts in workforce dynamics, Alex believed in proactive measures to ensure teams were always prepared.
Beyond systems and policies, Alex championed a culture of accountability. He encouraged teams to take ownership of their safety training and actively participate in the continuous evolution of processes. “The key is creating an environment where safety isn’t just a requirement—it’s a shared value,” Alex reflected.
Through this commitment to improvement, Alex inspired others to view safety as a collective responsibility, fostering resilience and readiness across South32’s global operations.
Conclusion
Alex Hollingsworth’s journey in the safety and training industry highlights the importance of vision, adaptability, and continuous improvement. His work at South32 not only transformed safety training processes but also set a new standard for innovation in global safety management.
One of Alex’s lasting contributions is the understanding that safety is a cultural journey, not a destination. By embracing digital transformation and focusing on real-world results, Alex has shown how the right tools and mindset can create safer, more efficient workplaces and people at work.
As Alex moves on to the next chapter of his career, his dedication to advancing safety practices leaves a lasting impact.
Related Articles
- All Posts
- 360 Immersive
- 360immersive
- accident prevention
- Alberta safety courses
- Allan James Moore
- asking for help
- avoidable injuries
- awareness
- back strain
- BambooHR integration
- biometric sensors
- BIS Podcast
- BIS Safety Software
- black holes
- Brave Leadership
- burnout
- Canadian safety history
- carbon monoxide
- CCOHS
- chemical
- chemical vapors
- chronic injuries
- chronic pain
- Coming Soon
- community safety programs
- Compliance
- compliance courses
- compliance tools
- compliance vs protection
- Construction advocacy
- Construction education
- Construction industry
- construction safety training
- continuous safety improvement
- crane
- customized training
- daily trip inspection
- Danny Sellers
- data-driven safety
- digital forms
- Dr. Joanna Pagonis
- driver file management
- driver training
- early intervention
- EHS
- Einstein
- electrical safety
- emergency preparedness
- emergency response
- emergency supplies
- emotional training
- employee health
- employee safety
- employee training
- ergonomic risks
- ergonomics
- evidence collection
- exoskeletons
- fall protection
- field safety
- field safety services
- fire prevention
- first aid kit
- first week on the job
- first workplace injury
- fleet management
- frontline safety
- gravitational waves
- hand injuries
- hands-on training
- hazard communication
- hazard prevention
- hazard recognition
- Health & Safety Podcast
- hearing loss prevention
- heavy equipment safety
- hidden workplace hazards
- high voltage systems
- HR automation
- HR software
- human-centered safety
- humor in safety
- immersive learning
- Imposter Syndrome
- incident data
- incident investigation
- incident reporting
- industrial safety
- injury consequences
- injury prevention
- injury prevention tips
- injury recovery
- injury reporting
- injury response
- injury response plan
- internal audits
- invisible dangers
- Jennifer Lastra
- job site hazards
- job site risks
- job site safety
- Jody Young
- KBR Safety Training
- labor movement
- ladder safety
- Leadership
- leadership accountability
- leadership and empathy
- learning from incidents
- lifting techniques
- LIGO
- LMS
- lockout tagout
- lone workers
- mental health at work
- MI Safety
- minor injuries
- new workers
- no-blame investigations
- noise exposure
- Northern BC
- NRCA
- NSC Standard 13
- occupational fatigue
- occupational hazards
- occupational health
- occupational safety
- OHSA
- oil and gas safety
- onboarding safety
- Online safety training
- organizational safety
- OSHA compliance
- OSHA standards
- overhead crane courses
- pain awareness
- personal protective equipment
- physics careers
- pipeline safety
- podcast
- post-accident review
- post-incident protocol
- PPE
- PPE enforcement
- PPE improvement
- pre-trip inspection
- pretrip inspection
- proactive safety measures.
- Professional development
- psychological hazards
- psychological safety
- repetitive motion injuries
- respirator safety
- risk management
- risk reduction
- road safety
- Robin Postnikoff
- root cause analysis
- routine task risks
- safe work habits
- safety
- safety accountability
- safety advice
- safety article
- safety awareness
- safety best practices
- safety communication
- safety compliance
- Safety Conversations
- safety culture
- safety engagement
- safety follow-up
- safety gear
- safety habits
- safety innovation
- safety insights
- safety inspection
- Safety Leaders
- safety leadership
- safety legislation
- safety lessons
- safety management
- safety management system
- safety metrics
- safety motivation.
- safety myths
- safety podcast
- safety procedure updates
- safety review process
- safety shortcuts
- Safety Spotlight
- safety systems
- safety technology
- safety theater
- safety tips
- safety training
- safety transparency
- silent dangers
- silica dust
- Sinogap Solutions
- slow-building hazards
- smart helmets
- space science
- supervisor training
- team communication
- teamwork
- Total Recordable Injury Formula
- tough guy mentality
- toxic air
- training
- training courses
- training matrix
- training record management
- transportation
- Trust and Accountability
- unseen workplace threats
- vehicle safety
- veteran advice
- Virtual Reality
- VR safety training
- VR Technology
- wearable technology
- WHMIS
- witness statements
- women in leadership
- work-alone training
- work-related injuries
- worker accountability
- worker advocacy
- worker fatigue
- worker protection
- worker safety
- worker safety habits
- worker trust
- workers' rights
- workforce management
- workforce training
- workplace accidents
- workplace air quality
- workplace best practices
- workplace certification
- Workplace Culture
- workplace hazards
- workplace health
- workplace incident response
- workplace injuries
- workplace injury prevention
- workplace mindset
- workplace risk factors
- workplace risk management
- Workplace safety
- workplace safety culture
- workplace safety rules
- workplace safety tips
- workplace safety training
- workplace stress
- workplace tiredness
- workplace wellness
- WSPS
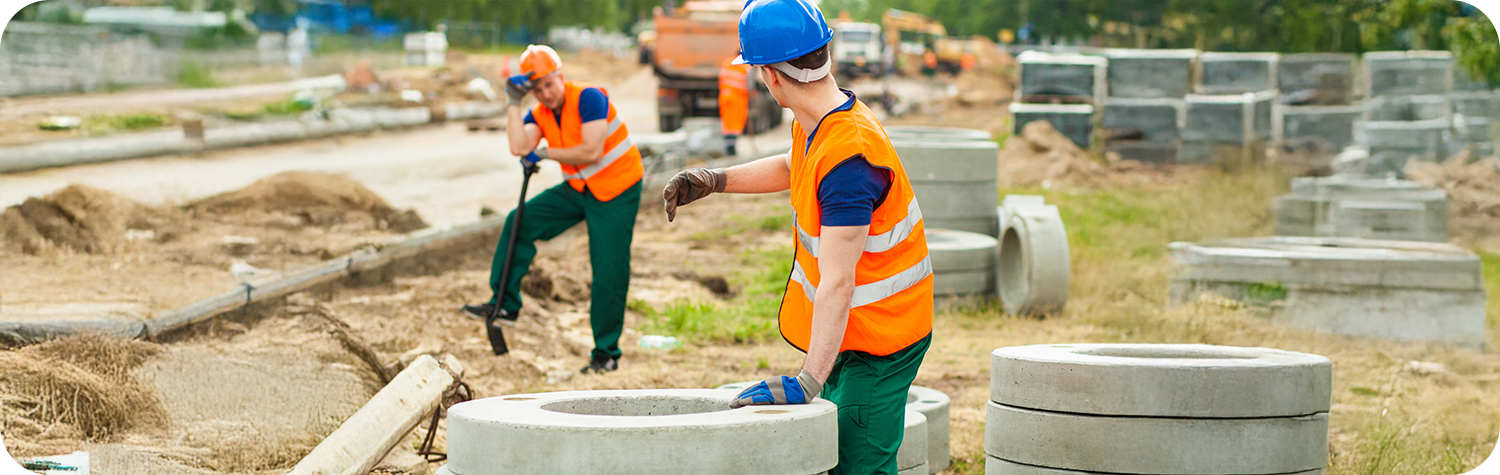
Too many workers risk injury by refusing help to appear tough. This article explains how asking for help and supporting...
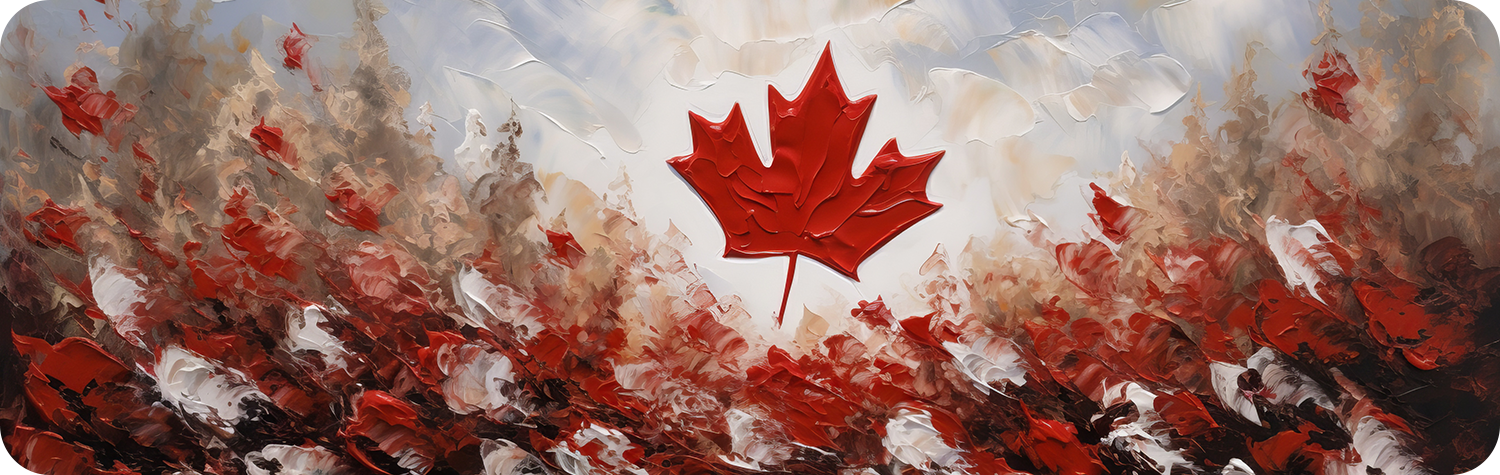
Canada’s safety standards weren’t handed down—they were hard-won. This article explores the rise of workplace safety from the early industrial...
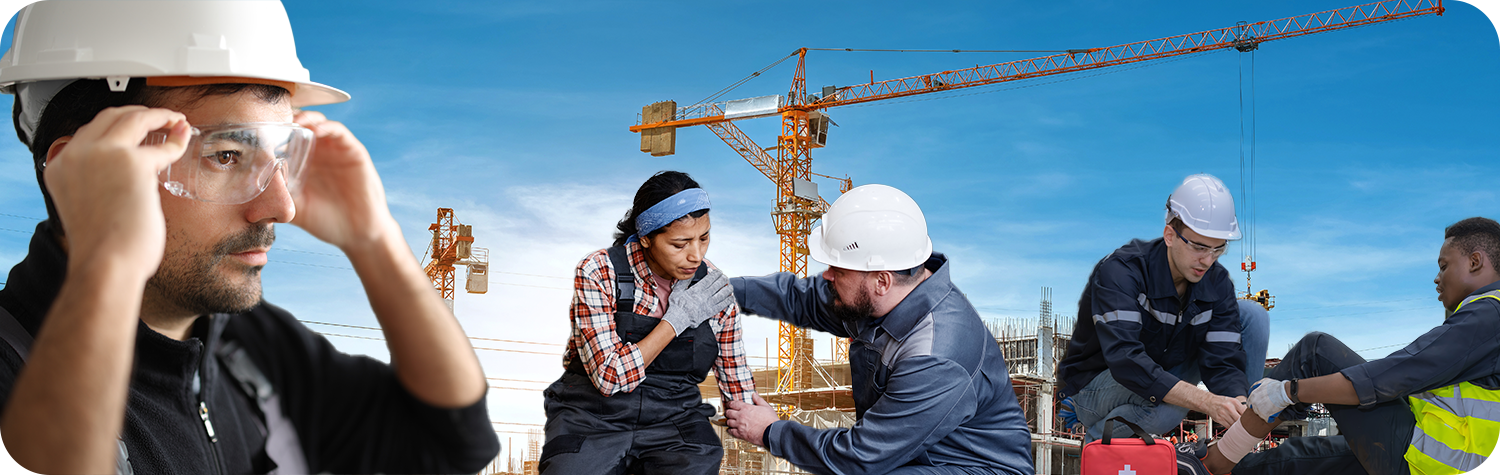
Workplace safety cultures fall into three categories: the good, the bad, and the ugly. Some organizations set the gold standard...